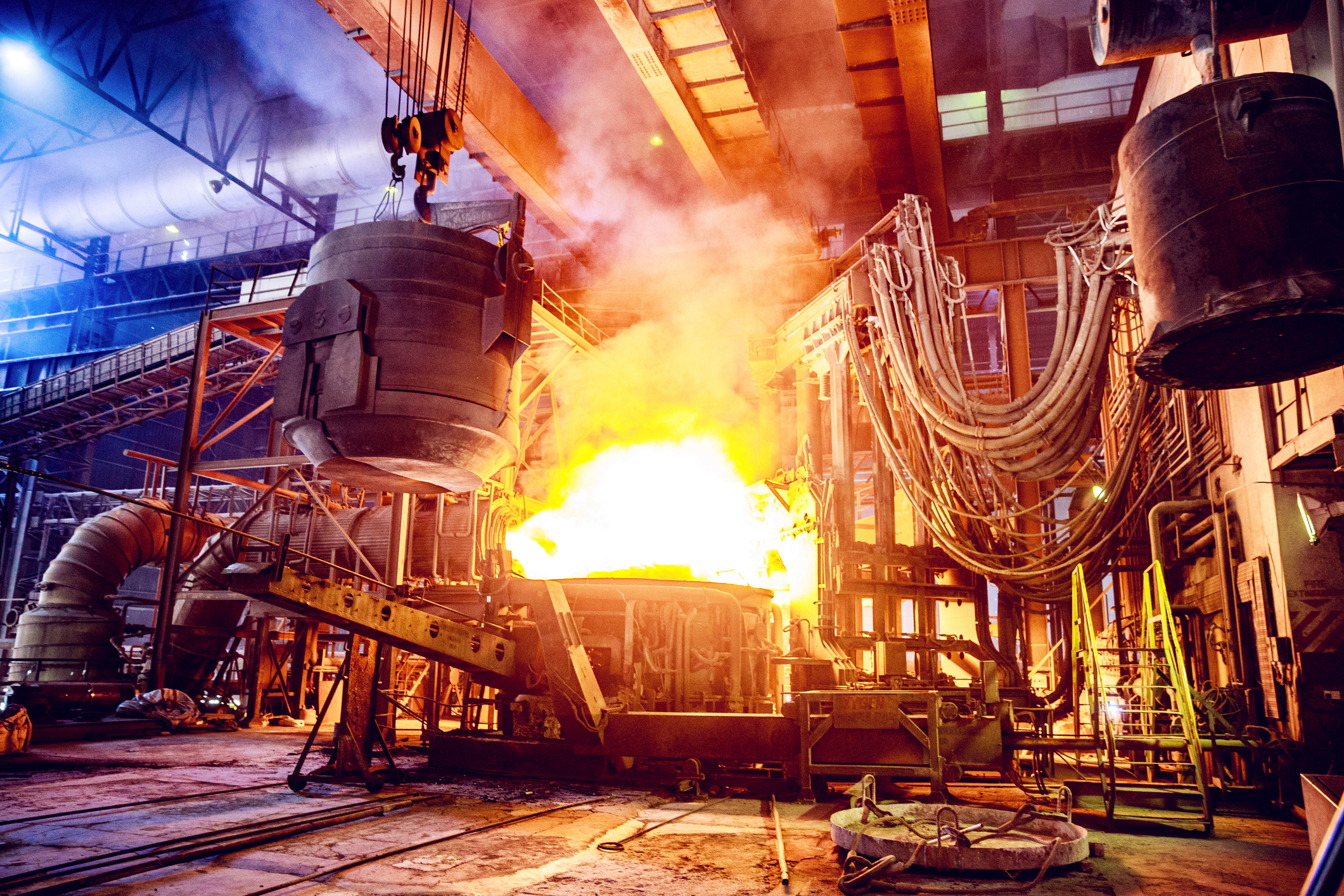
EPDM (Ethylene Propylene) Selection Guide
EP elastomers, O-rings, gaskets, & custom molded parts contain copolymers of ethylene and propylene with some added substances in certain compounds. EPDM materials, O-rings, gaskets, & custom molded parts can operate over a wide temperature range, and are compatible with glycol fluids that cause problems for most typical elastomeric seals. However, ethylene-propylene O-rings, gaskets, & custom molded parts swell easily when exposed to hydrocarbons such as mineral oil and grease. Due to its compatibility with glycol fluids, EP O-rings, gaskets, & custom molded parts are used in the automotive, aerospace, and other industries where hydraulic fluids and braking fluids are common.
Common names include: EPDM (Ethylene-propylene diene monomer), EP Trade Names: Nordel®, Epcar®, Epsyn®, Vistalon®, Royalene®, Vistalon®
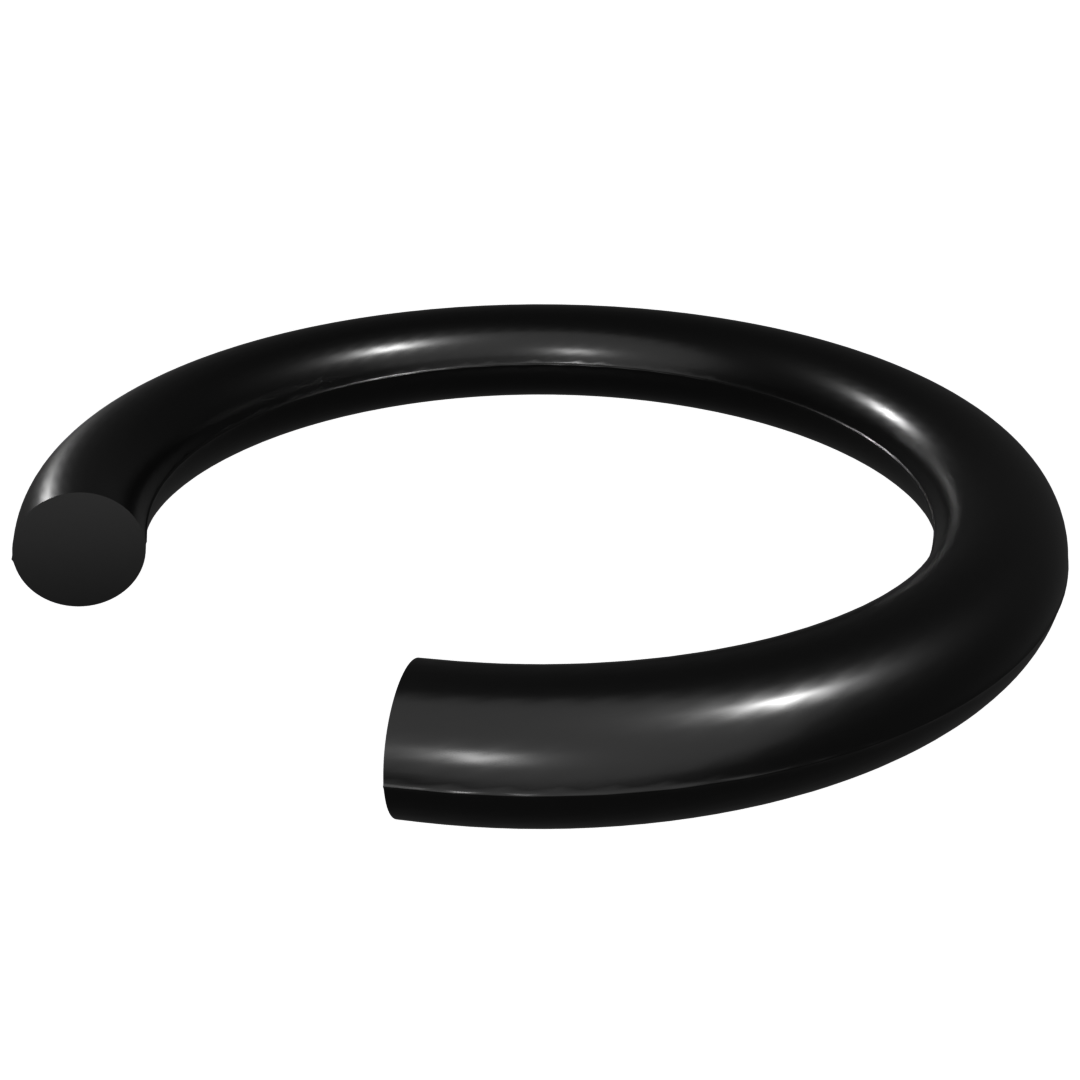
Features of EPDM
- EPDM O-rings, gaskets, & custom molded parts have excellent resistance to alcohols, glycol, engine coolant, braking fluids and hydraulic fluids such as Skydrol
- Specific blends of EPDM are rated for Nuclear Use. To learn more, see our Nuclear Grade EPDM page.
- Some EPDM is USP Class VI tested for medical applications and pharmaceutical manufacturing. To learn more, see our USP Class VI EPDM page.
- EPDM O-rings, gaskets, & custom molded parts have good resistance to heat and compression
- EPDM O-rings, gaskets, & custom molded parts have good resistance to steam and hot water
- EPDM O-rings, gaskets, & custom molded parts have good resistance to ketones, alkalis, polar solvents
- EPDM O-rings, gaskets, & custom molded parts have good resistance to ozone, sunlight, and aging
- EPDM O-rings, gaskets, & custom molded parts are available in multiple compounds to meet performance and cost requirements
Limitations of EPDM
- EPDM O-rings, gaskets, & custom molded parts have poor performance when in contact with oils, gasoline, kerosene, aromatic and aliphatic hydrocarbon, halogenated solvents, concentrated acids, non-polar solvents, petroleum oils and aromatic fuels.
- EPDM O-rings, gaskets, & custom molded parts have a Service Temperature Range of (varies with application): -65°F to 302°F (-54°C to 150°C)
Please consult a Canyon Components Engineer about your specific application and we will use our decades of experience to formulate a solution that fits your need.
EPDM Materials Available
This table shows many of our standard materials and links out to our O-ring store. Get in touch with us if you need a custom gasket, custom molded part, or non-standard geometry!
Filter by
Temperature Search (°C)
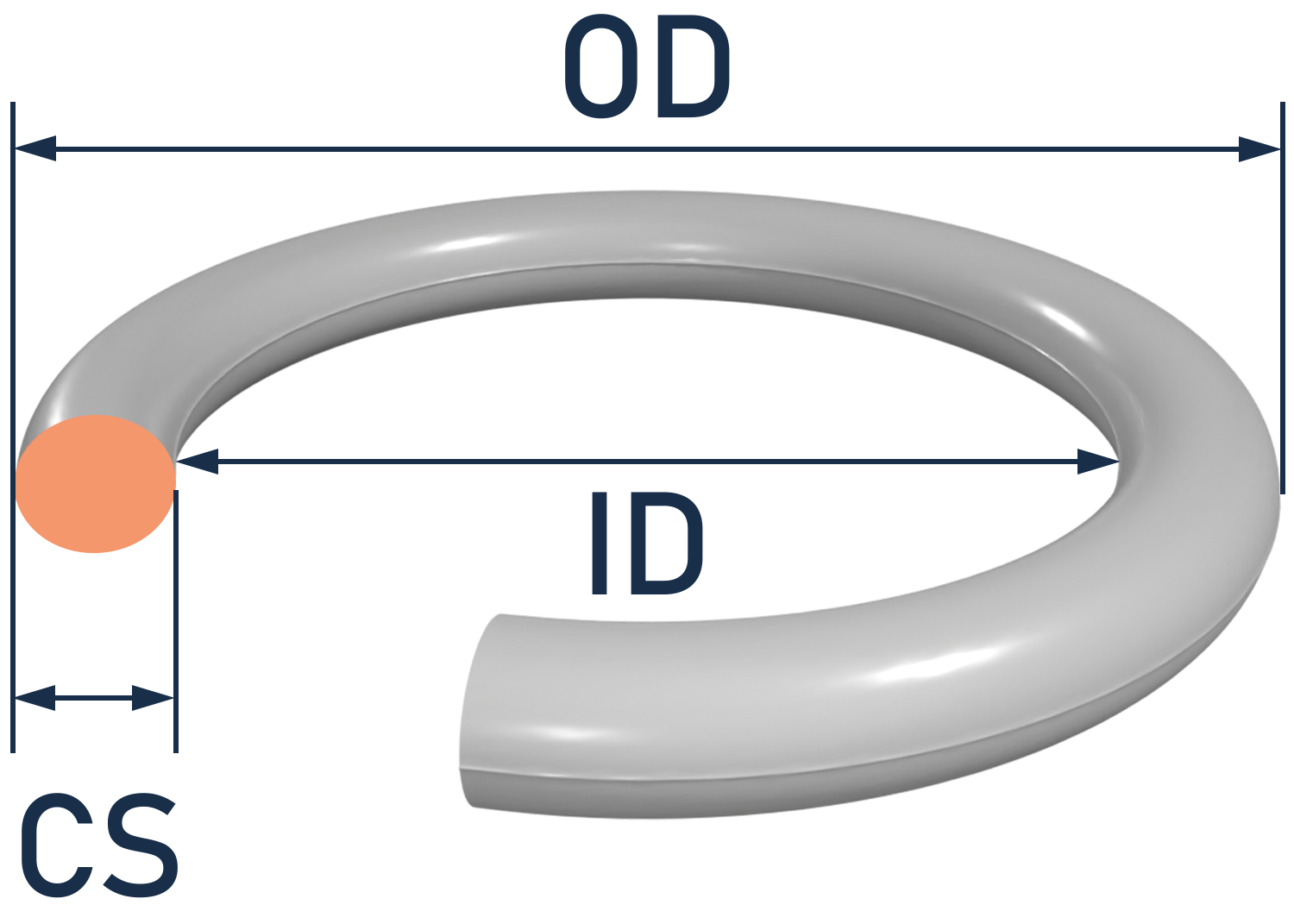
Back to Elastomers Hub
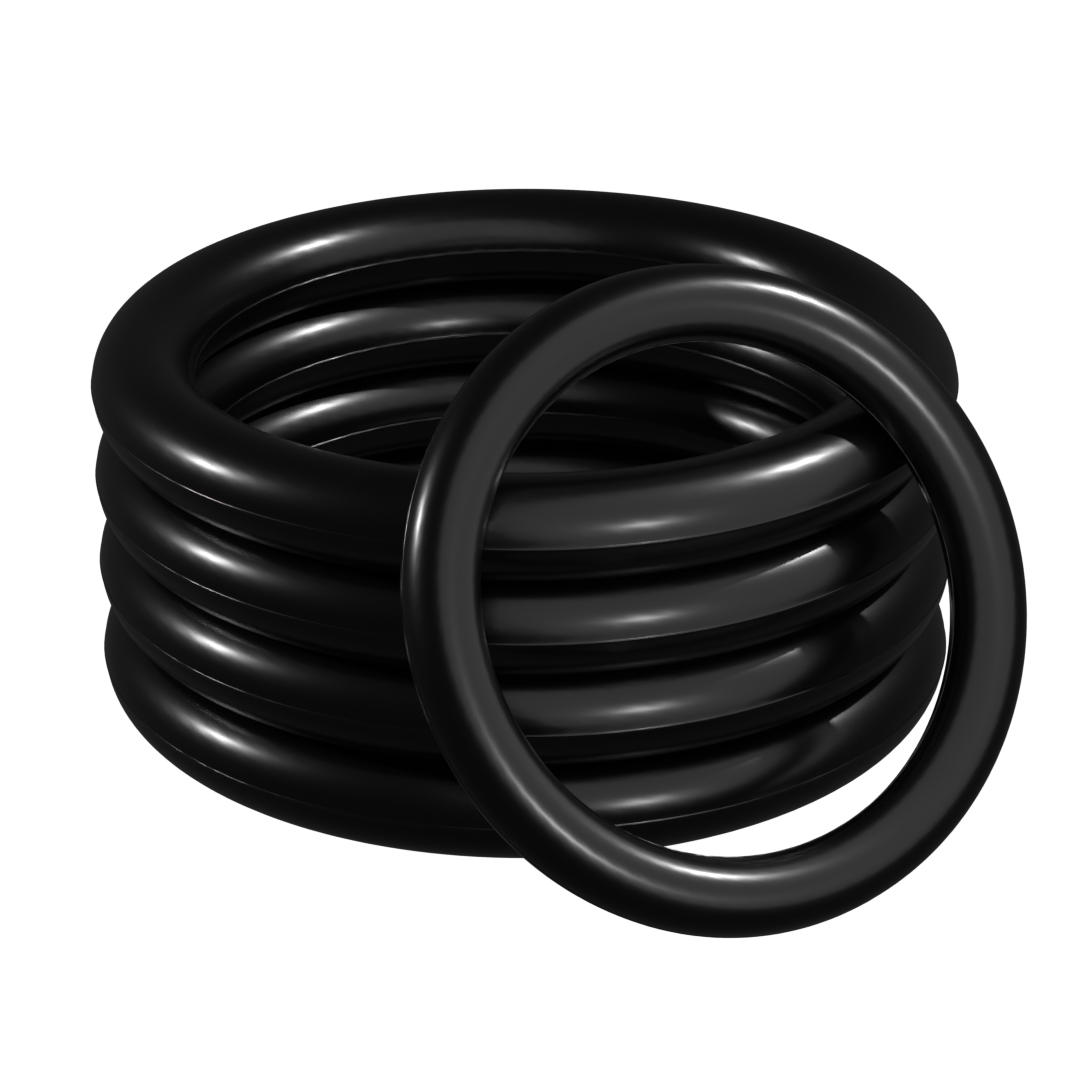
Get A Quote Now!
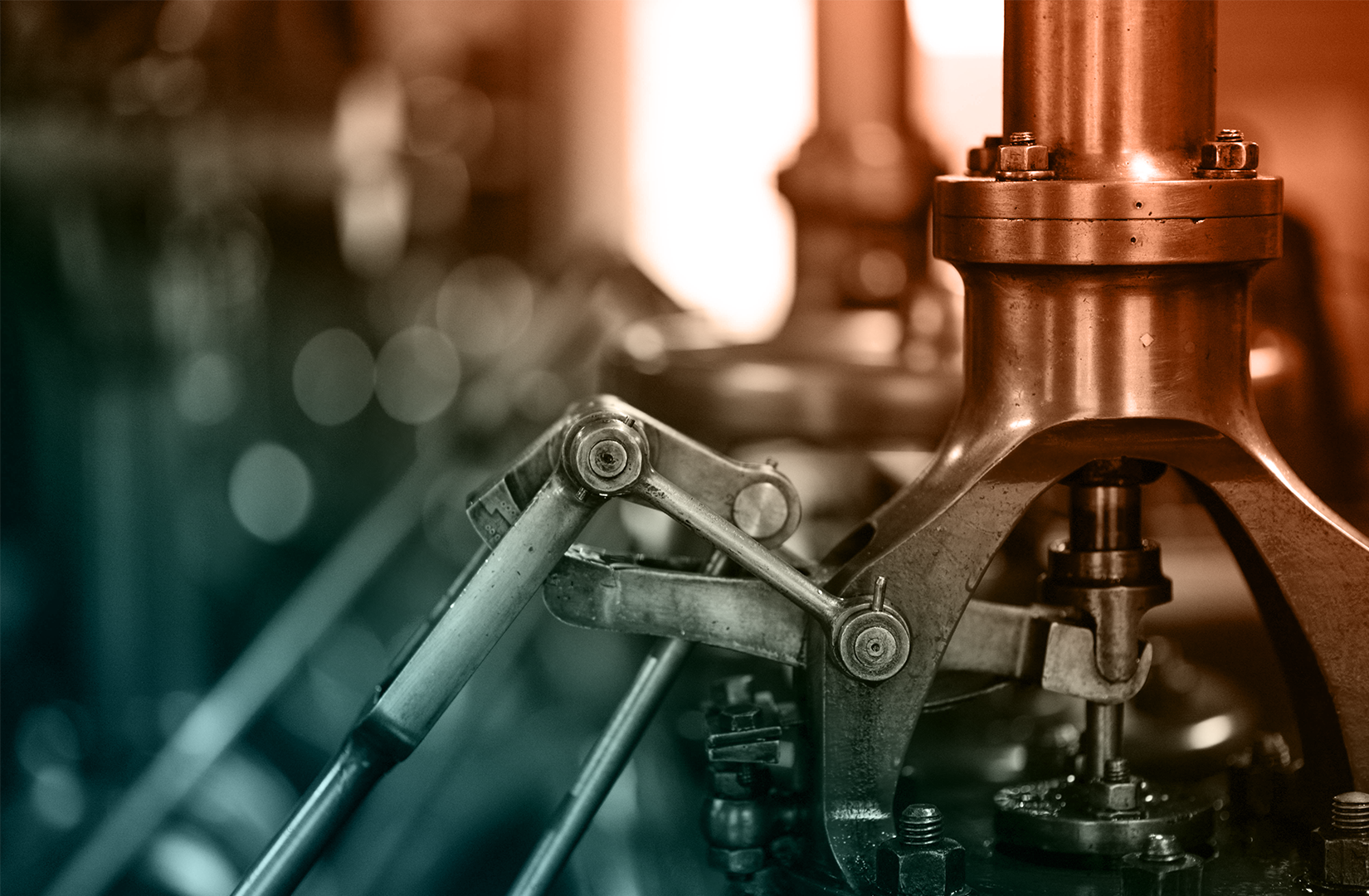
Groove Design References
Learn More
Coatings, Packaging, & Other Services
Learn More
Custom Parts & Custom O-rings
Learn More
Are green O-rings heat resistant?
The color of an O-ring does not necessarily indicate its heat resistance. O-rings are made from various elastomer materials, and their heat resistance depends on the specific material used rather than their color.
Heat resistance of O-rings is determined by the elastomer material's formulation and its ability to withstand elevated temperatures without losing its sealing properties or degrading. Common elastomer materials used for heat-resistant O-rings include:
The color of an O-ring doesn't inherently signify a specific characteristic or quality; rather, it's often used as a means to identify different materials or specifications. Here's a general guide to what different colored O-rings might indicate:
1. Black: The most common color for O-rings, typically made of nitrile (Buna-N), neoprene, EPDM, or other general-purpose materials. These are widely used in various applications due to their good resistance to oils, fuels, and certain chemicals. However, it should be noted that virtually any elastomeric material can be, and will frequently be manufactured in black colorations. This includes specialty materials like Aflas, FFKM Perfluoroelastomers, and silicone.
2. Blue: Fluorosilicone O-rings are typically manufactured in blue colorations. Also, blue is often associated with FDA-approved materials that are safe for food, water, and beverage contact. Blue O-rings are also easily detectable, which helps in maintaining safety standards in food processing industries.
3. Green: Commonly indicates the presence of hydrogenated nitrile (HNBR), which offers better heat and chemical resistance compared to standard nitrile. Viton® (fluorocarbon rubber) can also frequently be found in green colorations.
4. Brown: Typically signifies the use of Viton® (fluorocarbon rubber), known for its excellent resistance to high temperatures and chemicals, including petroleum products.
5. Red, Orange, or Pink: Frequently used for silicone O-rings, which are known for their heat resistance and use in food-grade applications.
6. White or Clear: Often indicates that the O-ring is made from silicone, Teflon (PTFE), or another material that is suitable for sanitary or medical applications.
7. Yellow: May indicate special compounds, such as polyurethane, which are known for their wear resistance and strength.
8. Metal Detectable O-rings: These O-rings are infused with metal detectable materials and are often blue. They are used in the food and pharmaceutical industries where contamination by foreign objects is a critical concern.
It's important to note that these color associations are not universal and can vary between manufacturers. The color alone should not be relied upon to determine the material or suitability of an O-ring for a specific application. Always refer to the manufacturer's specifications or consult with a Canyon Components engineer when selecting an O-ring for a particular use.
To determine the heat resistance of an O-ring, it is crucial to identify the material it is made from and consult the manufacturer's specifications or datasheets to ensure that it meets the temperature requirements of your specific application. The color alone should not be used as an indicator of heat resistance.
How long does an EPDM O-ring last?
The lifespan of an EPDM (Ethylene Propylene Diene Monomer) O-ring depends on various factors, including the application environment, the quality of the O-ring, and how it is used and maintained. However, EPDM O-rings are generally known for their long service life, especially in suitable applications.
1. Application Environment: EPDM O-rings perform well in environments with sunlight, ozone, weathering, and certain chemicals. They are often used in outdoor applications due to their excellent resistance to aging under UV light and ozone. However, they are not suitable for use with oils, fuels, and hydrocarbons, as they can degrade in such environments.
2. Temperature Range: EPDM maintains its properties over a wide temperature range, typically from -48°C to +150°C (-55°F to +300°F). Consistent exposure to temperatures outside this range can shorten the O-ring's lifespan.
3. Quality of the O-ring: Higher quality EPDM O-rings, manufactured with better compounding and curing processes, will typically last longer than lower quality alternatives.
4. Usage and Maintenance: Proper installation and regular maintenance can significantly extend the life of an EPDM O-ring. Mechanical stress, excessive stretching during installation, and improper sizing can all reduce the lifespan.
In ideal conditions, EPDM O-rings can last many years, potentially up to 10-20 years, but this can vary widely based on the specific application and conditions. For critical applications, it's recommended to regularly inspect and replace O-rings as needed, and perform application specific testing for lifespan estimates based on the intended use.
How many types of EPDM are there?
EPDM rubber, or Ethylene Propylene Diene Monomer, is available in various grades, each designed to meet specific requirements for different applications. The grades of EPDM rubber differ mainly in terms of their monomer composition, which influences their physical properties and suitability for various uses.
1. Commercial Grade EPDM Rubber: This grade is commonly used for general-purpose applications such as roofing membranes, gaskets, and weatherstripping. It is recognized for its durability, flexibility, and cost-effectiveness.
2. WRAS Approved EPDM Rubber: This grade adheres to the Water Regulations Advisory Scheme (WRAS) standards, making it suitable for applications involving potable water. It is specifically used in water and plumbing systems where maintaining water quality and meeting regulatory standards is essential.
3. Expanded EPDM/Neoprene Closed-Cell Sponge Rubber: This grade combines EPDM with Neoprene in a closed-cell structure, enhancing its insulation properties. It is particularly valuable in applications requiring both effective insulation and moisture resistance.
Each of these grades possesses distinct characteristics that make them suitable for specific industrial and commercial applications. The choice of EPDM grade depends on factors such as the required durability, flexibility, chemical resistance, and the specific environmental conditions of the application.
Is EPDM better than rubber?
Whether EPDM (Ethylene Propylene Diene Monomer) is "better" than other types of rubber depends on the specific application and environment. EPDM is a type of synthetic rubber with particular properties that make it suitable for certain uses. Here's how EPDM compares to other rubbers in various aspects:
1. Resistance to Weathering and Ozone: EPDM excels in outdoor applications due to its superior resistance to UV radiation, ozone, and weathering. This makes it better than many other rubbers for applications exposed to harsh environmental conditions.
2. Temperature Resistance: EPDM has a wide operating temperature range and can perform well in both hot and cold environments, which is better than some types of rubber, like natural rubber, that don’t perform as well at higher temperatures.
3. Chemical Resistance: EPDM is resistant to many chemicals, particularly water-based and alkaline substances. However, it is not resistant to oil, gasoline, and hydrocarbons, where nitrile rubber or Viton would be better choices.
4. Electrical Insulation: EPDM is an excellent electrical insulator, making it preferable in applications where this property is required.
5. Flexibility and Durability: EPDM maintains its flexibility over a wide temperature range and has good tensile strength, but it may not be as flexible as some natural rubber compounds in certain applications.
6. Cost-Effectiveness: Generally, EPDM is more cost-effective than some specialized synthetic rubbers, like silicone or fluorocarbons (Viton), especially in applications where its specific resistance properties are required.
7. Water, Steam Resistance: EPDM is an excellent choice for applications involving water or steam, surpassing most other rubbers in this regard.
In summary, EPDM has advantages in environmental resistance, temperature range, and cost-effectiveness for specific applications. However, it is not suitable for use with oils or hydrocarbons, and other types of rubber may be better in those environments. The "best" rubber depends on the specific requirements of the application, including exposure to chemicals, temperature, and physical demands.
Is EPDM or Viton better for acid?
When it comes to resistance against acids, the suitability of EPDM (Ethylene Propylene Diene Monomer) and Viton (a brand name for Fluorocarbon elastomers) largely depends on the type of acid and the concentration involved. Both materials have different levels of chemical resistance:
1. EPDM: It has good resistance to many mild acids, especially at lower concentrations. It is also resistant to bases, steam, and polar substances like ketones and alcohols. However, its resistance to strong and concentrated acids can be limited. EPDM is often chosen for its excellent resistance to weathering, ozone, UV radiation, and aging, rather than its chemical resistance.
2. Viton: Known for its exceptional resistance to a wide range of chemicals, Viton performs well against many acids, including some stronger and more corrosive ones. It's particularly resistant to sulfuric, nitric, hydrochloric, and phosphoric acids at varying concentrations. However, its resistance can vary with the concentration and temperature of the acid. Viton is also highly resistant to oils, fuels, and most mineral acids, making it suitable for harsher chemical environments.
Key Considerations:
- Type of Acid: The specific acid and its concentration play a crucial role. For instance, Viton is generally better for handling stronger acids.
- Concentration and Temperature: Both concentration and temperature can affect the material's resistance. Higher concentrations and temperatures generally require materials with higher resistance, like Viton.
- Application Environment: Consider factors like exposure to other chemicals, temperature ranges, and whether the seal will be used in dynamic or static applications.
Conclusion:
- For strong, corrosive acids, particularly in higher concentrations and temperatures, Viton is often the better choice due to its superior chemical resistance.
- For milder acids and lower concentrations, especially in environments where weathering and ozone resistance are also important, EPDM may be sufficient.
It's important to consult with material specifications and possibly conduct compatibility tests for the specific acid and conditions of your application to make the best choice.
Is Nitrile Rubber an EPDM?
No, Nitrile Rubber (often referred to as NBR, Buna-N, or Acrylonitrile Butadiene Rubber) is not the same as EPDM (Ethylene Propylene Diene Monomer). These are two distinct types of synthetic rubber, each with different chemical compositions and properties:
1. Nitrile Rubber (NBR):
- Composition: Made from acrylonitrile and butadiene.
- Properties: Known for its excellent resistance to oils, fuels, and other chemicals like aliphatic hydrocarbons, mineral oils, and greases.
- Temperature Range: Generally, NBR can withstand temperatures from -40°C to 125°C (-40°F to 257°F).
- Applications: Commonly used in the automotive and aeronautical industry to make fuel and oil handling hoses, gaskets, seals, and o-rings. It is also used in disposable gloves, especially in the medical field.
2. Ethylene Propylene Diene Monomer (EPDM):
- Composition: Made from ethylene, propylene, and a diene comonomer.
- Properties: Excellent resistance to weathering, ozone, UV, and aging; good heat and steam resistance; very good insulation properties. Not resistant to oils and fuels.
- Temperature Range: EPDM typically operates effectively in a range of -55°C to 150°C (-67°F to 300°F).
- Applications: Commonly used in automotive weather stripping and hoses, roofing membranes, outdoor electrical cable insulation, and waterproofing sheets.
In summary, while both Nitrile Rubber and EPDM are synthetic rubbers used in a variety of applications, they have different chemical resistances and are suitable for different environments. NBR is preferable in applications involving oils and hydrocarbons, while EPDM is better suited for outdoor, heat, and steam applications.
Is Viton an EPDM?
No, Viton and EPDM are not the same; they are two distinct types of synthetic rubber, each with its own unique properties and chemical composition.
1. Viton: This is a brand name for a type of synthetic rubber and fluoropolymer elastomer, typically known as Fluoroelastomers (FKM). Viton is known for its excellent resistance to high temperatures and a wide range of chemicals, including oils, fuels, lubricants, and most mineral acids. It is commonly used in environments where these resistances are crucial, such as in the automotive, aerospace, and chemical processing industries.
2. EPDM (Ethylene Propylene Diene Monomer): This is a type of synthetic rubber made from ethylene, propylene, and a diene monomer. EPDM is known for its excellent resistance to weathering, ozone, UV radiation, and aging. It is also resistant to water, steam, and some mild acids and alkalis. However, it does not have good resistance to oil and fuel, which is a stark contrast to Viton. EPDM is commonly used in outdoor applications, such as in automotive weather stripping and seals, roofing membranes, and window and door seals.
In summary, while both Viton and EPDM are valuable in their respective applications due to their specific properties, they are not interchangeable and are chosen based on the requirements of the application regarding chemical exposure, temperature range, and environmental conditions.
Is Viton stronger than EPDM?
The term "stronger" can mean different things in the context of material properties, such as tensile strength, tear resistance, or resilience under various conditions. When comparing Viton and EPDM, it's important to consider the specific aspects of strength relevant to your application:
Tensile Strength and Tear Resistance
- Viton: Generally has higher tensile strength compared to EPDM, although this can vary with different blends. This means it can withstand more stress or force before breaking. Viton also typically exhibits better resistance to tearing, especially in harsh chemical environments.
- EPDM: While EPDM has good tensile strength, it is generally lower than that of Viton. It's more valued for its flexibility and durability in extreme weather conditions rather than its raw strength.
Resistance to Chemicals and Temperature
- Viton: Has superior resistance to a wide range of chemicals, including oils, fuels, lubricants, and some acids. It also excels in high-temperature applications, maintaining its integrity and strength at temperatures where EPDM might degrade.
- EPDM: Excellent resistance to ozone, UV, and weathering makes it strong in outdoor applications. However, it lacks the chemical and oil resistance of Viton and is not as strong in high-temperature scenarios.
Durability in Different Environments
- Viton: Maintains its strength and resists degradation in environments that would adversely affect many other materials, such as automotive or industrial settings with exposure to hydrocarbons.
- EPDM: Exhibits strong durability in outdoor, UV-exposed, or weather-impacted applications but can weaken in the presence of oils, fuels, and high heat.
General Physical Strength
- Both materials are quite robust in their respective areas of application. However, the "strength" as in resistance to physical stress or deformation under load will vary depending on the specific formulation of the elastomer.
Conclusion
- Viton: Stronger in terms of chemical resistance, high-temperature performance, and tensile strength. Ideal for harsh industrial environments.
- EPDM: Strong in terms of weathering, UV resistance, and flexibility at low temperatures. Best suited for outdoor and water-based applications.
The choice between Viton and EPDM should be based on the specific environmental and chemical conditions they will face in their intended application. Each material has its strengths and weaknesses, making them suitable for different types of challenges.
What are cheap O-rings made of?
Cheap O-rings are typically made from less expensive elastomer materials compared to premium or specialized O-rings like Viton, specialty Silicone blends, Aflas, or FFKM. The choice of material depends on the cost-effectiveness required for the application. Here are some common inexpensive elastomers used for cheap O-rings:
1. Nitrile Rubber (NBR): Nitrile rubber, also known as Buna-N, is one of the most cost-effective elastomers. It offers good resistance to oils, fuels, and lubricants, making it a popular choice for many industrial applications. While it may not have the same level of performance as more expensive materials, it is suitable for many standard sealing applications.
2. EPDM (Ethylene Propylene Diene Monomer): EPDM is known for its excellent weather resistance and is often used in outdoor applications. It's more cost-effective than premium elastomers like Viton and Silicone and is suitable for sealing applications that don't require high-temperature or chemical resistance.
3. SBR (Styrene Butadiene Rubber): SBR is an economical elastomer often used in low-cost O-rings. It has good abrasion resistance but may not offer the same level of chemical resistance as Nitrile or EPDM.
4. Natural Rubber (NR): Natural rubber is another low-cost elastomer option. It offers good elasticity and low-temperature flexibility but may not perform well in environments with oils or certain chemicals.
5. Neoprene (CR): Neoprene is a moderately priced elastomer known for its resistance to weathering, ozone, and UV radiation. It's often used in outdoor applications where cost is a consideration.
While these materials are cost-effective, it's important to note that they have limitations compared to more expensive elastomers like Viton, specialty Silicone blends, Aflas, and FFKM. They may not perform well in extreme temperature or chemical environments. When choosing O-rings, it's essential to consider the specific requirements of your application and select the material that balances performance and cost-effectiveness to meet those needs.
What are EPDM O-rings used for?
EPDM O-rings, made from Ethylene Propylene Diene Monomer, a type of synthetic rubber, are used in a variety of applications due to their excellent resistance to environmental factors and certain chemicals. Here are some common uses:
1. Automotive Applications: They are used in cooling systems, brake systems, and windshield wiper systems because of their resistance to heat and weathering.
2. HVAC Systems: EPDM O-rings are suitable for heating and cooling systems, including air conditioning units, due to their excellent heat and steam resistance.
3. Water and Steam Systems: Their resistance to hot water and steam makes them ideal for use in boilers, steam appliances, hot water systems, and outdoor water applications.
4. Outdoor Applications: Due to their excellent resistance to UV rays, ozone, and weathering, they are used in outdoor fixtures and applications that are exposed to harsh environmental conditions.
5. Chemical Processing: EPDM O-rings are used in applications involving certain chemicals, especially those where resistance to acids, alkalis, and ketones is required.
6. Food and Beverage Industry: They are sometimes used in food processing equipment due to their non-toxic nature and ability to withstand cleaning agents and hot water.
7. Pharmaceutical and Medical Fields: Their compatibility with certain hygienic requirements makes them suitable for some medical devices and pharmaceutical processing equipment.
It is important to note that while EPDM O-rings have excellent resistance to many environmental factors, they are not suitable for use with petroleum-based oils and fuels as they can degrade or swell in such environments. The specific use of an EPDM O-ring should always be determined based on the compatibility of EPDM with the particular substances and conditions of the application.
What does EPDM mean in rubber?
EPDM stands for "Ethylene Propylene Diene Monomer." It is a type of synthetic rubber widely used in a variety of applications. Here's a breakdown of what EPDM is and its key characteristics:
1. Chemical Structure:
- Ethylene and Propylene: These are the primary components of EPDM. They form a copolymer, which is a polymer derived from two different monomers. This combination provides excellent resistance to ozone, weathering, and heat.
- Diene Monomer: The addition of a diene component allows for sulphur vulcanization (a process of cross-linking polymer chains to form a more durable material). This makes EPDM more versatile and improves certain properties like its elasticity and resilience.
2. Properties:
- Weather Resistance: EPDM is extremely resistant to degradation from weather elements like UV rays, ozone, and extreme temperatures, making it ideal for outdoor applications.
- Chemical Resistance: It has good resistance to polar substances such as water, steam, and some mild acids, alkalis, and solvents.
- Thermal Stability: EPDM maintains its properties over a wide temperature range, typically from -67°F to 300°F (-55°C to 150°C).
- Electrical Insulation: It is a good electrical insulator, which makes it useful in various electrical applications.
3. Applications:
- EPDM is used in automotive weather stripping and seals, due to its excellent resistance to ozone, steam, and heat.
- It's found in roofing membranes for its durability and resistance to weather.
- It's used in hoses, gaskets, and tubing, especially where heat, ozone, and weather resistance are needed.
- EPDM is also used in pond liners, window and door seals, and electrical insulation.
4. Versatility:
- EPDM can be formulated in various ways to enhance specific properties, like tensile strength or elasticity, making it adaptable for a wide range of applications.
In summary, EPDM is a versatile and durable synthetic rubber known for its excellent resistance to environmental factors, making it suitable for both outdoor and some industrial applications. Its ability to withstand harsh weather conditions, along with its thermal stability and chemical resistance, makes it a popular choice in various industries.
What is an EPDM O-ring?
An EPDM O-ring is a type of sealing component made from Ethylene Propylene Diene Monomer (EPDM), a synthetic rubber. O-rings are small, loop-shaped seals used in a wide variety of applications to prevent the escape of gases or liquids. They are placed in grooves and compressed between two or more parts to form a seal.
EPDM is particularly well-suited for O-rings due to its excellent resistance to weathering, UV radiation, ozone, aging, and many chemicals. It's also known for its good heat resistance and insulating properties. However, EPDM is not recommended for use with petroleum-based oils and fuels because it can swell or degrade when exposed to these substances.
EPDM O-rings are commonly used in automotive cooling systems, outdoor weather-resistant applications, water and steam systems, and various other applications where the O-ring will not come into contact with oils or fuels. The specific choice of an EPDM O-ring depends on factors like the required temperature range, the type of chemicals it will be exposed to, and the required durability.
What is better, EPDM or Buna?
Whether Nitrile or EPDM is "better" depends largely on the specific application and environmental conditions they are intended for. Both Nitrile and EPDM have distinct properties that make them suitable for different uses. Here's a comparison to help determine which might be more appropriate for a given situation:
1. Oil and Fuel Resistance:
- Nitrile: Excellent resistance to oils, fuels, and other hydrocarbons. This makes it a preferred choice for automotive and industrial applications involving oil and petroleum-based products.
- EPDM: Poor resistance to oil and fuel. It is not suitable for applications involving petroleum products.
2. Weather and UV Resistance:
- Nitrile: Good resistance to weather, but not as strong as EPDM. It can degrade with prolonged exposure to UV rays.
- EPDM: Outstanding resistance to weather, UV radiation, and ozone. Ideal for outdoor applications.
3. Heat Resistance:
- Nitrile: Generally good heat resistance, but typically not as high as EPDM. It can handle temperatures up to about 275°F (135°C).
- EPDM: Excellent heat resistance, often used in applications with temperatures up to 300°F (150°C) and sometimes higher.
4. Chemical Resistance:
- Nitrile: Good resistance to many chemicals, especially hydrocarbons, oils, and fats.
- EPDM: Excellent resistance to a wide range of chemicals, including certain acids, alkalis, and ketones, but not suitable for exposure to oils and fuels.
5. Application Examples:
- Nitrile: Often used in seals, gaskets, hoses, and O-rings in automotive, oil and gas, and mechanical applications.
- EPDM: Commonly used in weather seals, roofing membranes, electrical insulation, and automotive cooling systems.
6. Cost:
- The cost can vary, but generally, Nitrile is less expensive than EPDM, making it a cost-effective option for applications that don't require the superior weather and heat resistance of EPDM.
In summary, the choice between Nitrile and EPDM depends on the specific requirements of your application. For environments involving oils and fuels, Nitrile is the better choice. For applications that demand high weather, UV, and heat resistance, EPDM is preferable. Always consider the environmental conditions and chemical exposures that the material will face to make the most appropriate selection.
What is the best O-ring for gasoline?
When selecting an O-ring for use with gasoline, the key factors to consider are the O-ring's resistance to gasoline (including any additives in the fuel), its ability to maintain integrity at various temperatures, and its compatibility with other environmental factors it may encounter. The most commonly recommended materials for O-rings used with gasoline are:
1. Viton (Fluorocarbon, FKM): Viton is often considered one of the best materials for gasoline applications due to its excellent resistance to hydrocarbons, including gasoline and its additives. It maintains its properties over a wide temperature range and offers good resistance to aging and weathering. This makes it a preferred choice for automotive fuel handling systems.
2. Nitrile (Buna-N, NBR): Nitrile rubber is another popular choice for gasoline applications, especially when cost is a consideration. It has good resistance to oils and fuels, including gasoline. However, it may not perform as well as Viton in high-temperature environments or when exposed to certain additives in modern fuels.
3. Ethylene Propylene Diene Monomer (EPDM): While EPDM has excellent resistance to weathering, ozone, and aging, its compatibility with gasoline is generally poor. It's not typically recommended for use with gasoline or petroleum-based fluids.
4. Neoprene (Chloroprene, CR): Neoprene has moderate resistance to gasoline but is generally less preferred than Viton or Nitrile for this application. It's more commonly used in environments where resistance to weathering and ozone is a priority.
5. Silicone: Silicone O-rings are not recommended for use with gasoline. They have poor resistance to petroleum-based fuels and oils.
Summary
- Best Overall: Viton is often considered the best choice for gasoline applications due to its superior resistance to hydrocarbons and high temperatures.
- Cost-Effective Alternative: Nitrile is a good, less expensive alternative with acceptable resistance to gasoline but may not perform as well in extreme conditions compared to Viton.
It's important to ensure that the O-ring material is compatible not only with gasoline but also with any fuel additives that may be present. Additionally, always check the specifications and recommendations from the O-ring manufacturer or supplier for your specific application.
What is the difference between EPDM and Viton O-rings?
EPDM (Ethylene Propylene Diene Monomer) and Viton (a brand name for Fluorocarbon elastomers) are both types of synthetic rubber, but they have different chemical compositions and properties that make them suitable for different applications. Here's a comparison of their key characteristics:
Chemical Composition
- EPDM: It is a terpolymer made from ethylene, propylene, and a diene monomer. The diene component allows for vulcanization with sulfur and other curatives.
- Viton: It is made from fluoropolymer elastomers, which are a family of synthetic rubbers made from fluorocarbon-based compounds. This gives it a high degree of resistance to heat and chemicals.
Resistance to Chemicals and Fluids
- EPDM: Excellent resistance to ozone, weathering, and aging; good resistance to water, steam, alkalis, and mild acidic environments. However, it has poor resistance to petroleum-based oils and fuels.
- Viton: Outstanding resistance to oils, fuels, lubricants, and most mineral acids. It also has excellent resistance to high temperatures and can withstand a variety of chemicals.
Temperature Range
- EPDM: Generally effective in temperatures ranging from -67°F to 300°F (-55°C to 150°C), although certain specialty blends can perform well outside of this range. It performs well in outdoor applications due to its resistance to harsh weather conditions.
- Viton: Has a broader temperature range, typically from -15°F to 437°F (-26°C to 225°C), and can withstand higher temperatures for short periods. This makes it suitable for applications involving high temperatures. Certain blends are capable of low temperature performance down to -54°F (-48°C).
Applications
- EPDM: Commonly used in automotive weather stripping and seals, roofing membranes, electrical insulation, and other applications where resistance to weather and ozone is crucial. It's also used in the water and steam systems due to its excellent water resistance.
- Viton: Primarily used in situations requiring resistance to high temperatures and chemicals, such as in automotive fuel handling systems, chemical processing industries, and aerospace applications.
Cost
- EPDM: More cost-effective for applications where resistance to weathering and ozone is required but not in contact with oils and fuels.
- Viton: Generally more expensive due to its costly composition and superior resistance to chemicals & high temperatures.
Summary
- EPDM: Best for outdoor and water/steam applications due to its excellent weather, ozone, and water resistance but not suitable for use with oils or fuels.
- Viton: Ideal for applications requiring resistance to high temperatures and a wide range of chemicals, including oils and fuels, but more expensive.
The choice between EPDM and Viton O-rings depends largely on the specific requirements of the application, including the types of chemicals, temperatures, and environmental conditions they will be exposed to.
What is the difference between EPR and EPDM O-rings?
EPR (Ethylene Propylene Rubber) and EPDM (Ethylene Propylene Diene Monomer) are both types of synthetic rubber, and they are often confused because of their similar names and properties. However, there are some distinctions between them:
1. Chemical Composition:
- EPR: Ethylene Propylene Rubber is essentially a copolymer of ethylene and propylene.
- EPDM: Ethylene Propylene Diene Monomer is a terpolymer, which means it is made up of three different monomers: ethylene, propylene, and a diene component. The diene addition allows for cross-linking via sulphur vulcanization, which is not possible with EPR.
2. Vulcanization:
- EPR can be vulcanized using peroxide-based systems. It does not contain a diene, so it cannot be vulcanized (cured) using sulphur-based systems.
- EPDM, due to the presence of the diene monomer, can be vulcanized using both peroxide and sulphur-based systems, giving it a broader range of cross-linking options.
3. Properties:
- Both EPR and EPDM are known for their excellent resistance to ozone, weathering, and aging. They are also both very resistant to polar substances like water, steam, and some acids.
- The addition of the diene in EPDM generally enhances its resistance to environmental factors and improves its overall range of physical properties.
4. Applications:
- EPR is used in applications requiring good resistance to water, steam, and some chemicals. It is common in automotive cooling systems and some chemical processing environments.
- EPDM is widely used in outdoor applications due to its superior resistance to weathering, ozone, and UV rays. It's found in automotive weather stripping and seals, roofing membranes, and electrical insulation.
5. Temperature Range:
- Both materials can operate in similar temperature ranges, typically between -55°F to 300°F (-48°C to 150°C), although this can vary based on the specific formulation.
In summary, while EPR and EPDM are similar in many aspects, especially in their resistance to weathering, ozone, and water, the key difference lies in their chemical structure and the type of vulcanization they undergo. EPDM's terpolymer structure with a diene component offers more versatility in processing and potentially enhanced properties in certain applications. However, for many practical purposes, they can often be used interchangeably, especially in applications where their resistance to weathering and water is the primary concern.
What is the most common type of O-ring?
The most common type of O-ring material used is Nitrile rubber, often referred to as NBR (Nitrile Butadiene Rubber) O-rings. NBR O-rings are widely used in various industries and applications due to their versatile properties and cost-effectiveness. Here are some reasons why NBR O-rings are commonly used:
1. Oil and Fuel Resistance: NBR O-rings exhibit excellent resistance to oils, fuels, and lubricants, making them ideal for sealing applications in automotive, machinery, and hydraulic systems.
2. Chemical Compatibility: NBR is compatible with a wide range of non-polar and polar chemicals, which makes it suitable for many industrial applications.
3. Temperature Range: NBR O-rings can perform effectively within a moderate temperature range, typically from -40°C (-40°F) to 125°C (257°F).
4. Cost-Effectiveness: NBR is relatively inexpensive compared to some other elastomer materials, making it a cost-effective choice for sealing solutions.
5. Availability: NBR O-rings are readily available in various sizes, shapes, and durometers, making them easy to source for a wide range of applications.
While NBR is the most common type of O-ring material, it's important to note that O-rings are available in a variety of materials, each with its own set of properties and suitability for specific applications. Depending on the requirements of the application, other types of O-ring materials, such as Viton (FKM), EPDM, silicone, and HNBR, may also be used to meet specific performance criteria such as temperature resistance, chemical compatibility, or durability. The choice of O-ring material should be based on the specific needs of the sealing application.
What is the strongest O-ring material?
The term "strongest" when referring to O-ring materials can mean different things depending on the specific requirements of the application, such as resistance to chemicals, temperature extremes, pressure, or wear and tear. There is no single "strongest" O-ring material that suits all applications; instead, the best material depends on the specific conditions the O-ring will be exposed to. Here are some materials considered strong in various aspects:
1. FKM (Fluoroelastomer, e.g., Viton): Known for excellent chemical resistance, especially to oils, fuels, and some acids, and high-temperature tolerance (up to about 225°C or 437°F). It is often considered one of the strongest materials in terms of chemical and heat resistance.
2. FFKM (Perfluoroelastomer, e.g., CanRez, Kalrez, Chemraz): Offers even higher chemical and temperature resistance than standard FKM. It can withstand temperatures up to 335°C (635°F) and almost all chemicals. FFKM O-rings are often used in extremely harsh chemical and thermal environments.
3. Nitrile Rubber (NBR, Buna-N): Offers excellent resistance to oils and petroleum-based fluids. It's a strong choice for applications involving oil and fuel exposure.
4. EPDM (Ethylene Propylene Diene Monomer): Has outstanding resistance to weathering, ozone, UV rays, and aging, as well as good heat and steam resistance. It's a strong material for outdoor and water/steam applications.
5. Silicone: Exhibits excellent flexibility and is resistant to extreme temperatures, both hot and cold. It's a strong choice for applications requiring temperature resistance over a wide range.
6. Polyurethane: Known for its excellent wear and tear resistance, making it a strong material for high-pressure hydraulic systems and applications involving abrasion.
Each of these materials has its strengths in specific areas, and the choice of material should be based on the application's requirements, including exposure to chemicals, temperature, pressure, and wear. In some highly demanding applications, specialized O-ring materials like FFKM might be necessary due to their superior resistance qualities, despite their higher cost.
Which is better, EPDM or Viton?
The choice between EPDM (Ethylene Propylene Diene Monomer) and Viton (a brand of FKM, fluoroelastomer) depends on the specific application and environmental conditions each material will be exposed to. Here's a comparison of the two:
1. Chemical Resistance:
- Viton: Excellent chemical resistance, particularly to oils, fuels, and hydrocarbons. It's also resistant to a wide range of other chemicals.
- EPDM: Good resistance to a variety of chemicals, but particularly strong against weathering, ozone, and UV rays. Not suitable for use with oils and fuels.
2. Temperature Range:
- Viton: Can handle higher temperature ranges than EPDM, typically up to 225°C (437°F), making it suitable for high-temperature applications.
- EPDM: Generally has a lower temperature range, up to around 150°C (302°F).
3. Cost:
- Viton: Generally more expensive than EPDM, due to its superior performance in harsh environments and expensive composition.
- EPDM: More cost-effective, making it a good choice for applications where its resistance properties are adequate.
4. Applications:
- Viton: Commonly used in automotive, aerospace, and industrial applications where chemical and temperature resistance is critical.
- EPDM: Often used in outdoor applications like roofing, seals in vehicles, and window and door seals due to its excellent weathering resistance.
5. Physical Properties:
- Viton: Typically harder and more resistant to compression set than EPDM.
- EPDM: More flexible and with better fatigue resistance.
6. Environmental Resistance:
- Viton: Better suited for harsh chemical environments.
- EPDM: Better for outdoor applications where weather and UV resistance are needed.
Ultimately, the choice depends on the specific requirements of your application, including exposure to chemicals, temperature ranges, and environmental conditions. It's always best to consult with a materials specialist or engineer to determine the most appropriate material for your specific needs.
Which is better, FKM or EPDM?
Choosing between FKM (Fluoroelastomer, with Viton being a well-known brand) and EPDM (Ethylene Propylene Diene Monomer) depends on the specific application requirements and environmental conditions. Both materials have unique properties that make them suitable for different uses. Here's a comparison to help determine which might be better for a given situation:
1. Chemical Resistance:
- FKM: Offers superior resistance to oils, fuels, lubricants, and most mineral acids. It also has good resistance to a variety of other chemicals.
- EPDM: Excellent resistance to ozone, weathering, and UV radiation. It also performs well with certain chemicals, especially ketones, hot water, steam, and alkalis. However, it is not suitable for use with oils, fuels, and hydrocarbons.
2. Temperature Resistance:
- FKM: Can handle higher temperatures, generally up to 225°C (437°F), and in some special formulations, even higher.
- EPDM: Has a lower temperature range, typically up to 150°C (300°F).
3. Environmental Conditions:
- FKM: Performs well in harsh chemical environments and where high heat resistance is needed.
- EPDM: Excellent for outdoor applications due to its superior resistance to weathering, ozone, and UV rays.
4. Cost:
- FKM: Generally more expensive, reflecting its advanced resistance capabilities, particularly in harsh chemical and temperature environments.
- EPDM: More cost-effective for applications where its properties are sufficient.
5. Applications:
- FKM: Common in automotive, aerospace, and industrial sectors for seals, O-rings, and gaskets, especially where oil and acid resistance is crucial.
- EPDM: Frequently used in automotive weather stripping and hoses, roofing membranes, and outdoor electrical insulation.
In summary, the choice between FKM and EPDM depends largely on the application's exposure to temperatures, chemicals, and environmental factors. FKM is typically better for applications involving oils, fuels, and high temperatures, while EPDM is more suitable for outdoor and water-based applications. Always consider the specific requirements of your application when choosing between these materials.
Which is better, Nitrile or EPDM?
Whether Nitrile or EPDM is "better" depends largely on the specific application and environmental conditions they are intended for. Both Nitrile and EPDM have distinct properties that make them suitable for different uses. Here's a comparison to help determine which might be more appropriate for a given situation:
1. Oil and Fuel Resistance:
- Nitrile: Excellent resistance to oils, fuels, and other hydrocarbons. This makes it a preferred choice for automotive and industrial applications involving oil and petroleum-based products.
- EPDM: Poor resistance to oil and fuel. It is not suitable for applications involving petroleum products.
2. Weather and UV Resistance:
- Nitrile: Good resistance to weather, but not as strong as EPDM. It can degrade with prolonged exposure to UV rays.
- EPDM: Outstanding resistance to weather, UV radiation, and ozone. Ideal for outdoor applications.
3. Heat Resistance:
- Nitrile: Generally good heat resistance, but typically not as high as EPDM. It can handle temperatures up to about 275°F (135°C).
- EPDM: Excellent heat resistance, often used in applications with temperatures up to 300°F (150°C) and sometimes higher.
4. Chemical Resistance:
- Nitrile: Good resistance to many chemicals, especially hydrocarbons, oils, and fats.
- EPDM: Excellent resistance to a wide range of chemicals, including certain acids, alkalis, and ketones, but not suitable for exposure to oils and fuels.
5. Application Examples:
- Nitrile: Often used in seals, gaskets, hoses, and O-rings in automotive, oil and gas, and mechanical applications.
- EPDM: Commonly used in weather seals, roofing membranes, electrical insulation, and automotive cooling systems.
6. Cost:
- The cost can vary, but generally, Nitrile is less expensive than EPDM, making it a cost-effective option for applications that don't require the superior weather and heat resistance of EPDM.
In summary, the choice between Nitrile and EPDM depends on the specific requirements of your application. For environments involving oils and fuels, Nitrile is the better choice. For applications that demand high weather, UV, and heat resistance, EPDM is preferable. Always consider the environmental conditions and chemical exposures that the material will face to make the most appropriate selection.
Why choose EPDM?
Choosing EPDM (Ethylene Propylene Diene Monomer) rubber can be advantageous for various applications due to its unique properties and benefits:
1. Resistance to Weather and Environmental Factors: EPDM is exceptionally resistant to UV exposure, ozone, aging, and weathering, making it ideal for outdoor applications. Its durability in harsh environmental conditions ensures long-term performance without significant degradation.
2. Temperature Resistance: EPDM has a broad operating temperature range. It can maintain its properties in temperatures as low as -67°F (-55°C) and as high as 300°F (150°C). This makes it suitable for applications that experience extreme temperature variation.
3. Chemical Resistance: EPDM is resistant to many chemicals, especially water-based and alkaline substances. It is often used in settings where chemical resistance is crucial, such as in certain industrial hose applications.
4. Cost-Effectiveness: Although the initial investment in EPDM may be higher than some other elastomers, its durability and minimal maintenance requirements can lead to significant long-term cost savings. This makes it a financially sensible choice for projects focused on efficiency and budget optimization.
5. Versatility in Applications: EPDM's adaptability extends across various industries, including automotive, construction, and industrial applications. Its versatility allows it to be used in a wide range of products, such as vehicle weather stripping, roofing materials, water system O-rings, hoses, and electrical insulation.
6. Low Maintenance Requirements: EPDM requires minimal maintenance, contributing to its cost-effectiveness and ensuring sustained operational efficiency. This feature is particularly beneficial in applications where uninterrupted functionality is paramount.
7. Flexibility and Durability: EPDM remains flexible under varying conditions and exhibits good tensile strength, making it suitable for a variety of dynamic and static applications.
8. Water Resistance: EPDM is one of the most water-resistant rubber materials, which is why it is commonly used in roofing and waterproof liners.
In summary, the decision to choose EPDM depends on the specific requirements of the application, such as the need for environmental resistance, temperature stability, chemical resistance, and long-term durability. The versatility and cost-effectiveness of EPDM make it a popular choice in a wide range of industrial and commercial settings.
Why is Viton so expensive?
Viton, a brand name for a type of fluoroelastomer produced by Chemours (formerly DuPont), is often more expensive than other types of elastomers (like Nitrile or EPDM) due to several factors related to its composition, manufacturing process, and performance characteristics. Here are the key reasons for its higher cost:
1. Complex Chemical Composition: Viton is made from a complex mixture of fluoroelastomers, which are high-performance synthetic rubbers. The raw materials and chemicals used to produce these fluoroelastomers are more costly than those used in simpler elastomers.
2. Advanced Manufacturing Process: The process of producing Viton is more sophisticated and involves additional steps compared to the production of some other common elastomers. This complexity adds to the overall cost of production.
3. Superior Performance Characteristics: Viton offers exceptional resistance to high temperatures, chemicals, and aging. Its ability to maintain integrity in extreme environments means that it can outperform and outlast many other types of rubber, justifying a higher price point for its advanced capabilities.
4. Specialized Applications: Viton is often used in specialized applications that require high-performance materials, such as in the aerospace, automotive, and chemical processing industries. The demands of these applications justify the need for a more expensive material.
5. Research and Development Costs: The development of Viton and its various grades involves significant research and development efforts to tailor the material to specific industrial needs. These R&D costs contribute to the higher price.
6. Market Demand and Supply Dynamics: The demand for high-performance materials like Viton in critical applications, combined with the relatively specialized manufacturing capabilities required to produce it, can lead to higher prices.
7. Longevity and Durability: The long service life of Viton can offset its initial higher cost over time, as it may not need to be replaced as frequently as less expensive materials.
In summary, the high cost of Viton is a result of its advanced material properties, complex manufacturing process, and the specialized applications it serves. While it is more expensive upfront, its durability and ability to perform in extreme conditions can provide cost savings over time, reducing the need for frequent replacements and maintenance.