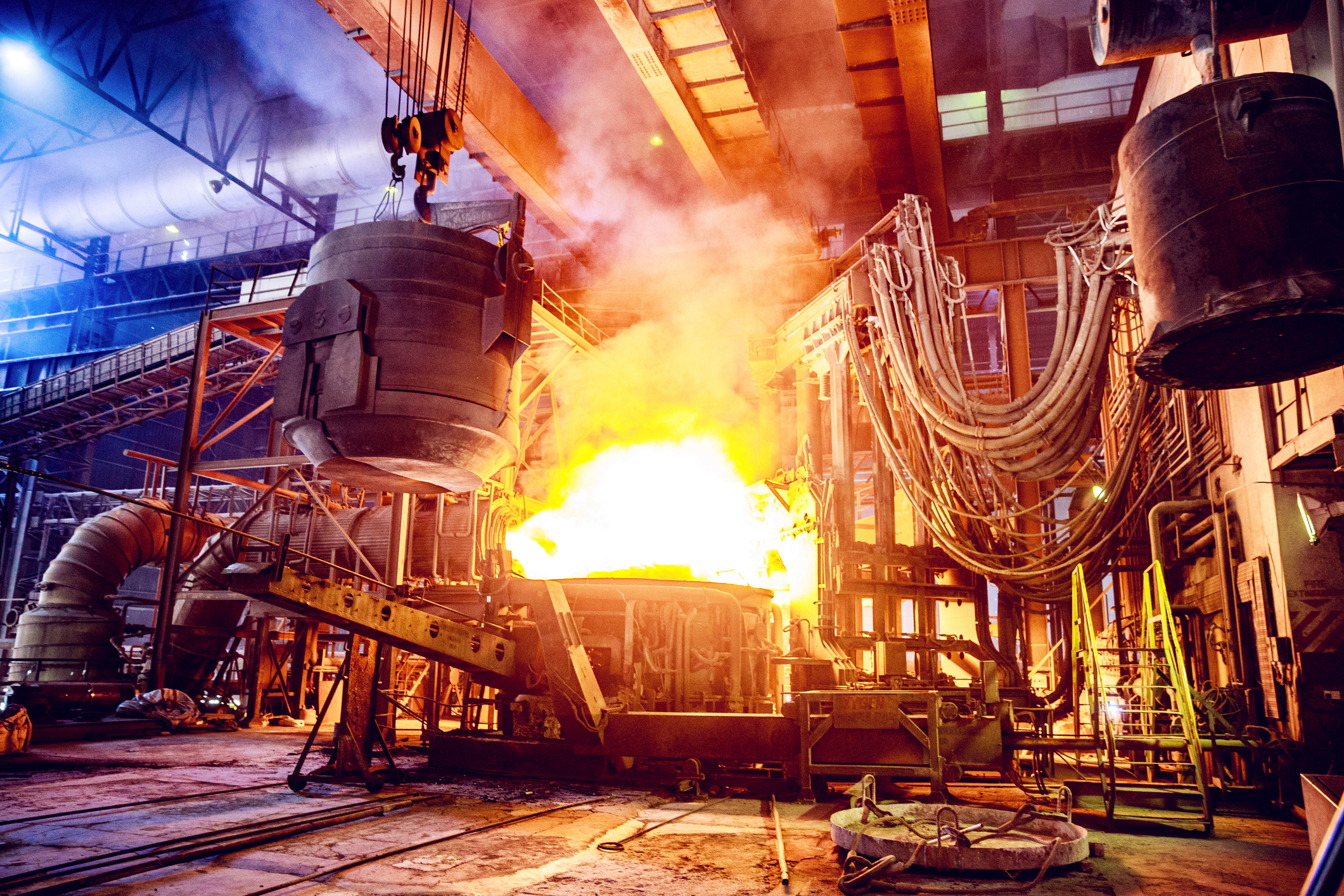
PMMA Plastic (Polymethyl Methacrylate) Selection Guide
PMMA (Polymethyl Methacrylate), commonly known as acrylic or acrylic glass, is a versatile thermoplastic polymer known for its transparency, optical clarity, and resistance to weathering. In this web page, we will explore the different types of PMMA, its numerous advantages and disadvantages, and the diverse industrial applications where PMMA plays a significant role.
PMMA (Polymethyl Methacrylate) rapid manufacturing, & custom molded parts are available now!
Check with one of Canyon’s helpful product engineers for an expert material and manufacturing recommendation.
Common names include: PMMA (Polymethyl Methacrylate), Trade Names: Plexiglas®, Lucite®, Acrylite®, Perspex®, Altuglas®, Optix®.
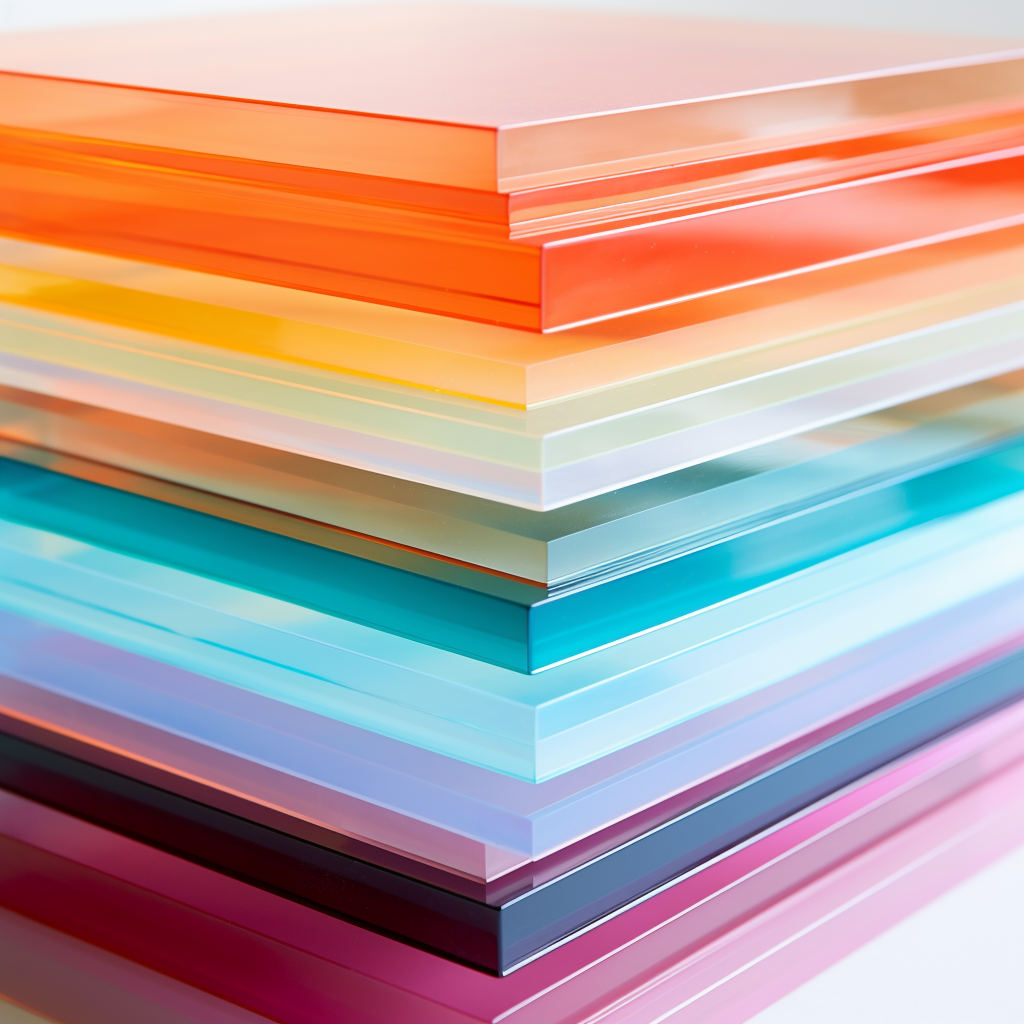
Advantages
- Optical Clarity: PMMA boasts exceptional optical clarity, making it an excellent choice for applications requiring transparency and aesthetics.
- Weather Resistance: PMMA is highly resistant to weathering, including UV radiation, making it suitable for outdoor and architectural applications.
- Ease of Processing: PMMA is easy to process, including cutting, machining, and thermoforming, making it versatile for various manufacturing techniques.
- Lightweight: PMMA is lightweight, which is advantageous in applications where weight is a consideration.
- Chemical Resistance: PMMA is resistant to many chemicals, ensuring its stability in various environments.
- Recyclability: PMMA is recyclable, making it an environmentally friendly option when properly managed.
Disadvantages
- Brittleness: PMMA can be relatively brittle, especially at low temperatures, which may limit its use in impact-critical applications.
- Scratch Sensitivity: PMMA is prone to scratching, so it may require additional coatings or treatments to enhance scratch resistance.
- Not Suitable for High-Temperature Environments: PMMA has a lower heat resistance compared to some other engineering plastics. It may soften or deform at elevated temperatures.
Common Applications of PMMA
- Aerospace: PMMA may find use in aircraft windows and cockpit displays due to its optical properties and lightweight nature.
- Automotive: PMMA is used in automotive applications for headlights, taillights, and interior components due to its optical clarity and weather resistance.
- Medical Devices: PMMA is used in medical device components, such as incubators and dental prosthetics, due to its biocompatibility and optical clarity.
- Construction and Architecture: PMMA is employed in architectural glazing, skylights, and signage due to its optical properties and weather resistance.
- Optical Components: PMMA is used in optical lenses, camera lenses, and eyeglass lenses due to its excellent optical clarity.
- Displays and Screens: PMMA is used for manufacturing screens, display cases, and protective covers for electronic devices due to its transparency and scratch resistance.
- Point-of-Purchase Displays: PMMA is a favored material for creating attractive and durable point-of-purchase displays in retail environments.
- Art and Design: PMMA is used in artistic sculptures, installations, and design projects due to its ease of shaping and optical properties.
Please consult a Canyon Components Engineer about your specific application and we will use our decades of experience to formulate a solution that fits your need.
Types of PMMA
PMMA can come in different variations, depending on its composition and intended use. Some common types of PMMA include the following.
Canyon Components strives to meet all customer service requests. Feel free to contact Canyon Components engineering and let our knowledgeable staff help you design the perfect part for your needs.
General Purpose PMMA
This standard type offers excellent clarity and light transmittance, comparable to glass. It's widely used in applications like display cases, lenses, and aquariums. Resistant to UV light and weathering, it's suitable for both indoor and outdoor applications, providing a balance between aesthetics and durability.
Impact-Modified PMMA
Enhanced for greater impact resistance, this PMMA variant is ideal for applications where durability is key, such as skylights, outdoor signage, and automotive tail lights. It maintains the clarity of standard PMMA while offering increased toughness against physical stress.
Heat-Resistant PMMA
Specially formulated to withstand higher temperatures, this type is used in applications like high-performance lighting fixtures and automotive components that are exposed to heat. It retains its shape and clarity under thermal stress, making it a reliable choice for heat-sensitive environments.
Extruded PMMA
This version is designed for ease of processing and is often used for producing sheets, tubes, and profiles. Extruded PMMA offers excellent surface finish and is commonly used in architectural applications, retail displays, and signage, where aesthetic appeal is essential.
Cast PMMA
Known for its superior optical properties and surface finish, cast PMMA is used in high-quality lenses, artistic installations, and precision engineering components. It offers greater flexibility in terms of size and thickness compared to extruded PMMA and provides exceptional clarity and light transmission.
UV-Curable PMMA
This innovative type is cured using UV light, resulting in enhanced mechanical properties and faster processing times. It's used in applications requiring rapid production, like coatings, adhesives, and dental applications. UV-curable PMMA is notable for its excellent clarity and resistance to yellowing over time.
Please consult a Canyon Components Engineer about your specific application and we will use our decades of experience to formulate a solution that fits your need.
Manufacturing Options for PMMA
PMMA parts can be manufactured using several methods, each suitable for different applications and part complexities.
Each of these methods has its own advantages, limitations, and cost implications. The choice of manufacturing technique usually depends on factors like the complexity of the design, required precision, material properties, and production volume.
Canyon Components strives to meet all customer service requests. Feel free to contact Canyon Components engineering and let our knowledgeable staff help you design the perfect part for your needs.
Back to Plastics Hub
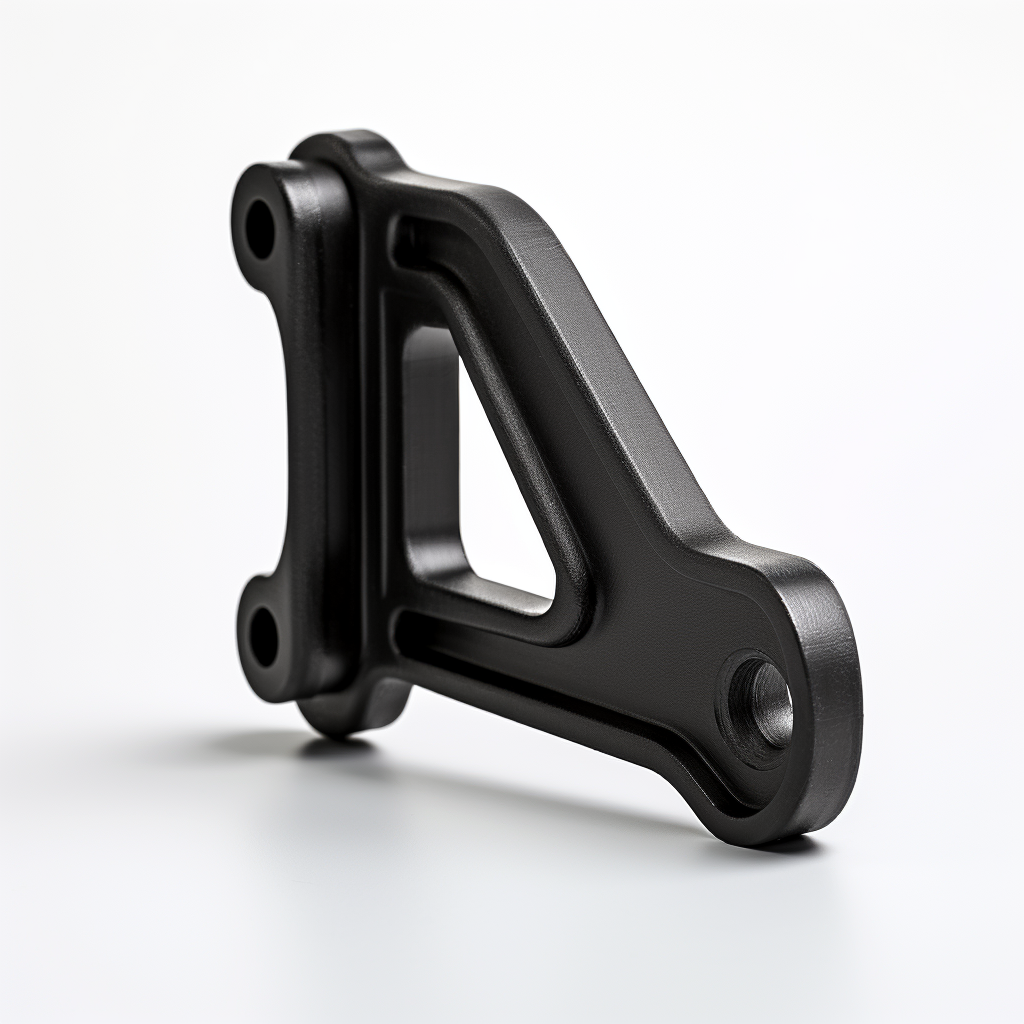
Get A Quote Now!
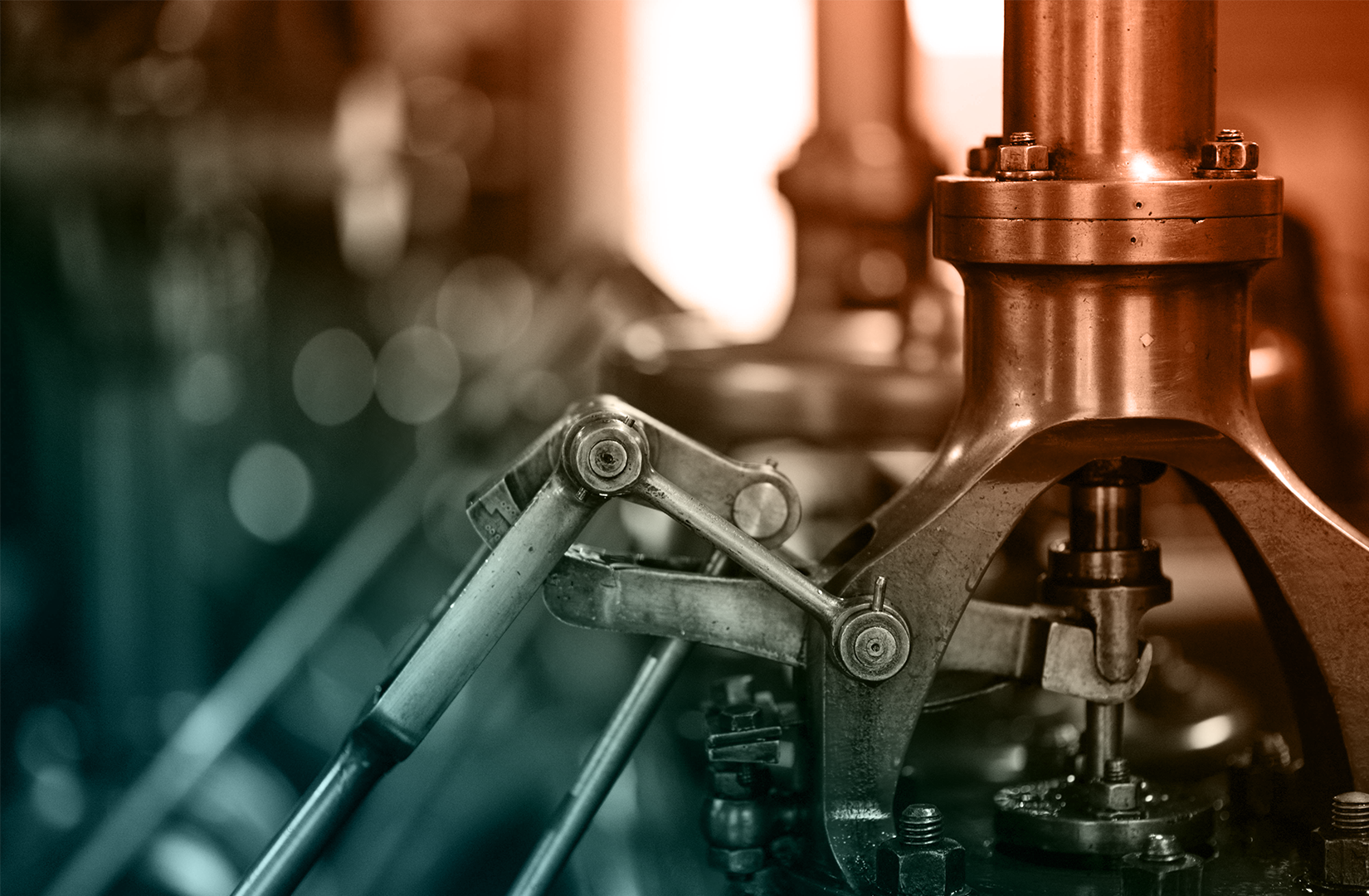
Groove Design References
Learn More
Coatings, Packaging, & Other Services
Learn More
Custom Parts & Custom O-rings
Learn More