Custom Parts - Plastics, Rubbers, and Metals
Updated: Jul 19, 2024
Whether you require parts to be manufactured from Plastics, Rubbers, or Metals, Canyon Components has you covered! In this blog post, we dig into some of the manufacturing processes available for each material type.
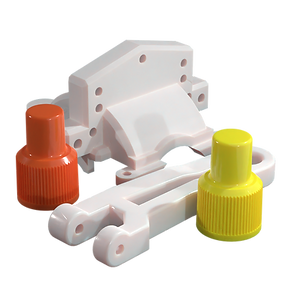
At Canyon Components, we recognize the value of expertly crafted, quickly produced custom parts. That's why we make sure to offer our customers any manufacturing technique they desire. You can trust Canyon Components to produce your custom parts to the highest standard, whether they are made of rubber, plastic, or metal.
We also offer rapid prototyping services and materials of virtually every specification requirement.
Canyon Components strives to meet all customer service requests. Feel free to contact a Canyon Components product and application consultant and let our knowledgeable staff help you design the perfect part for your needs.
With manufacturing capabilities focused in rubbers, plastics, and metals, Canyon Components can make even the most complex parts a reality.
Custom Rubber Parts
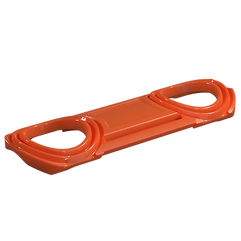
Custom rubber parts can be manufactured in a variety of ways depending on the customers requirements and intended use. Often times, rubber parts can be split into the following manufacturing categories: Compression Molding, Transfer Molding, Injection Molding, and Extrusion.
Compression Molding: Compression molding is an extremely common rubber molding process in which oversized, uncured rubber preforms are placed into a heated compression mold. These preforms are specifically designed to meet the fill requirements of the mold as well as the tolerance requirements of the final part. The heated mold then compresses the preform. Once the material within the mold is cured via the programmed logic of the molding machine, the mold can be opened and the part is removed. The part then undergoes a de-flashing process and is ready for final inspection and packaging. Compression molding is popular because it is low cost and the molds are easy to produce, but it does not allow for tolerances that are as tight as injection molding tolerancing.
Transfer Molding: Transfer molding is sometimes considered to be the midpoint between compression molding and injection molding. Like compression molding, a large uncured preform is created and will be used as the material source for production. The preform is placed in a section of the molding machine that compresses the material until it is forced through small holes and fills the mold cavities. The material is then allowed to cure and the final part is removed from the machine. Transfer molding is preferred because it allows for high cavity counts and short production cycles. Unfortunately, transfer molding is more expensive than compression molding due to mold complexity. Also, transfer molding tends to produce large amounts of waste material which contributes to the cost of the final part.
Injection Molding: Injection molding rubber is functionally similar to injection molding plastics. Uncured elastomeric material is loaded into an extruder and injected into the mod via a runner and gating system. The material is cured within the mold and can then be removed. Injection molding produces high quality parts with rapid cycle times. Also, no preforms need to be created which further decreases cycle times. Unfortunately, injection molding molds can be more expensive to produce and there are limitations to what elastomeric materials can be used.
Extrusion: When an application requires one long cord of material that uses the same cross sectional profile across its length, extrusion is often used. First, a die is manufactured that matches the specific cross sectional geometry required by the final part. The die can then be attached to the end of an extruder that is filled with uncured material. The material is then pushed through the die and is cured in line as more geometry is created behind it. Extrusion is commonly used for sheets, O-ring cord, and tubing.
Custom Plastic Parts
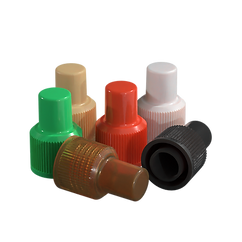
Canyon Components can also produce any plastic part that you may require. From polypropylene to polycarbonate to PEEK, every material and geometry is possible! The most common manufacturing techniques available for custom plastic parts are Injection Molding, Thermoforming, and Machining.
Injection Molding: Injection molding plastics is functionally similar to injection molding rubber. Uncured plastic material is loaded into an extruder and injected into the mod via a runner and gating system. The material is cured within the mold and can then be removed. Injection molding produces high quality parts with rapid cycle times. The primary difference from rubber injection molding is that plastic injection molded parts and molds must be designed with more care to ensure that the final part can be properly removed from the mold once curing is complete. This is because most plastics are rigged enough that they can be bent and fracture if a mold is designed improperly. Additional variables to keep in mind include knit lines, ejection pin location, and warping.
Thermoforming: Thermoforming is a process by which a thin sheet of plastic is heated and vacuumed (or compressed) to the surface of a mold, causing the thin sheet of plastic to take on the shape of the mold. The parts can then be put through CNC post processing to refine the parts and add any additional geometric features. Thermoforming is relatively low cost and can create light components at high volume.
Machining: With CNC Machining, custom plastic parts can be produced rapidly with none of the startup costs associated with molds. While this production method is not as fast as molding, CNC machining can still be a valid way to produce medium quantities of complex parts for production purposes.
Component Assemblies

Another commonly requested service is custom component assemblies. Many customers require assemblies made from multiple components, and Canyon Components can support this need! It's very common for assemblies to have multiple parts composed of different material types, and every assembly requires something different.
Please consult a Canyon Components Engineer about your specific application and we will use our decades of experience to formulate an assembly solution that fits your need!
Specialty Materials

Canyon Components proudly serves all industries. Whether you operate in the medical, food & drug, semiconductor, aerospace, military, or automotive industries, Canyon Components will have materials that meet your needs. Some examples of specialty materials are listed below.
USP VI {87} & {88}: Material that has undergone the USP Class VI testing systemic injection test, intracutaneous test, and implantation test. These tests prove that the material in question is biologically unreactive up to levels determined by the standard. USP Class VI materials are frequently used in medical grade products and mechanisms.
FDA CFR 21.177.2600: This certification is a list of elastomers, curing agents, vulcanizing materials, and other fillers that are permitted by the FDA. Depending on the level of compliance, FDA compliant materials are recognized as safe for use in applications contacting different types of food products. FDA compliant materials are frequently used in food grade products and mechanisms.
AED Norsok-M710 & AED NACE-TM0297: These Norsok and NACE standards both test to prove a materials capability in applications where rapid gas decompression (aka. explosive decompression) is possible. Materials that pass NACE and Norsok tests are commonly used in ultra high pressure environments where CO2 is present.
NSF 51 & NSF 61: NSF 51 establishes a minimum public health and sanitation requirement for a material. NSF 51 compliant materials are commonly used in food grade products and mechanisms. NSF 61 establishes minimum health effect requirements for chemical contents and impurities that are imparted to drinking water. NSF 61 compliant materials are commonly used in applications where the part may come in contact with drinking water.
There are many other specifications that components can be manufactured to, including 3A, MIL-spec, and AS9100. We also offer optional clean room manufacturing, specialty coatings, custom packaging. Please see our Services Page if you are interested in learning more.
Prototyping
Often times, it is extremely useful to receive low volume prototype parts for preliminary testing. If you find yourself in a situation like this, Canyon Components has you covered. With rapid prototyping methods like 3D printing, CNC machining, and single cavity test molds, it is possible to produce low volume, ultra high quality parts for your testing needs.
Canyon Components engineers are also available to assist in part design and in consultation.

3D Printing: With SLA and FDM 3D printing, custom prototype parts can be rapidly manufactured for testing purposes from numerous plastics, rubbers, metals, and ceramics.
CNC Machining: With CNC Machining, custom metal and plastic parts can be produced rapidly. While this is not as fast as molding, CNC machining can still be a valid way to produce medium quantities for production purposes.
Single Cavity Molds: Sometimes a large mold with hundreds of cavities is unnecessary due to small volume production quantities for test purposes. Single cavity molds can be produced for these purposes. It saves costs in the short term and more cavities can always be added once the design is proven.
Please consult a Canyon Components Engineer about your specific application and we will use our decades of experience to formulate a solution that fits your need!
Sources:
[1] Root. (2023, August 10). Step-by-Step process: How to make plastic parts efficiently. FOW Mould. https://www.immould.com/how-to-make-plastic-parts-efficiently/