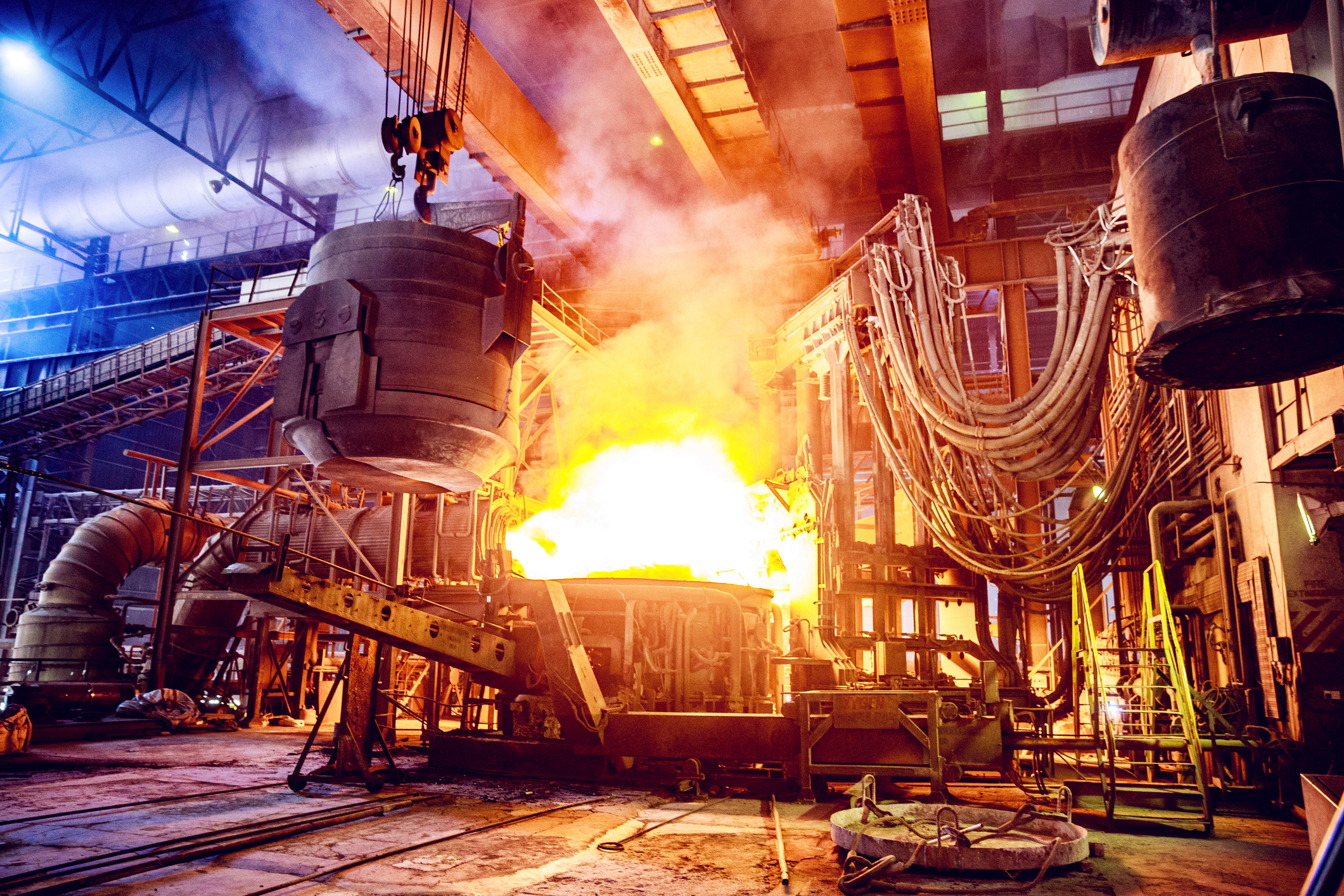
Copper Metal Selection Guide
Copper is a versatile and widely used metal known for its excellent electrical conductivity, thermal conductivity, and corrosion resistance. It has been used by humans for thousands of years and plays a crucial role in various industrial applications. In this web page, we will explore the different types of copper, its numerous advantages and disadvantages, and the diverse industrial uses where copper plays a significant role.
Copper rapid manufacturing, & machined parts are available now!
Check with one of Canyon’s helpful product engineers for an expert material and manufacturing recommendation.
Common names include: Electrolytic Tough Pitch (ETP) Copper, Oxygen-Free Copper (OFC), Phosphor Bronze, Brass (Copper-Zinc Alloy), Bronze (Copper-Tin Alloy), Cupronickel (Copper-Nickel Alloy), Beryllium Copper, Tellurium Copper.

Advantages
- Excellent Electrical Conductivity: Copper is one of the best electrical conductors among metals, making it essential in electrical and electronic applications.
- High Thermal Conductivity: Copper has excellent thermal conductivity, making it suitable for heat exchangers and cooling systems.
- Corrosion Resistance: Copper naturally forms a protective oxide layer, providing good corrosion resistance in most environments.
- Malleability and Ductility: Copper is highly malleable and ductile, allowing for easy shaping and forming into various shapes and sizes.
- Recyclability: Copper is highly recyclable, and recycled copper retains its properties, contributing to sustainability efforts.
- Antimicrobial Properties: Copper surfaces have antimicrobial properties and are used in healthcare settings to reduce the spread of infections.
Disadvantages
- Cost: Copper can be more expensive than some other materials, especially in large-scale applications.
- Low Strength: Pure copper has lower tensile strength compared to some other metals, requiring larger sections or alloys for increased strength.
- Weight: Copper is relatively heavy, which may not be suitable for applications where weight reduction is crucial.
- Susceptibility to Stress Corrosion Cracking: Copper alloys can be susceptible to stress corrosion cracking in specific environments, requiring proper material selection and protection.
Common Applications of Copper
- Electrical and Electronics: Copper is extensively used in electrical wiring, cables, and printed circuit boards due to its excellent electrical conductivity.
- Plumbing and HVAC: Copper pipes and tubing are commonly used in plumbing and heating, ventilation, and air conditioning (HVAC) systems due to their corrosion resistance.
- Construction: Copper roofing, cladding, and architectural elements are used for their aesthetic appeal and durability.
- Automotive: Copper is used in various automotive components, including radiators, connectors, and electrical systems.
- Marine: Copper-nickel alloys are used in marine applications for their corrosion resistance in saltwater environments.
- Heat Exchangers: Copper is used in heat exchangers for its excellent thermal conductivity.
- Coins and Currency: Copper and copper alloys are used in coinage and currency due to their durability and antimicrobial properties.
- Healthcare: Copper surfaces are used in healthcare settings to reduce the spread of infections.
Please consult a Canyon Components Engineer about your specific application and we will use our decades of experience to formulate a solution that fits your need.
Types of Copper
Copper can come in different variations, depending on its composition and intended use. Some common types of Copper include the following.
Canyon Components strives to meet all customer service requests. Feel free to contact Canyon Components engineering and let our knowledgeable staff help you design the perfect part for your needs.
Electrolytic Tough Pitch (ETP) Copper
This highly pure form of copper is known for its excellent conductivity of electricity and heat, making it ideal for electrical wiring, motors, and generators. ETP copper is also easily fabricated and welded, making it versatile for various industrial applications.
Oxygen-Free Copper (OFC)
With very low oxygen content, OFC offers superior electrical and thermal conductivity and is less prone to embrittlement when heated. It's used in high-quality audiovisual systems, semiconductor manufacturing, and specialized electrical applications where high conductivity is crucial.
Phosphor Deoxidized Copper (DHP/C122)
Containing a small amount of phosphorus, DHP copper has good corrosion resistance and is easily welded, making it suitable for use in plumbing, heating, and cooling systems. Its deoxidized nature prevents hydrogen embrittlement and makes it ideal for applications involving welding and brazing.
Beryllium Copper
Known for its high strength and hardness, beryllium copper is used in applications where durability and resistance to stress are required, such as in aerospace components, oil and gas equipment, and precision instruments. It also has good electrical and thermal conductivity.
Tellurium Copper
Characterized by its enhanced machinability, tellurium copper is ideal for intricate parts where detailed machining is required. It's commonly used in electrical connectors, plumbing fittings, and in the production of hot forged products.
Brass (Copper-Zinc Alloy)
Brass, an alloy of copper and zinc, offers excellent corrosion resistance, malleability, and acoustic properties. It’s widely used in musical instruments, decorative items, and fittings. The proportion of zinc varies to create a range of brasses with differing properties to suit various applications.
Please consult a Canyon Components Engineer about your specific application and we will use our decades of experience to formulate a solution that fits your need.
Manufacturing Options for Copper
Copper parts can be manufactured using several methods, each suitable for different applications and part complexities.
Each of these methods has its own advantages, limitations, and cost implications. The choice of manufacturing technique usually depends on factors like the complexity of the design, required precision, material properties, and production volume.
Canyon Components strives to meet all customer service requests. Feel free to contact Canyon Components engineering and let our knowledgeable staff help you design the perfect part for your needs.
Back to Metals Hub
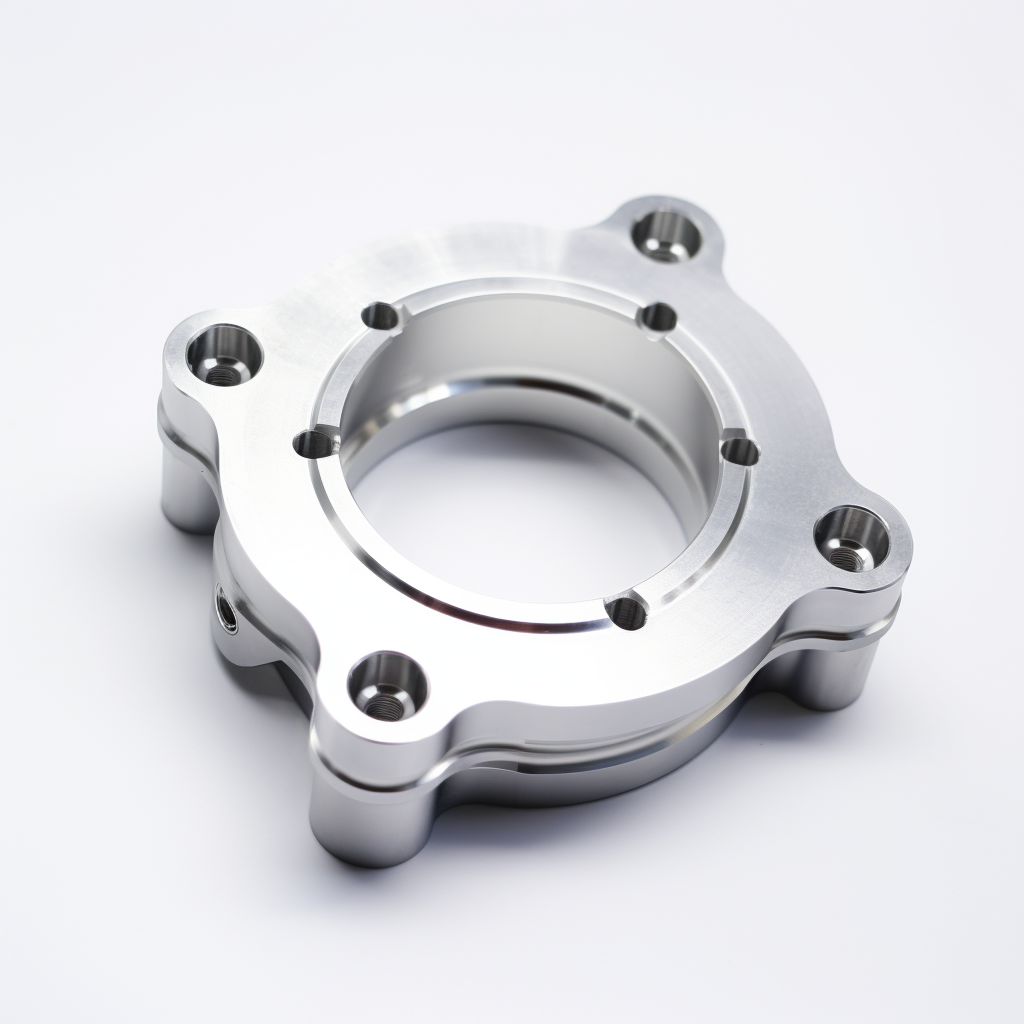
Get A Quote Now!
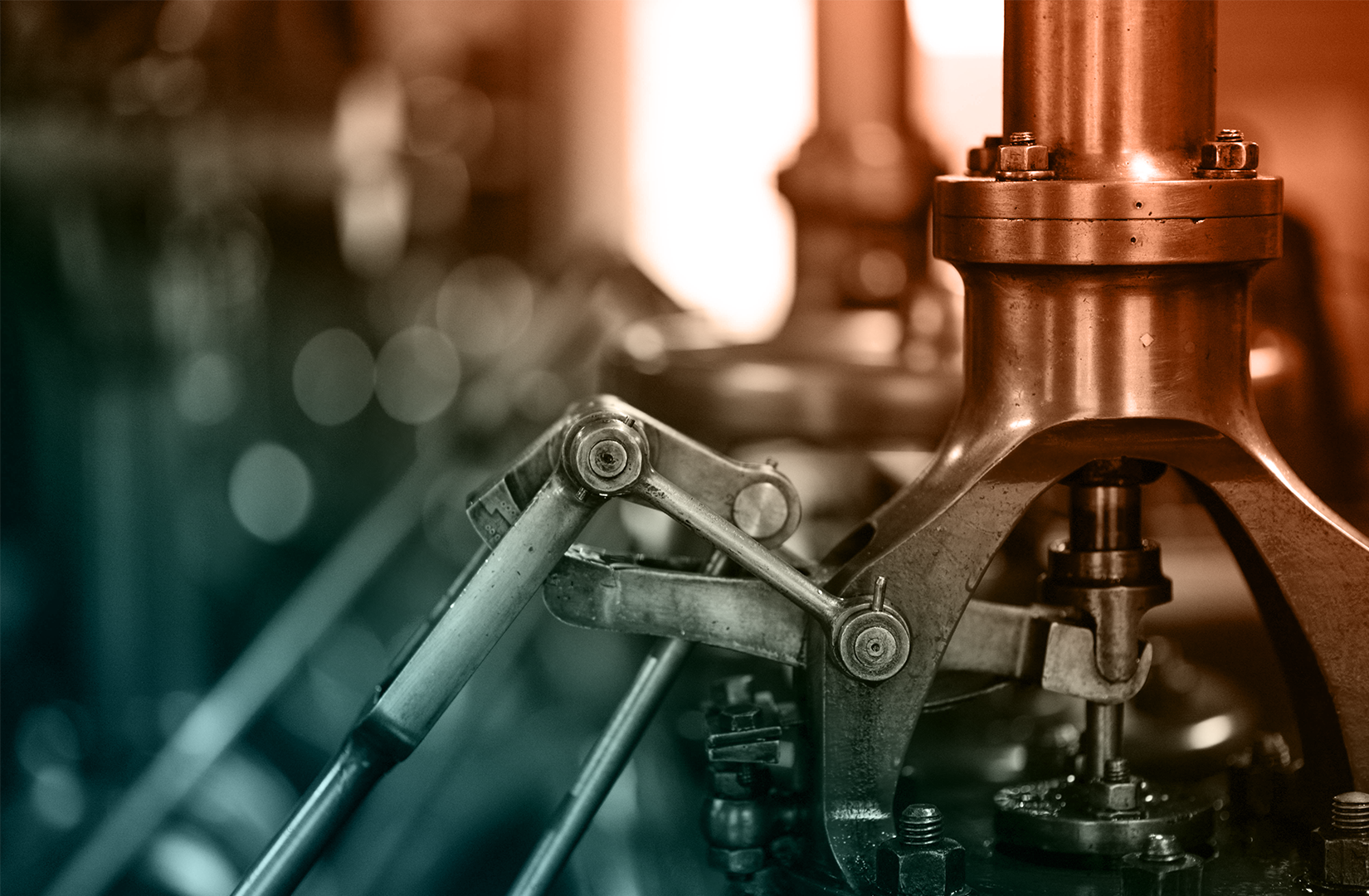
Groove Design References
Learn More
Coatings, Packaging, & Other Services
Learn More
Custom Parts & Custom O-rings
Learn More