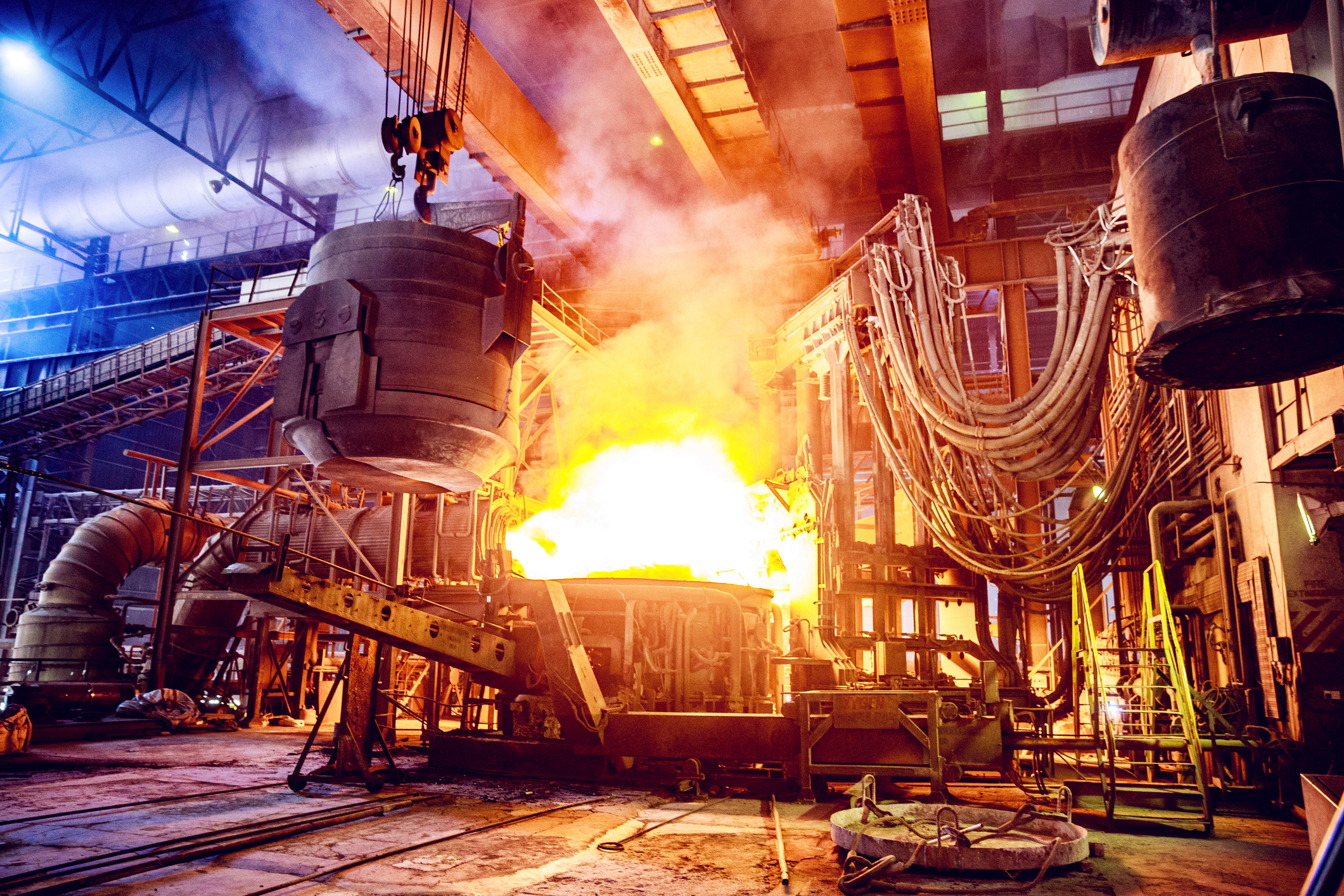
Medical & Pharmaceutical Grade O-ring Materials
In the fields of medicine and pharmaceuticals, the quality and safety of materials used are of paramount importance. Medical and pharmaceutical grade materials are designed and manufactured to meet rigorous standards, ensuring that they do not compromise patient health. In this web page, we will delve into the significance of medical and pharmaceutical grade materials, common application considerations, and discuss the USP Class VI 87 & 88 standards that govern these materials.
With Canyon Components, you can be sure that high quality materials that meet you needs are always readily available. Custom & standard Medical & Pharmaceutical Grade Materials available now!
Check with one of Canyon’s helpful product engineers for an expert material and manufacturing recommendation.
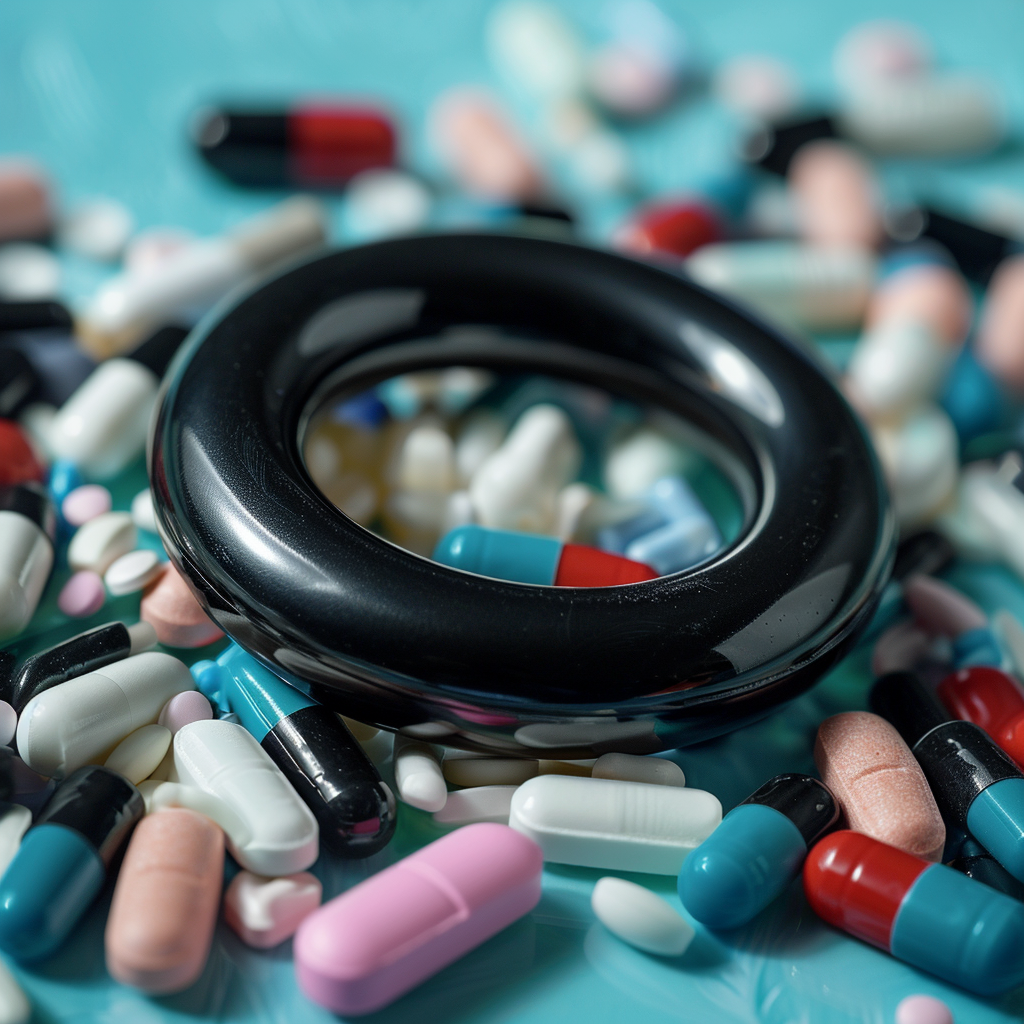
Medical & Pharmaceutical Materials Available
Thousands of Medical & Pharmaceutical Grade Materials are available now with Canyon Components! Some common Medical & Pharmaceutical Grade Materials include the following.
This table shows many of our standard materials and links out to our O-ring store. Get in touch with us if you need a custom gasket, custom molded part, or non-standard geometry!
Filter by
Temperature Search (°C)
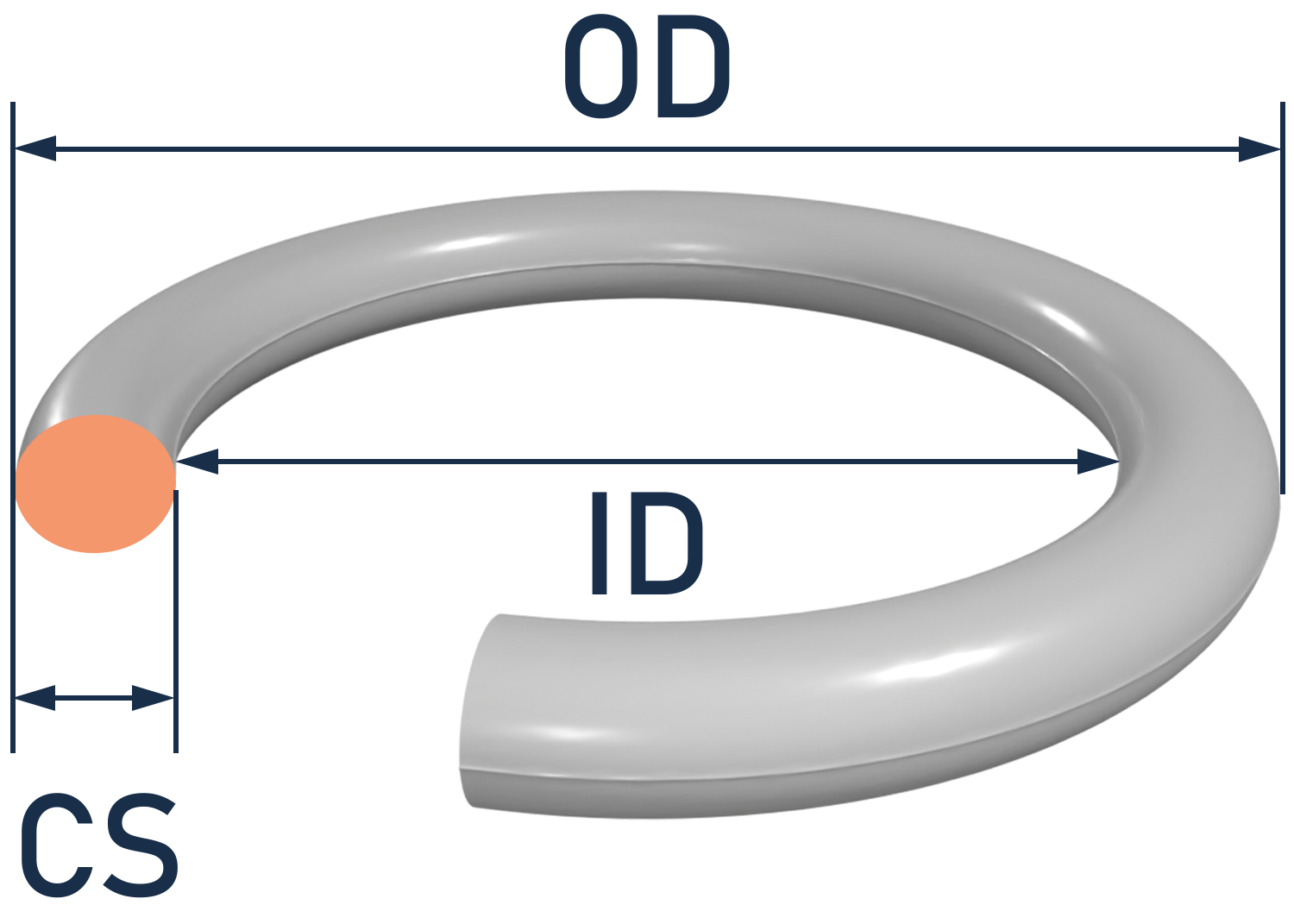
Please consult a Canyon Components Engineer about your specific application and we will use our decades of experience to formulate a solution that fits your need.
What are Medical & Pharmaceutical Grade Materials?
- Medical and pharmaceutical grade materials are substances, components, or equipment specifically engineered to meet the stringent requirements of the healthcare and pharmaceutical industries. These materials must be biocompatible, non-toxic, and free from contaminants to ensure patient safety and the efficacy of pharmaceutical products.
Common Considerations
- Biocompatibility: Materials must be biocompatible, meaning they do not cause adverse reactions when in contact with living tissues, blood, or bodily fluids.
- Purity and Sterility: Materials should be pure and sterile to prevent contamination of pharmaceutical products and minimize the risk of infections or adverse reactions in medical applications.
- Chemical Compatibility: Materials must be chemically compatible with the drugs, chemicals, and processes they come into contact with, ensuring product stability and efficacy.
- Traceability: Materials should be traceable to ensure quality control, batch tracking, and recall procedures in case of issues.
- Regulatory Compliance: Compliance with regulatory standards, such as the USP Class VI 87 & 88, is essential to meet the strict requirements of the healthcare and pharmaceutical industries.
Key Standards
- USP Class VI: USP Class VI materials undergo an array of cytotoxicity tests that aim to certify that a material is biocompatible by proving that it doesn't leach any chemicals that have harmful reactions or long term bodily effects. These tests are designed to assess systemic biological reactivity when the material in question makes contact with mammalian cells. It's commonly used for O-rings, gaskets, & custom molded parts.
- USP Class VI <87>: USP Class VI <87> is a set of in-vitro cytotoxicity tests involving agar diffusion, elution assays, and direct contact. It's commonly used for O-rings, gaskets, & custom molded parts.
- USP Class VI <88>: USP Class VI <88> is a set of in-vivo cytotoxicity tests involving direct implantation, intracutaneous injection, and systemic injection studies. It's commonly used for O-rings, gaskets, & custom molded parts.
Please consult a Canyon Components Engineer about your specific application and we will use our decades of experience to formulate a solution that fits your need.
Medical & Pharmaceutical
USP Class VI Materials
Explore USP Class VI materials for medical devices, pharmaceuticals, and food processing, ensuring safety and purity.
ISO 10993-1
Discover ISO 10993-1 materials, certified for biocompatibility in medical devices, ensuring safety and performance.
Vacuum Baking & Cleaning
Explore our specialized services: vacuum baking for material degassing, ultrasonic cleaning for precision parts, and custom bagging for product protection. Request a quote today!
Clean Room Manufactured Materials
Discover clean room manufactured material features, applications, and how they meet strict cleanliness standards in medical, pharmaceutical, and semiconductor environments.
Medical & Pharmaceutical Materials Available
Click here to see some of our most commonly served industries!
Each of these materials has its own advantages, limitations, and cost implications. The choice of material usually depends on factors like chemical compatibility, temperature, pressure, dynamic or static use, and specification requirements.
Canyon Components strives to meet all customer service requests. Feel free to contact Canyon Components engineering and let our knowledgeable staff help you design the perfect part for your needs.
Please consult a Canyon Components Engineer about your specific application and we will use our decades of experience to formulate a solution that fits your need.
Back to Industries Hub
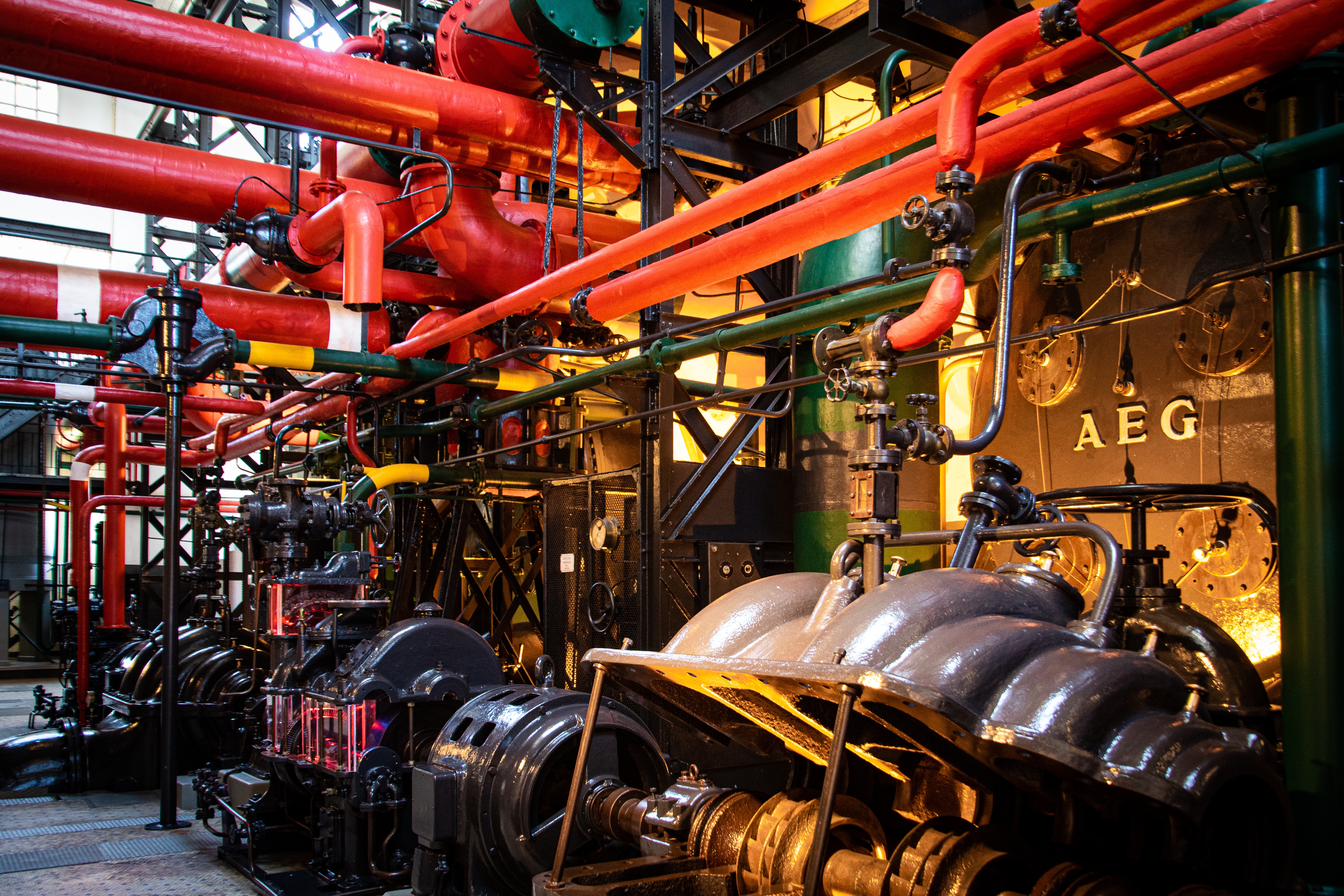
Get A Quote Now!
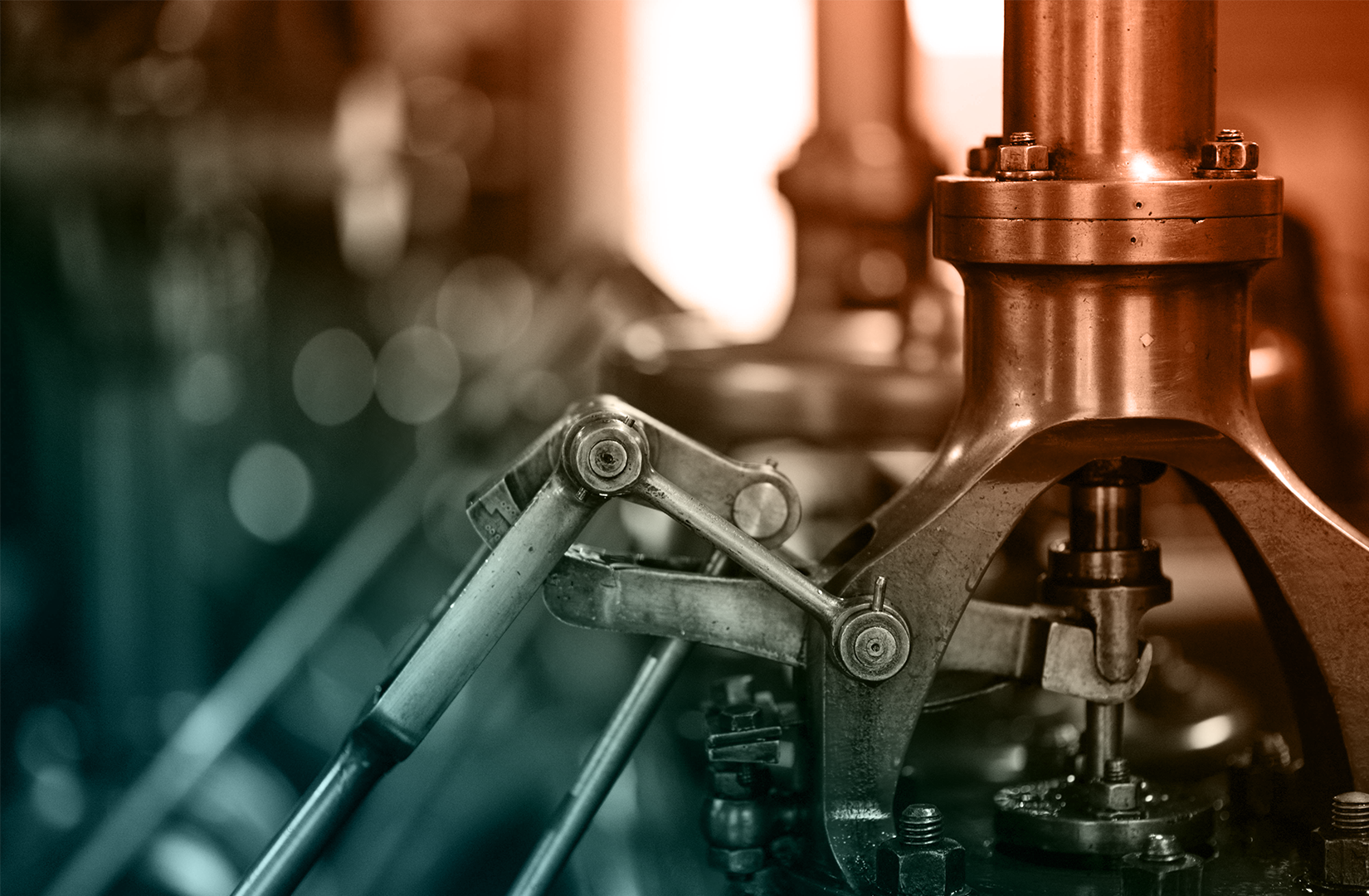
Groove Design References
Learn More
Coatings, Packaging, & Other Services
Learn More
Custom Parts & Custom O-rings
Learn More