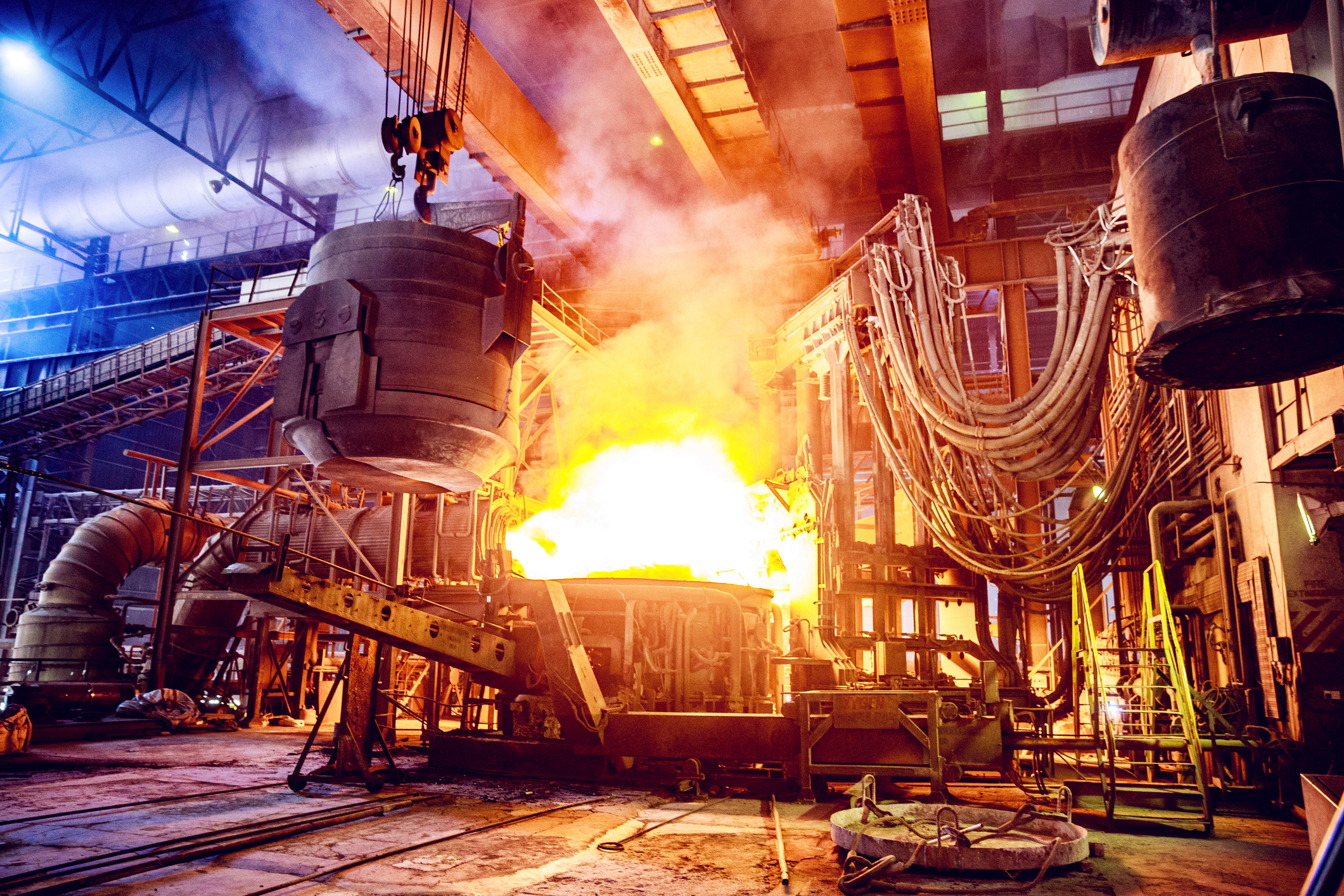
Military, Aerospace, & Automotive Grade Materials
In the military, aerospace, and automotive industries, materials play a pivotal role in ensuring safety, performance, and reliability. Military, aerospace, & automotive grade materials are specifically designed and rigorously tested to meet the demanding requirements of these sectors. In this web page, we will explore the significance of these materials, common application considerations, and discuss the different types used across these industries.
With Canyon Components, you can be sure that high quality materials that meet you needs are always readily available. Custom & standard Military, Aerospace, & Automotive Grade Materials available now!
Check with one of Canyon’s helpful product engineers for an expert material and manufacturing recommendation.
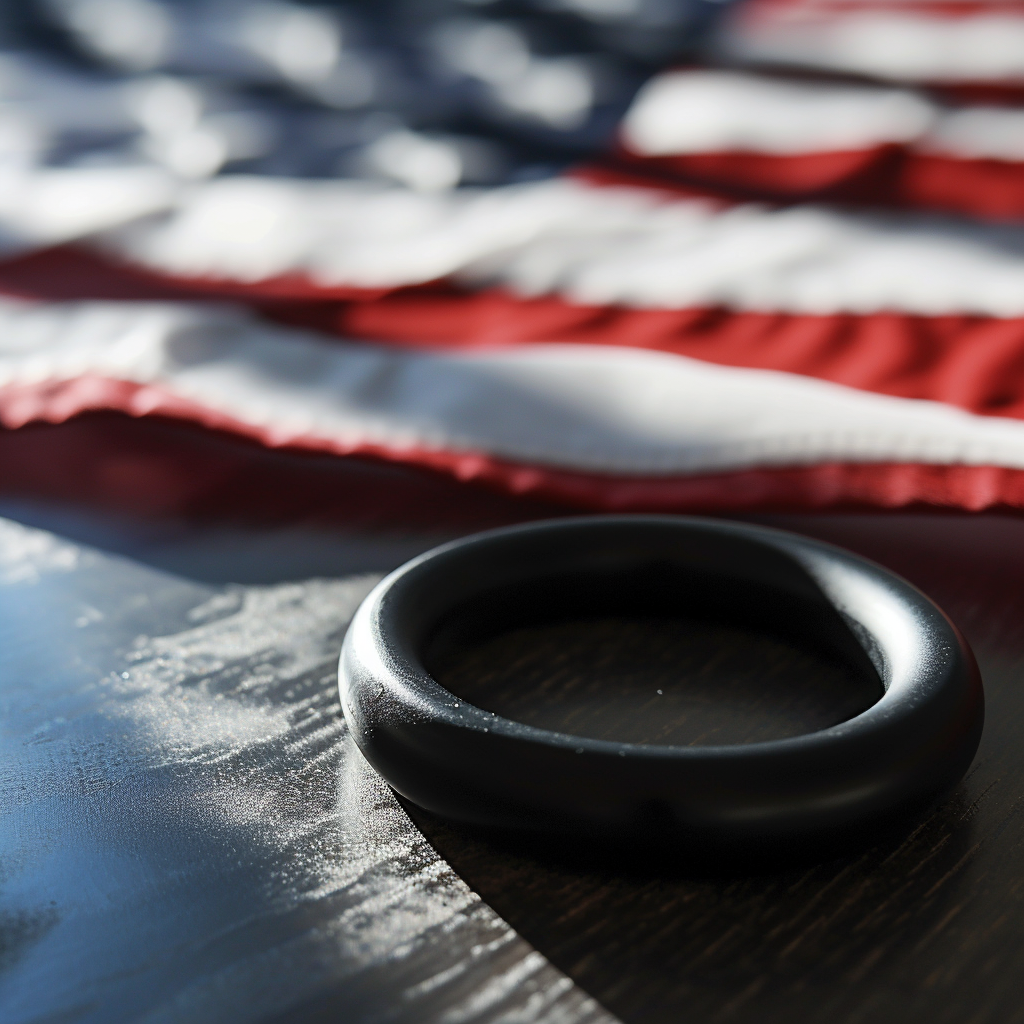
Military, Aerospace, & Automotive Materials Available
Thousands of Military, Aerospace, & Automotive Grade Materials are available now with Canyon Components! Some common Military, Aerospace, & Automotive Grade Materials include the following.
This table shows many of our standard materials and links out to our O-ring store. Get in touch with us if you need a custom gasket, custom molded part, or non-standard geometry!
Filter by
Temperature Search (°C)
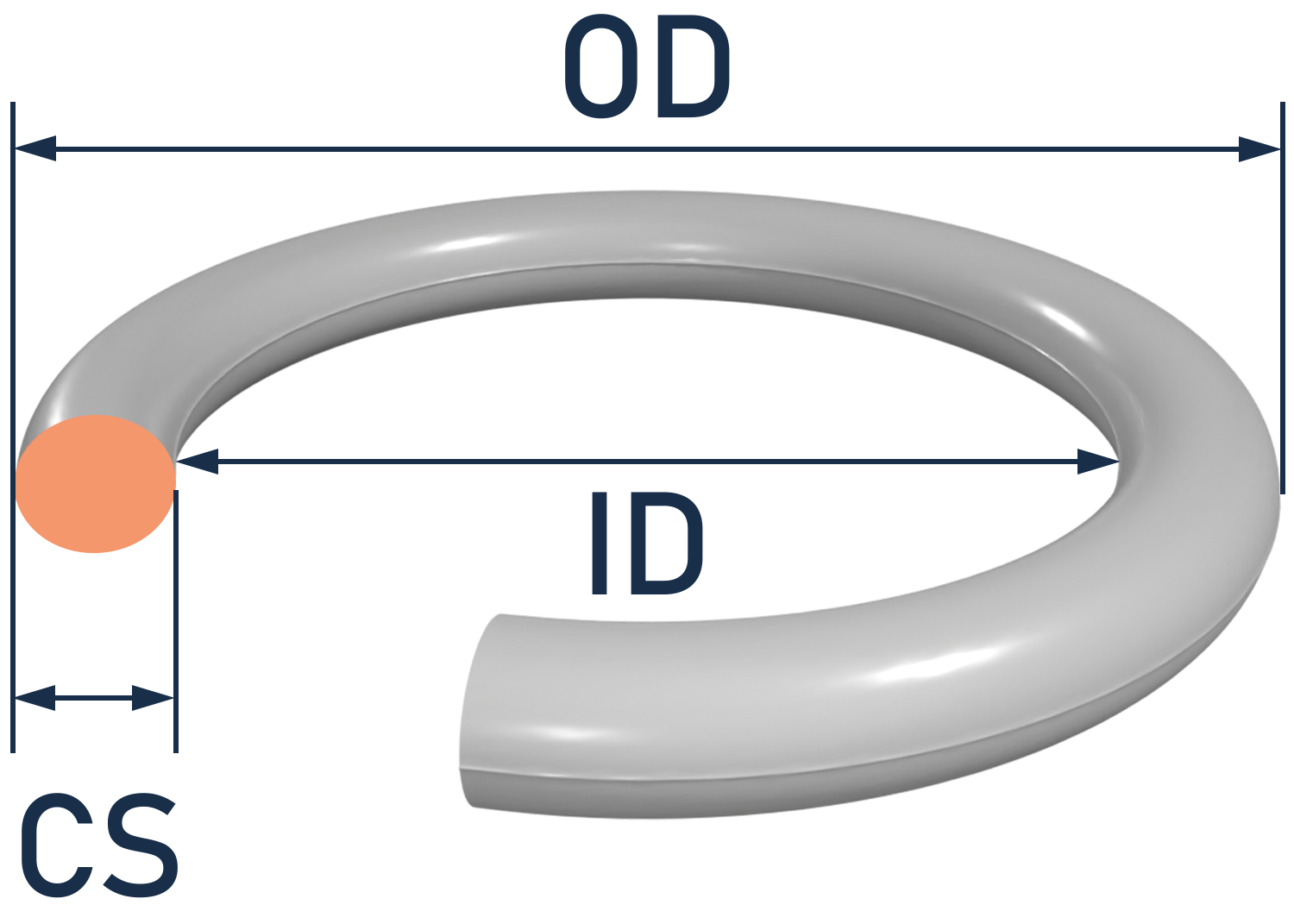
Please consult a Canyon Components Engineer about your specific application and we will use our decades of experience to formulate a solution that fits your need.
What are Military, Aerospace, & Automotive Grade Materials?
- Military, aerospace, & automotive grade materials are substances, components, or equipment engineered to excel in the challenging and high-performance environments of these sectors. These materials must meet strict criteria for strength, durability, thermal stability, and safety.
Common Considerations
- Weight and Strength: Materials must strike a balance between low weight and high strength to meet the stringent weight restrictions in aerospace and automotive applications.
- Thermal Performance: Thermal stability and resistance to extreme temperatures are crucial, particularly in aerospace and automotive engine components.
- Durability and Reliability: Materials must withstand rigorous testing, vibrations, and mechanical stresses, ensuring long-term durability and reliability.
- Safety and Security: Materials should comply with safety standards and regulations, ensuring the protection of personnel and assets.
- Cost-Efficiency: While performance is vital, cost considerations are essential to optimize material selection and production processes.
Material Options
Fluorosilicone:
- Military: Fluorosilicone is used in military applications for its resistance to fuel, oil, and solvents, particularly in fuel systems and various seals.
- Aerospace: In aerospace, it's valued for its wide temperature range and resistance to fuels and degradation in harsh environments, making it suitable for seals and gaskets in aircraft.
- Automotive: For the automotive industry, fluorosilicone finds use in fuel systems and transmission components due to its resistance to petroleum oils and fuel.
EPDM (Ethylene Propylene Diene Monomer):
- Military: EPDM's durability and weather resistance make it suitable for outdoor military equipment and vehicles, protecting against water, UV, and temperature variations.
- Aerospace: In aerospace, EPDM is used for its excellent resistance to ozone, weathering, and aging, ideal for window seals, hoses, and insulation materials in certain aircraft applications.
- Automotive: In automotive applications, EPDM is commonly used for weatherstripping, door seals, and hoses due to its resistance to ozone, coolants, and heat.
NBR (Nitrile Butadiene Rubber):
- Military: NBR is used in military applications for gaskets and seals in fuel handling systems because of its resistance to oils and fuels.
- Aerospace: It's utilized in aerospace for components like fuel hoses and seals, offering good resistance to oils and various hydrocarbons.
- Automotive: In the automotive industry, NBR is prevalent in fuel and oil handling systems, like fuel hoses, gaskets, and O-rings, due to its oil resistance.
Silicone:
- Military: Silicone's flexibility and high-temperature resistance make it ideal for military electronic components and seals in extreme environments.
- Aerospace: Widely used in aerospace for its thermal stability and low outgassing properties, silicone is ideal for seals, gaskets, and insulation in aircraft.
- Automotive: In automotive, silicone is used for hoses, gaskets, and seals, particularly in high-temperature areas like engine compartments.
FKM (Fluorocarbon Rubber):
- Military: FKM is used for seals and gaskets in military vehicles and equipment due to its excellent resistance to high temperatures, fuels, and chemicals.
- Aerospace: In aerospace, it's used for O-rings, seals, and gaskets, especially in fuel systems and engines, due to its resistance to jet fuel, hydraulic fluids, and high temperatures.
- Automotive: FKM finds application in automotive fuel systems, transmission seals, and O-rings, thanks to its resistance to high temperatures and various fluids.
EMI & RFI Shielding Materials:
- Military: These materials are critical in military applications for protecting sensitive electronic equipment from electromagnetic interference and radio frequency interference.
- Aerospace: In aerospace, they are used in aircraft electronics and communication systems to prevent interference and ensure the reliability of onboard systems.
- Automotive: In the automotive sector, EMI and RFI shielding materials are used in electronic systems to prevent interference with critical vehicle functions and communication systems.
Please consult a Canyon Components Engineer about your specific application and we will use our decades of experience to formulate a solution that fits your need.
Military, Aerospace, & Automotive
Glossary of Specifications
Explore our Glossary of Specifications, offering clear definitions and explanations of key industry standards and certifications. Learn how these specifications impact material selection and compliance in various industries.
AMS (Aerospace Material Specification)
Learn about AMS (Aerospace Material Specification) materials, designed to meet rigorous standards for aviation and aerospace industries. Discover their features, compliance, and how they ensure performance and safety in critical applications.
Mil-Spec Elastomeric Materials
Discover Mil-Spec elastomeric materials, engineered to meet stringent military specifications for strength, durability, and precision. Learn about their features, compliance, and how they perform in extreme conditions for defense applications.
USA Manufactured Parts
Discover high-quality O-rings, rubber, plastic, and metal parts manufactured in the USA. Learn about our commitment to American-made products that meet rigorous quality standards for diverse industries.
Military, Aerospace, & Automotive Materials Available
Click here to see some of our most commonly served industries!
Each of these materials has its own advantages, limitations, and cost implications. The choice of material usually depends on factors like chemical compatibility, temperature, pressure, dynamic or static use, and specification requirements.
Canyon Components strives to meet all customer service requests. Feel free to contact Canyon Components engineering and let our knowledgeable staff help you design the perfect part for your needs.
Please consult a Canyon Components Engineer about your specific application and we will use our decades of experience to formulate a solution that fits your need.
Back to Industries Hub
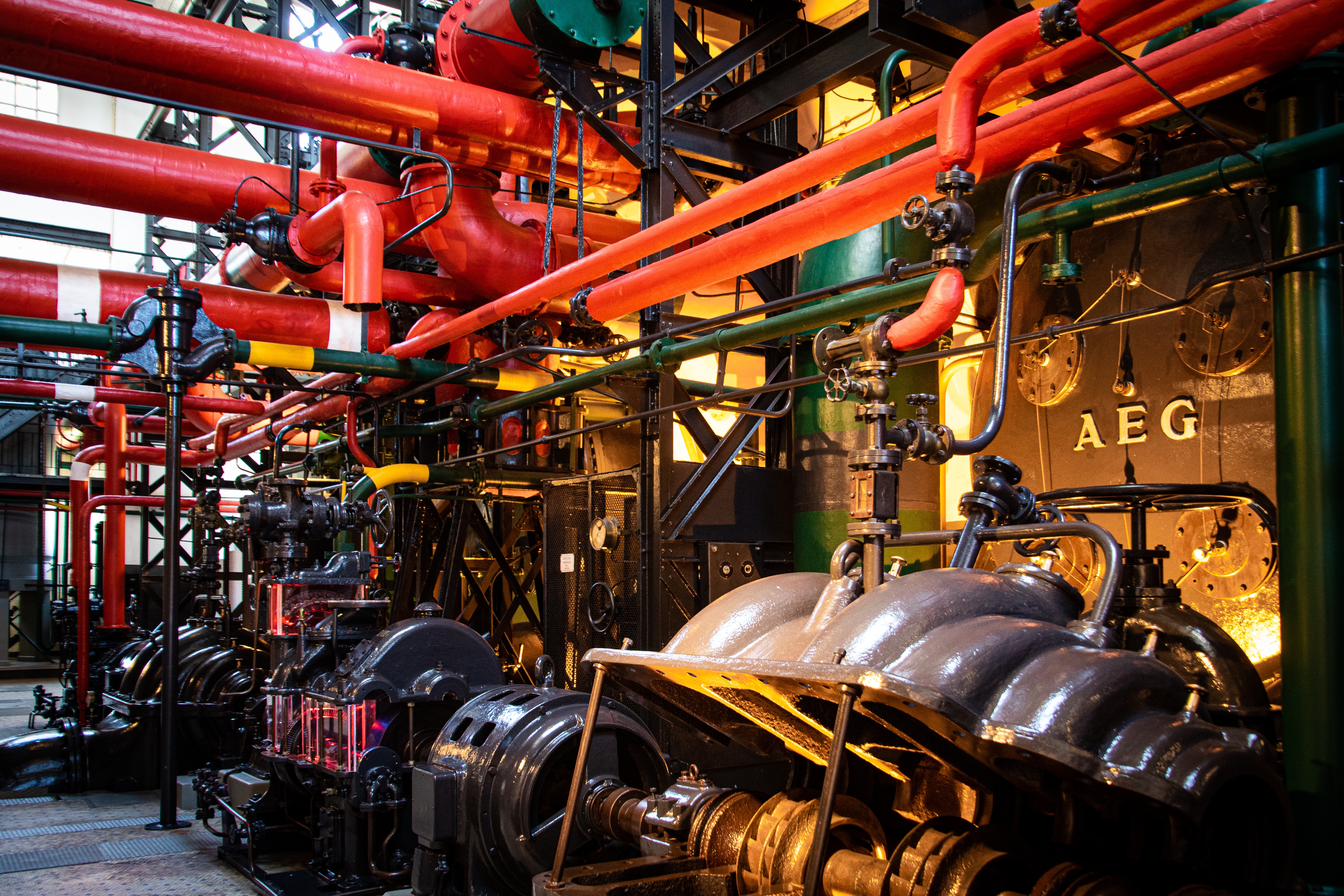
Get A Quote Now!
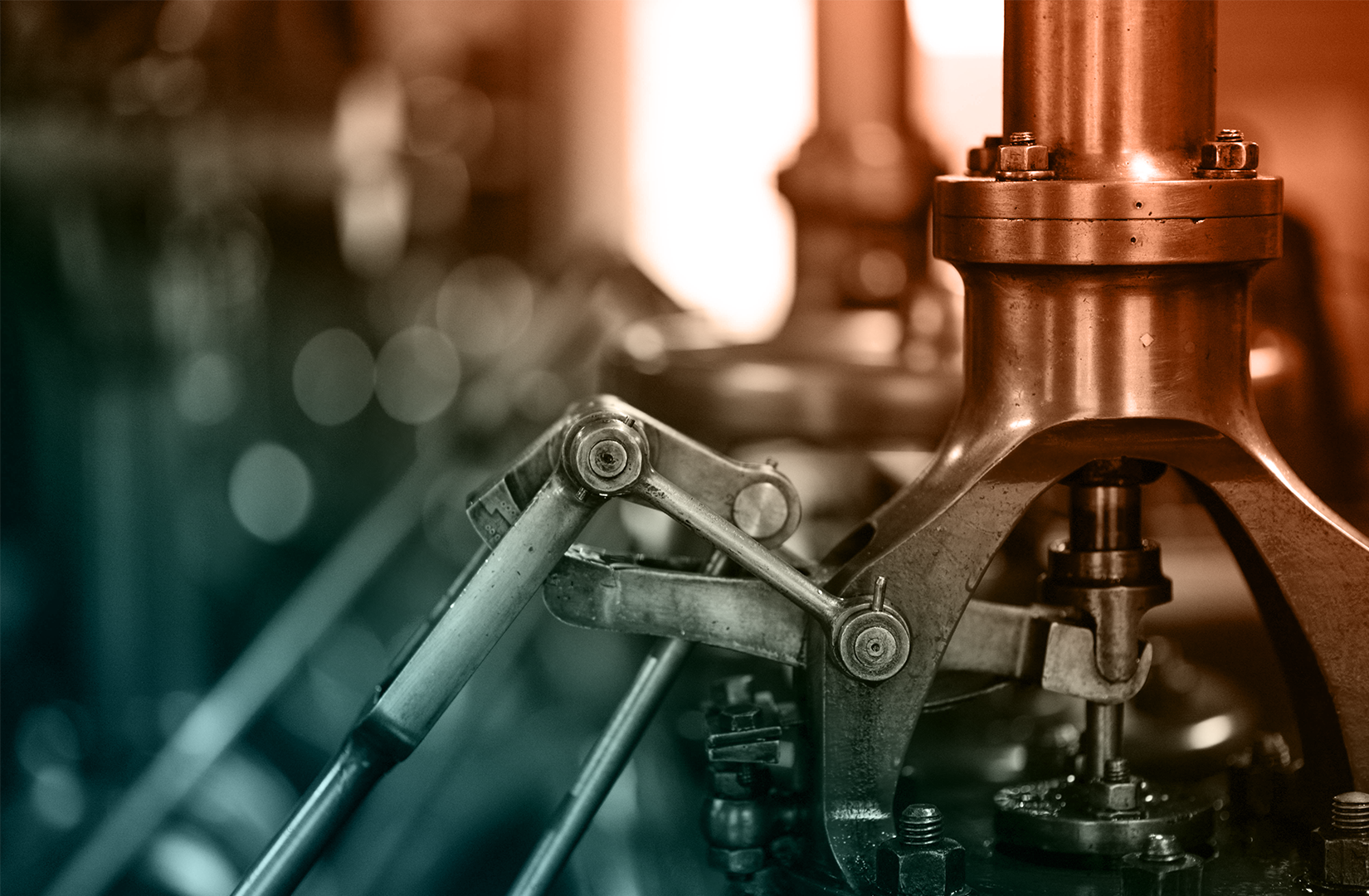
Groove Design References
Learn More
Coatings, Packaging, & Other Services
Learn More
Custom Parts & Custom O-rings
Learn More