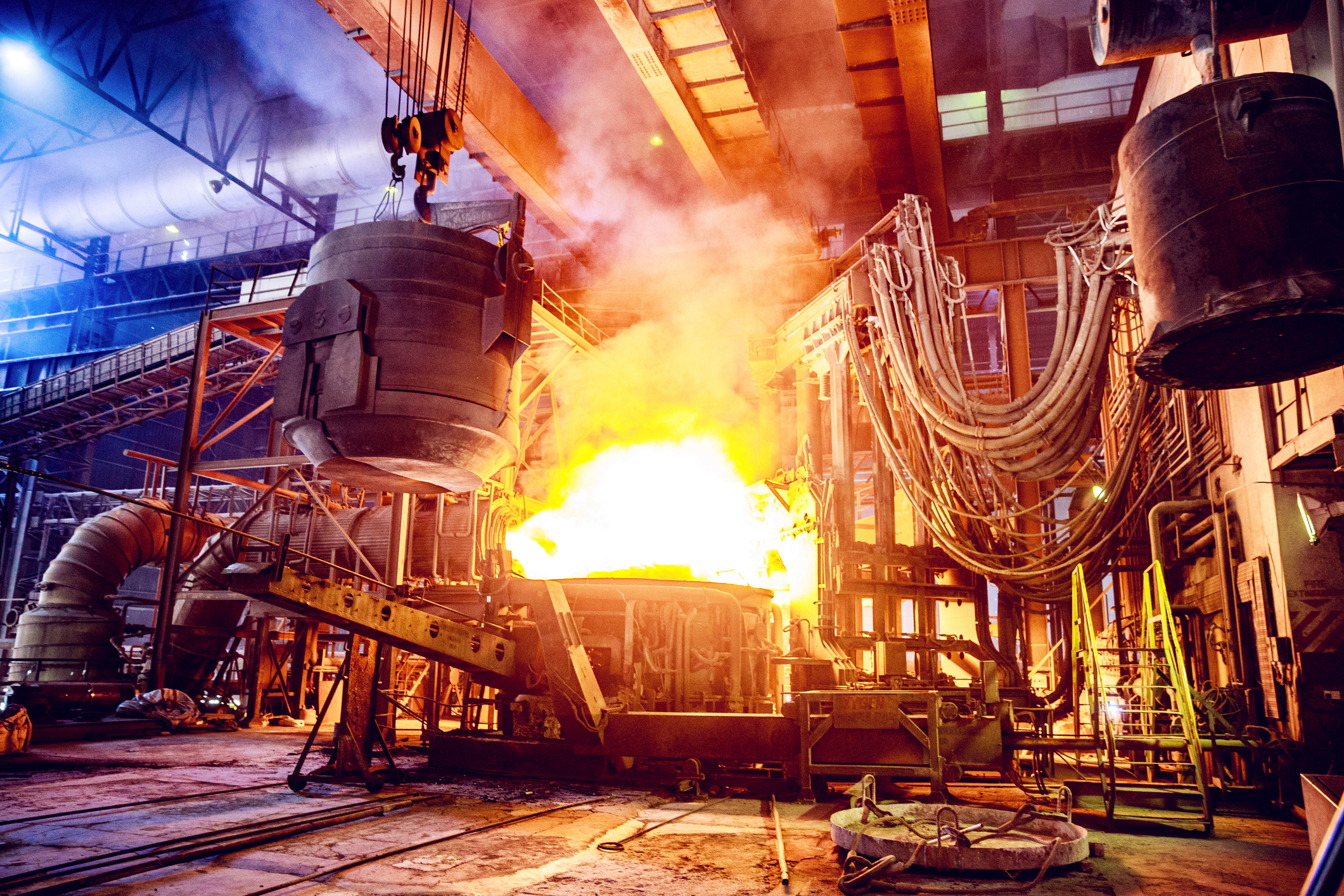
PPSU Plastic (Polyphenylsulfone) Selection Guide
PPSU (Polyphenylsulfone) is a high-performance engineering thermoplastic known for its exceptional heat resistance, chemical resistance, and mechanical properties. In this web page, we will explore the different types of PPSU, its numerous advantages and disadvantages, and the diverse industrial applications where PPSU plays a crucial role.
PPSU (Polyphenylsulfone) rapid manufacturing, & custom molded parts are available now!
Check with one of Canyon’s helpful product engineers for an expert material and manufacturing recommendation.
Common names include: PPSU (Polyphenylsulfone, PPSF), Trade Names: Radel® R, Udel®, Durason® PPSU, Mindel™, Veradel®, Tecason® P.
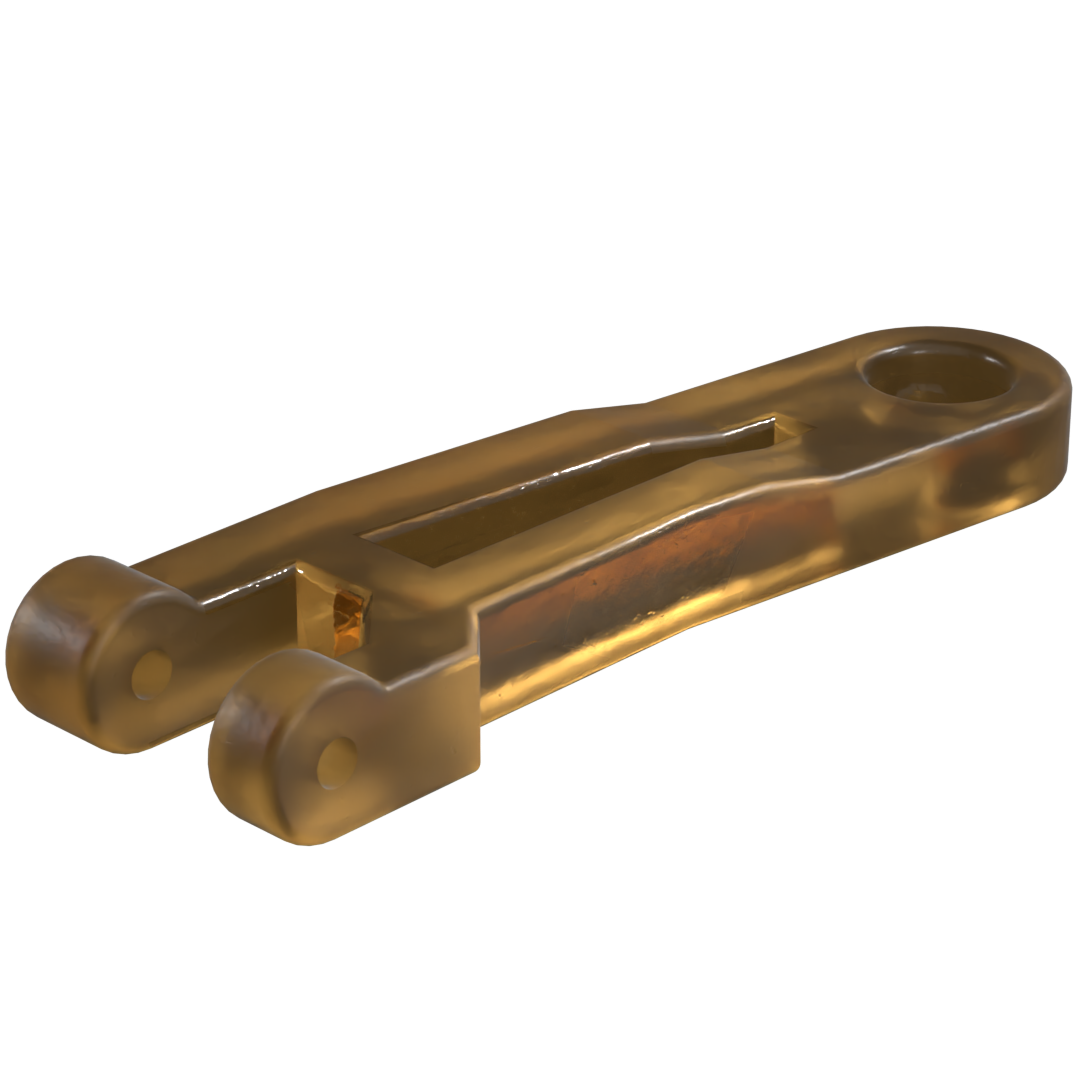
Advantages
- High Heat Resistance: PPSU can withstand high temperatures, making it suitable for use in applications exposed to heat and steam sterilization.
- Excellent Chemical Resistance: PPSU is highly resistant to a wide range of chemicals, acids, bases, and solvents, making it suitable for corrosive environments.
- High Impact Strength: PPSU exhibits excellent impact resistance, even at low temperatures, ensuring durability in demanding applications.
- Dimensional Stability: PPSU has good dimensional stability, maintaining its shape and size under varying temperature conditions.
- Sterilizability: PPSU is suitable for repeated sterilization cycles, making it ideal for use in medical and dental equipment.
- Biocompatibility: PPSU is biocompatible and approved for use in medical and dental applications.
- Low Smoke and Toxicity: PPSU produces low smoke and toxic emissions when burned, making it suitable for certain applications with strict fire safety requirements.
Disadvantages
- Cost: PPSU can be more expensive compared to some other thermoplastics, which can impact its use in cost-sensitive applications.
- Not Suitable for High-Load Bearings: PPSU may not be suitable for applications with extreme high-load bearing requirements, as it may exhibit wear over time.
Common Applications of PPSU
- Medical and Dental: PPSU is used in medical and dental equipment, including surgical instruments, dental instruments, orthopedic devices, and sterilization trays due to its biocompatibility, sterilizability, and chemical resistance.
- Aerospace: PPSU is employed in aerospace applications for components that require high heat resistance, such as aircraft interior parts and electrical connectors.
- Food and Beverage Industry: PPSU is used in food processing equipment, valves, fittings, and components that require heat and chemical resistance.
- Electrical and Electronics: PPSU is used for electrical connectors, insulators, and housings due to its electrical insulating properties and resistance to high temperatures.
- Automotive: PPSU is used in automotive applications for components such as coolant systems, pumps, and sensors due to its heat resistance and durability.
- Oil and Gas Industry: PPSU is employed in oil and gas applications for downhole tools, seals, and connectors due to its resistance to harsh chemicals and high temperatures.
- Plumbing: PPSU is used in plumbing applications for hot water systems, fittings, and valves due to its heat resistance and chemical resistance.
Please consult a Canyon Components Engineer about your specific application and we will use our decades of experience to formulate a solution that fits your need.
Types of PPSU
PPSU can come in different variations, depending on its composition and intended use. Some common types of PPSU include the following.
Canyon Components strives to meet all customer service requests. Feel free to contact Canyon Components engineering and let our knowledgeable staff help you design the perfect part for your needs.
Standard PPSU
Renowned for its high heat resistance and toughness, standard PPSU is ideal for medical and food service applications due to its ability to withstand repeated sterilization. It's also used in aerospace and automotive industries for its high strength-to-weight ratio and resistance to chemicals and steam.
Glass Fiber Reinforced PPSU
By incorporating glass fibers, this type offers enhanced structural strength and stiffness. It's suitable for industrial applications that demand higher load-bearing capacity and dimensional stability, such as in automotive under-hood components and electrical insulators.
Flame Retardant PPSU
This variant includes flame-retardant additives, making it a prime choice for electronic and aerospace applications where fire resistance is critical. It maintains the inherent high-temperature resistance of PPSU while adding an essential layer of safety against fire hazards.
Carbon Fiber Reinforced PPSU
Integrating carbon fibers significantly increases the material's strength and thermal stability. This makes it ideal for lightweight, high-strength applications in aerospace and advanced automotive engineering, where minimizing weight without sacrificing durability is essential.
UV-Stabilized PPSU
Designed to resist UV radiation, this type is perfect for outdoor applications, including aircraft and vehicle exteriors, where prolonged exposure to sunlight is a concern. It retains the mechanical properties of PPSU while preventing degradation and discoloration from UV exposure.
Mineral Filled PPSU
Incorporating mineral fillers enhances the thermal properties and dimensional stability of PPSU, making it suitable for precision components in electronics and automotive industries. This type offers improved rigidity and thermal conductivity, ideal for applications requiring enhanced heat dissipation.
Please consult a Canyon Components Engineer about your specific application and we will use our decades of experience to formulate a solution that fits your need.
Manufacturing Options for PPSU
PPSU parts can be manufactured using several methods, each suitable for different applications and part complexities.
Each of these methods has its own advantages, limitations, and cost implications. The choice of manufacturing technique usually depends on factors like the complexity of the design, required precision, material properties, and production volume.
Canyon Components strives to meet all customer service requests. Feel free to contact Canyon Components engineering and let our knowledgeable staff help you design the perfect part for your needs.
Back to Plastics Hub
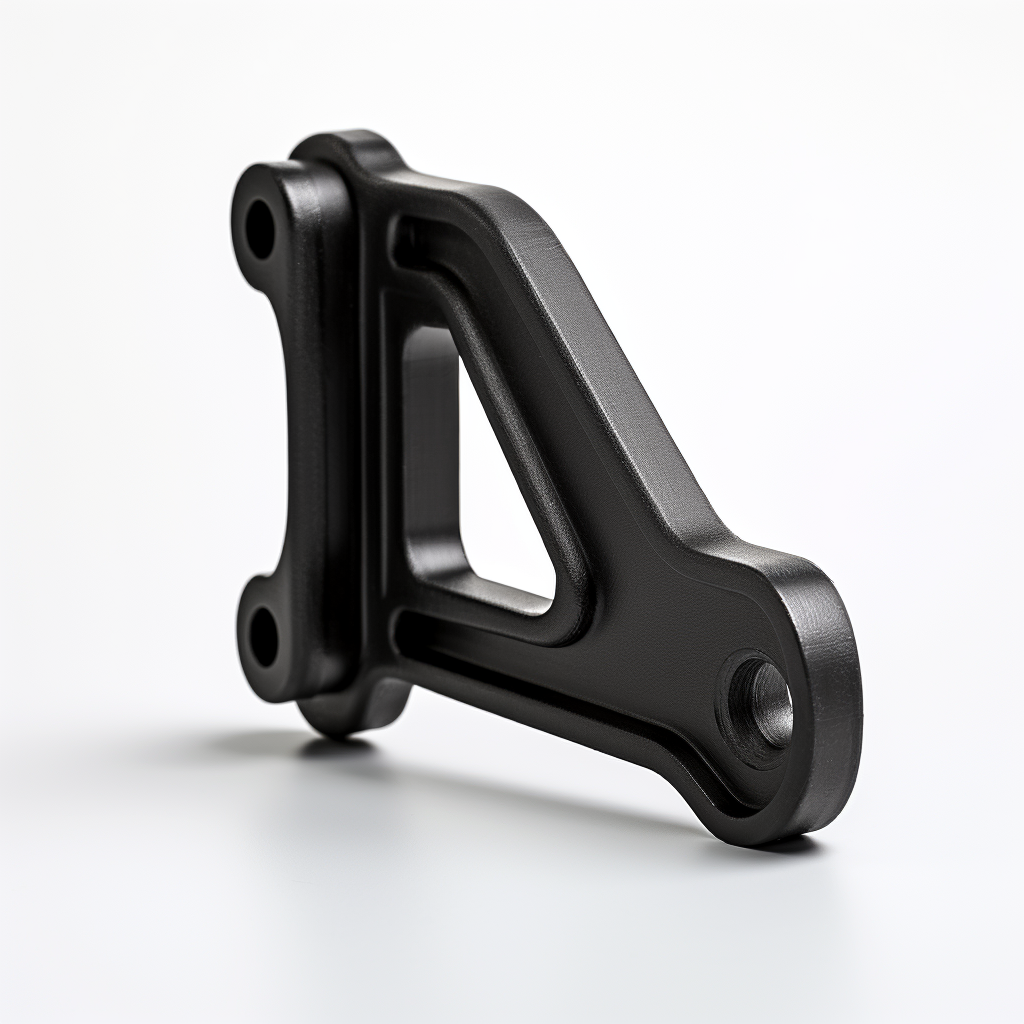
Get A Quote Now!
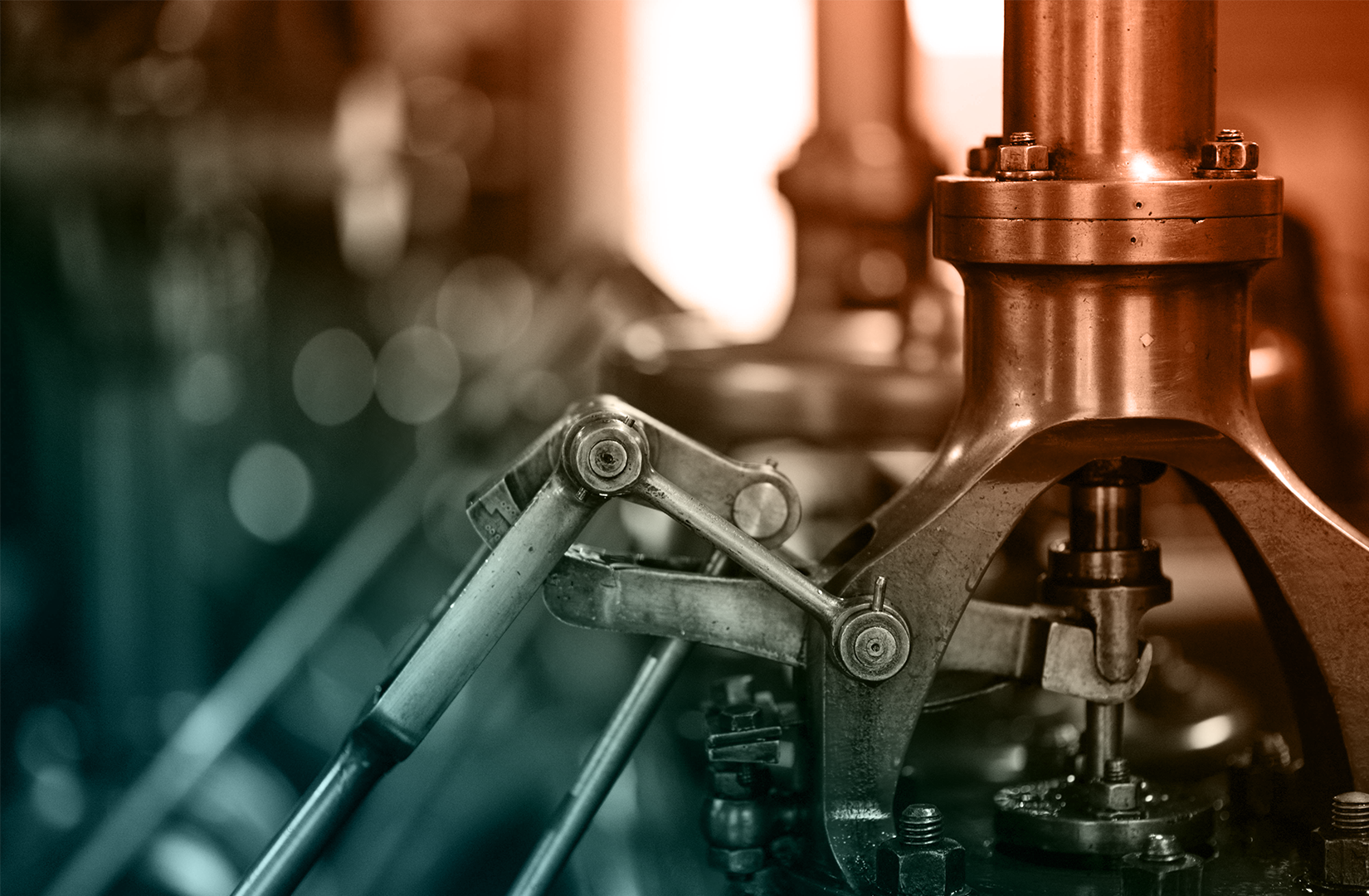
Groove Design References
Learn More
Coatings, Packaging, & Other Services
Learn More
Custom Parts & Custom O-rings
Learn More