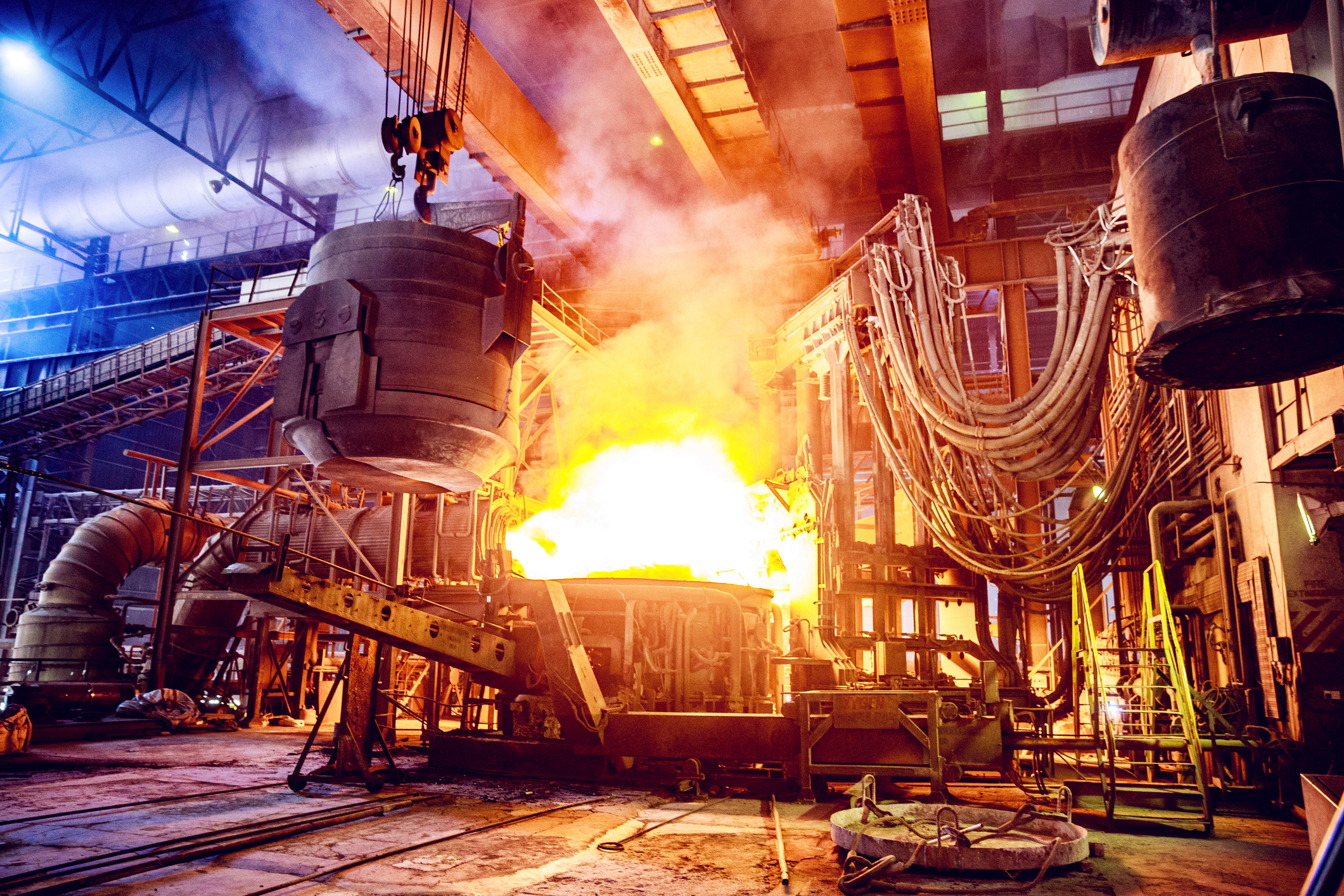
Silicone (VMQ, PVMQ) Selection Guide
The term "silicone" covers a large group of materials, O-rings, gaskets, & custom molded parts in which vinyl-methyl-silicone(VMQ) is often the central ingredient. These compounds can be synthesized with a wide variety of compositions and properties. Silicone seals, O-rings, gaskets, & custom molded parts do not demonstrate the greatest tensile strength or wear resistance, but remain relatively unchanged over a very large temperature range. For these reasons, silicone seals, O-rings, gaskets, & custom molded parts are excellent for extreme temperatures in static applications. However, the low strength and wear resistance of silicone O-rings, gaskets, & custom molded parts causes the seal to fail in many dynamic applications.
Canyon Components carries a range of silicone O-rings, gaskets, & custom molded parts, and we are happy to custom tailor a seal to meet your application requirements! In addition to standard compression molding, silicone can also be injection molded in it's LSR (liquid silicone rubber) form. Silicone seals, O-rings, gaskets, & custom molded parts are popular in applications where extreme temperature fluctuations are common, such as the automotive and aerospace industries. Additionally, many silicone compounds, O-rings, gaskets, & custom molded parts are physiologically neutral making them ideal for the medical and food industries.
Common names include: VQM (Silicone), PVMQ Trade Name: Silastic®, Elastosil®, Thermoflex®, Wacker, DOW Corning, DOWSIL.
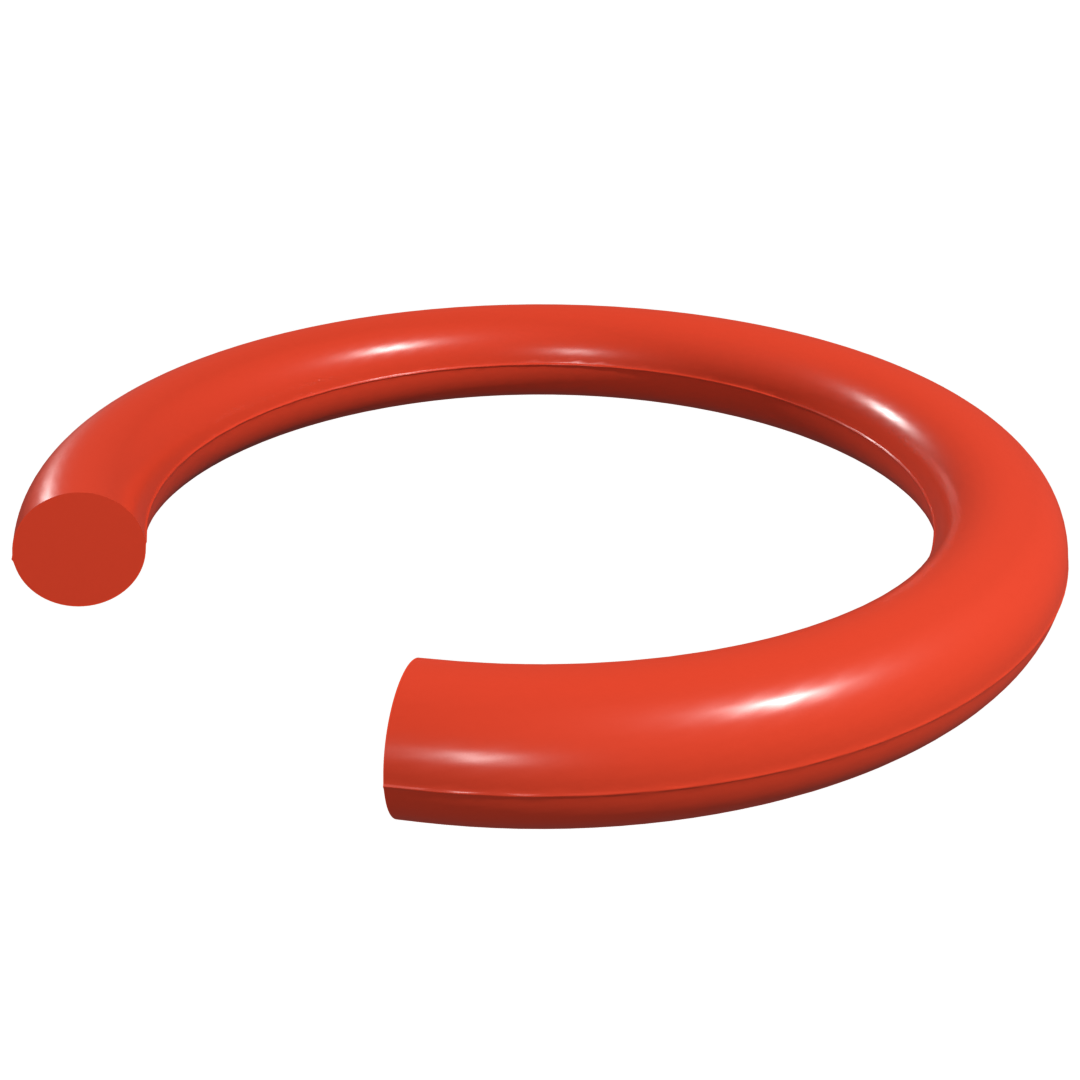
Features of Silicone
- Silicone O-rings, gaskets, & custom molded parts can be compounded to meet FDA, USP Class VI, USDA, 3-A and Canada AG. Learn more about Platinum Cured Silicone.
- Silicone O-rings, gaskets, & custom molded parts have excellent heat and compression resistance, excellent flexibility, good electrical insulator
- Silicone O-rings, gaskets, & custom molded parts have excellent resistance to oxygen, ozone and sunlight
- Silicone O-rings, gaskets, & custom molded parts have excellent resistance to animal and vegetable oil and grease
- Silicone O-rings, gaskets, & custom molded parts are physiologically neutral and good resistance to fungal and biological attack
- Silicone O-rings, gaskets, & custom molded parts are available in multiple compounds to meet performance and cost requirements
Limitations of Silicone
- Silicone O-rings, gaskets, & custom molded parts are not recommended for dynamic applications since it has low strength, poor abrasion resistance and high gas permeability
- Silicone O-rings, gaskets, & custom molded parts have poor resistance to concentrated solvents, oils, concentrated acids, diluted sodium hydroxide, hydrocarbon based fuels, and aromatic mineral oil
- Silicone O-rings, gaskets, & custom molded parts have poor resistance to aromatic Hydrocarbons (benzene, toluene), aromatic mineral oil, acids and alkalis
- Silicone O-rings, gaskets, & custom molded parts have poor resistance to superheated water or steam over 250°F
- Silicone O-rings, gaskets, & custom molded parts have a Service Temperature Range of (varies with application): -90°F to 500°F (-68°C to 260°C). Depending on compound and application. Learn more about Low Temperature PVMQ Silicone and High Temperature Silicone.
Please consult a Canyon Components Engineer about your specific application and we will use our decades of experience to formulate a solution that fits your need.
Silicone Materials Available
This table shows many of our standard materials and links out to our O-ring store. Get in touch with us if you need a custom gasket, custom molded part, or non-standard geometry!
Filter by
Temperature Search (°C)
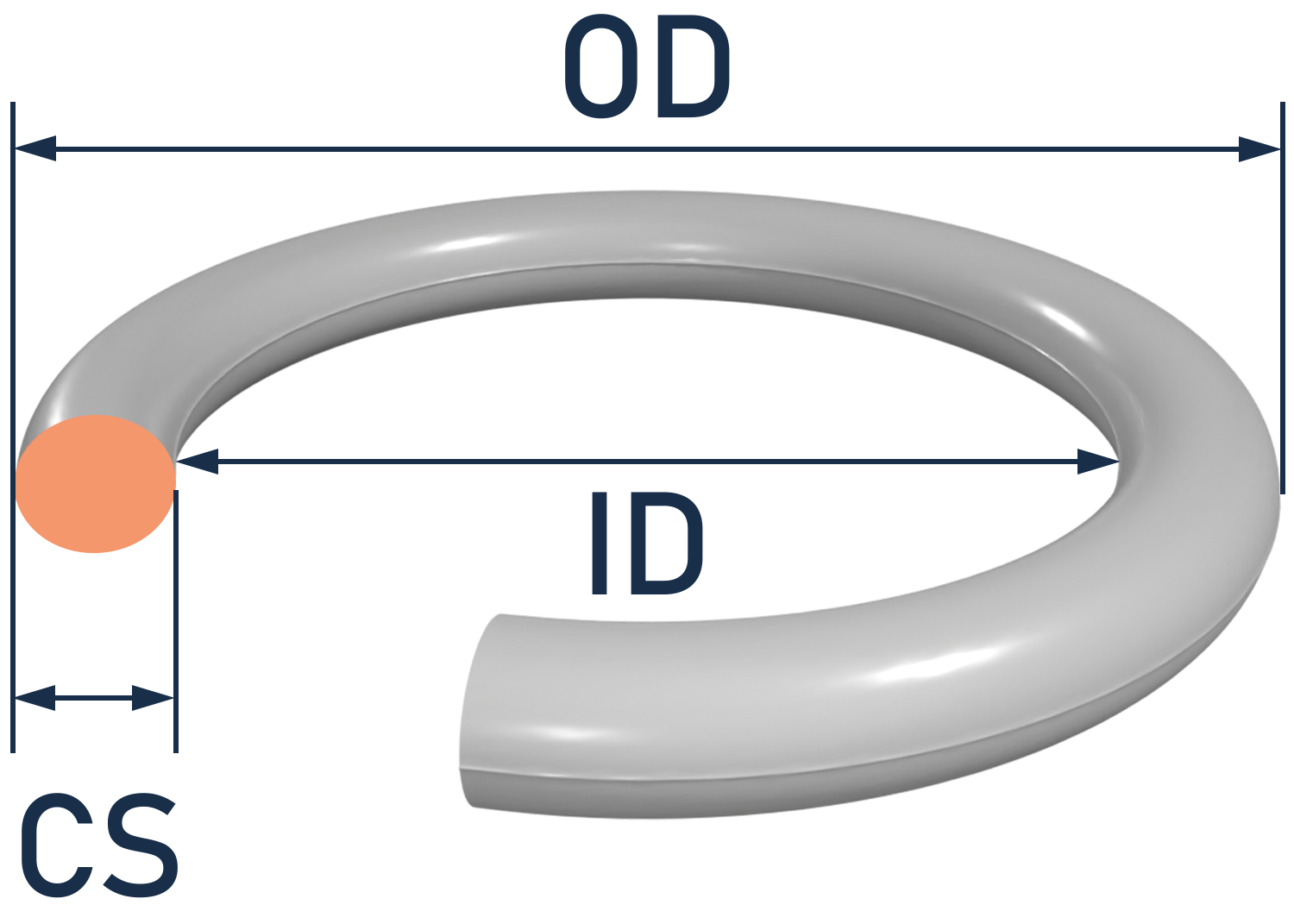
Back to Elastomers Hub
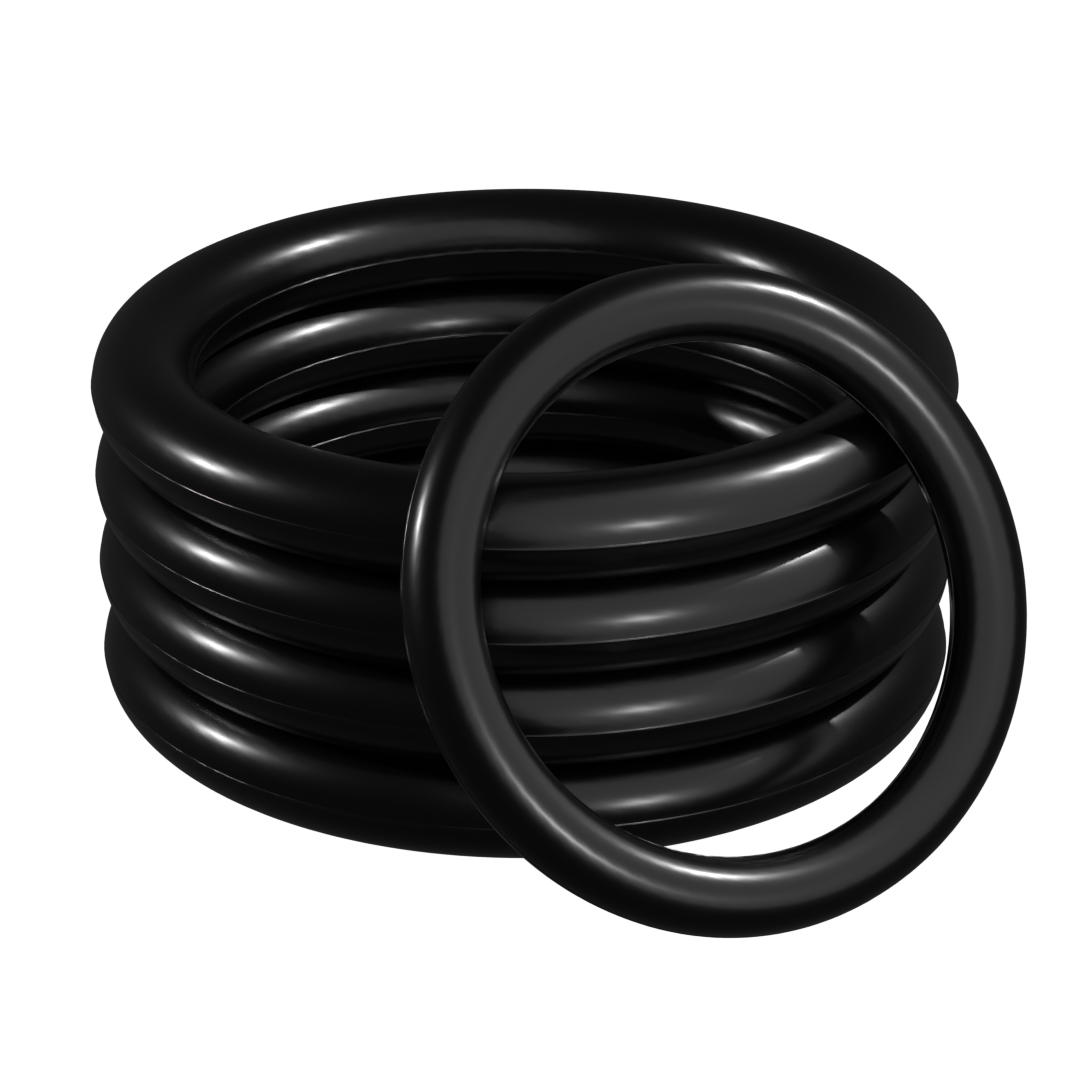
Get A Quote Now!
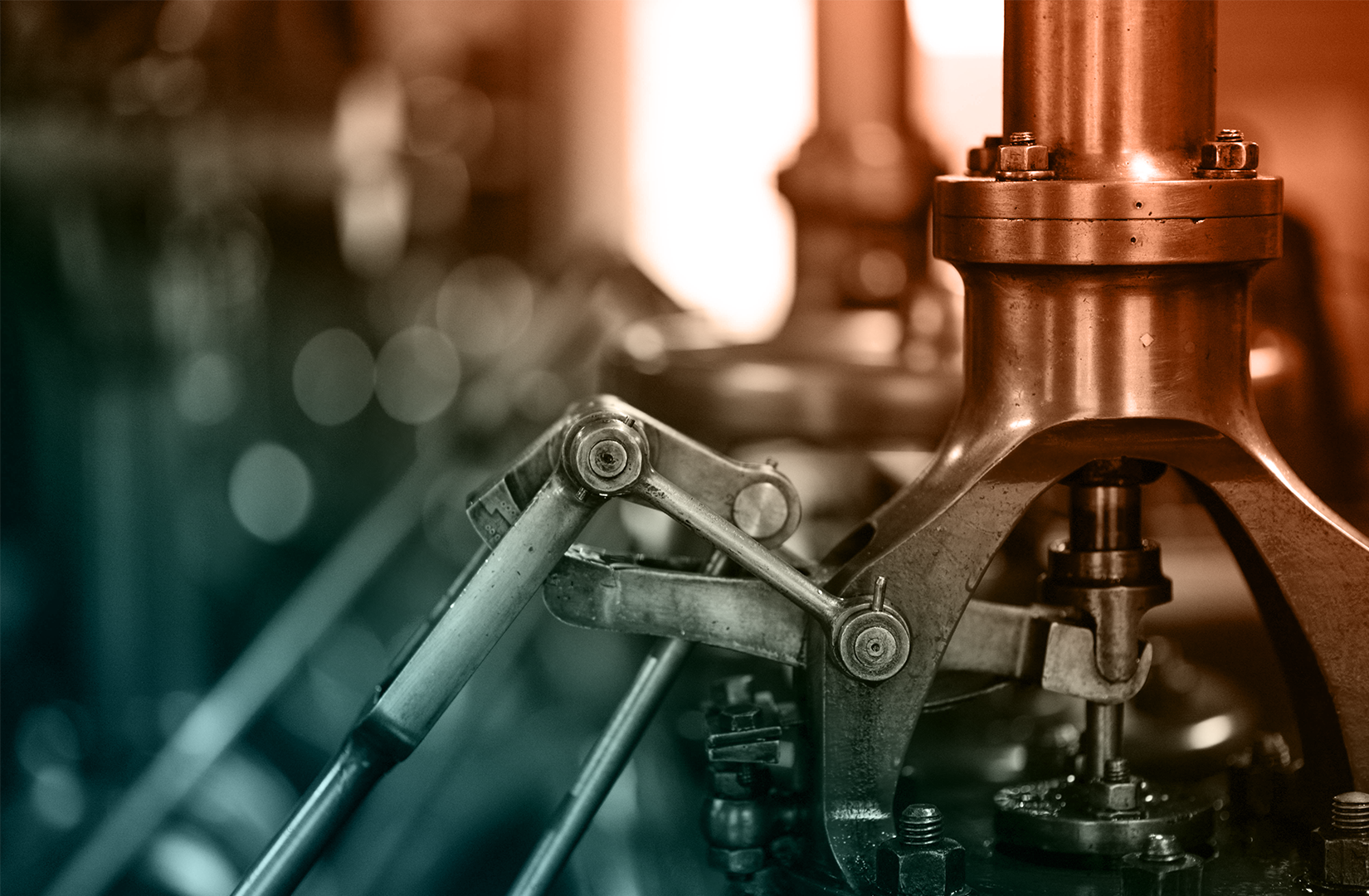
Groove Design References
Learn More
Coatings, Packaging, & Other Services
Learn More
Custom Parts & Custom O-rings
Learn More
Are Fluorosilicone O-rings the same as silicone O-rings?
No, Fluorosilicone O-rings (FSO-rings) are not the same as Silicone O-rings (Silicone O-rings). Silicone and fluorosilicone O-rings are both elastomeric sealing materials, but they have different chemical compositions and properties that make them suitable for different applications. Here's a comparison of their key characteristics:
Silicone O-Rings:
1. Composition: Silicone O-rings are made from silicone rubber, which is a polymer composed of silicon, oxygen, carbon, and hydrogen atoms. The unique chemical structure of silicone gives it its characteristic flexibility and heat resistance.
2. Temperature Range: Silicone O-rings have a broad temperature range and can withstand temperatures from approximately -100°F to 600°F (-75°C to 315°C) depending on the blend. They are excellent for high-temperature applications.
3. Chemical Resistance: Silicone has good resistance to water, steam, and many chemicals. However, it is not recommended for use with petroleum-based products, fuels, and certain solvents.
4. Elasticity: Silicone O-rings are known for their flexibility and elasticity, making them suitable for dynamic sealing applications.
5. Electrical Insulation: Silicone is an excellent electrical insulator and is used in electrical and electronic applications.
Fluorosilicone O-Rings:
1. Composition: Fluorosilicone O-rings are made from fluorosilicone rubber, which is a modified form of silicone rubber. It contains fluorine atoms in addition to silicon, oxygen, carbon, and hydrogen atoms. This modification enhances its resistance to oils and fuels.
2. Temperature Range: Fluorosilicone O-rings have a temperature range similar to standard silicone, typically from -100°F to 356°F (-75°C to 180°C). While they can withstand high temperatures, they are not as heat-resistant as some other elastomers.
3. Chemical Resistance: Fluorosilicone offers improved resistance to petroleum-based products, including oils, fuels, and solvents, compared to standard silicone. It is particularly suitable for applications where exposure to these substances is a concern.
4. Elasticity: Fluorosilicone maintains the flexibility and elasticity characteristic of silicone rubber, making it suitable for dynamic sealing applications.
5. Fuel and Oil Resistance: The primary advantage of fluorosilicone over standard silicone is its enhanced resistance to oils and fuels, which is valuable in automotive and aerospace applications.
Summary:
- Silicone O-rings: Suitable for high-temperature applications and where exposure to water and steam is a concern. Not recommended for use with petroleum-based products.
- Fluorosilicone O-rings: Ideal for applications requiring resistance to oils, fuels, and solvents, while still maintaining flexibility. They have a broader range of chemical resistance compared to standard silicone.
The choice between silicone and fluorosilicone O-rings should be based on the specific requirements of the application, particularly in terms of temperature, exposure to oils or fuels, and chemical compatibility.
Are silicone O-rings better than rubber?
Silicone and rubber O-rings (like EPDM, Viton, and NBR) each have unique properties, making them suitable for different applications. The choice between them depends on the specific requirements of your use case. Here are some key differences:
1. Temperature Resistance: Silicone O-rings generally have a wider temperature range compared to other rubber materials. They can operate effectively in more extreme temperatures, both hot and cold.
2. Chemical Resistance: Rubber O-rings, particularly those made from nitrile or other specialized compounds, often have better resistance to certain oils and fuels compared to silicone. However, silicone is generally more resistant to weathering, ozone, and UV radiation.
3. Durability: Other rubber materials are typically more durable and have better tear resistance than silicone. They're suited for applications involving high pressure or where mechanical wear is a concern.
4. Flexibility and Seal Quality: Silicone maintains its flexibility over a wider range of temperatures, which can be crucial in certain sealing applications. However, for dynamic applications where the O-ring is in constant motion, other rubber materials might provide better performance.
5. Cost and Availability: Other rubber materials are usually more cost-effective and widely available in a variety of sizes and specifications.
6. Food Safety and Medical Applications: Silicone is often preferred for food-grade and medical applications due to its inertness and ability to be sterilized.
In summary, if your application involves extreme temperatures, exposure to UV light, or requires FDA compliance for food or medical use, silicone O-rings might be the better choice. However, for general industrial applications, especially where oil and fuel resistance, durability, and cost are concerns, O-rings made from other rubber materials might be more suitable.
Are there different types of O-rings?
Yes, there are different types of O-rings, and they can vary in terms of materials, sizes, shapes, and specific properties to suit various applications. Here are some common types of O-rings:
1. Material Types:
- Nitrile Rubber (NBR): Known for its excellent resistance to oils and fuels.
- Viton (FKM): Offers superior chemical resistance, especially to harsh chemicals and high-temperature environments.
- EPDM: Resistant to weathering, ozone, and UV rays, making it suitable for outdoor applications.
- Silicone: Known for its flexibility and ability to withstand extreme temperatures.
- Polyurethane: Offers excellent wear resistance and is used in high-pressure hydraulic systems.
- Neoprene: Balances chemical stability with flexibility and is often used in refrigeration and air conditioning.
2. Size and Shape:
- O-rings come in various sizes and shapes, from standard circular O-rings to square, rectangular, and custom shapes to fit specific sealing needs.
3. Temperature and Pressure Ratings:
- O-rings are designed to handle specific temperature and pressure ranges. High-performance O-rings are available for extreme conditions.
4. FDA-Compliant O-rings:
- These O-rings are made from materials approved by the U.S. Food and Drug Administration (FDA) and are safe for use in food and pharmaceutical applications.
5. Chemical-Resistant O-rings:
- Some O-rings are specially formulated to resist specific chemicals or environments, such as O-rings designed for use with aggressive acids or solvents.
6. Metric and Imperial Sizes:
- O-rings are available in both metric and imperial (inch) sizes to accommodate various international standards and requirements.
7. Static and Dynamic Seals:
- O-rings can be used in static sealing applications (where there is no movement between sealing surfaces) or dynamic sealing applications (where there is relative motion between sealing surfaces).
8. High-Purity O-rings:
- These O-rings are used in applications requiring high-purity materials, such as semiconductor manufacturing.
9. Custom O-rings:
- Manufacturers can produce custom O-rings to meet specific size, material, and performance requirements.
10. Hygienic O-rings:
- These O-rings are designed for sanitary applications in industries like food, pharmaceuticals, and biotechnology.
The choice of O-ring type depends on the specific requirements of the sealing application, including factors such as temperature, pressure, chemical exposure, and the environment in which the O-ring will be used. Selecting the right type of O-ring is essential to ensure a reliable and effective seal.
Are Viton O-rings better than regular O-rings?
Viton O-rings and regular O-rings (typically made of materials like Nitrile, Silicone, or EPDM) have different properties and are better suited for different applications. The choice between them depends on the specific needs of your application. Here are some factors to consider:
1. Chemical Resistance: Viton O-rings have excellent resistance to a wide range of chemicals, including oils, fuels, lubricants, and most mineral acids. They perform better than regular O-rings in harsh chemical environments.
2. Temperature Resistance: Viton withstands high temperatures better than most common O-ring materials. It can be used in environments where temperatures clumb up to 437°F, making it suitable for high-temperature applications.
3. Durability and Longevity: Viton has excellent resistance to aging, weathering, ozone, oxygen, and sunlight. This makes Viton O-rings more durable and long-lasting in harsh environments compared to some regular O-rings.
4. Cost: Viton O-rings are generally more expensive than regular O-rings made from materials like Nitrile or Silicone. This is due to their superior performance characteristics.
5. Application Specific: The choice should be based on the specific requirements of the application, such as exposure to chemicals, temperature ranges, and mechanical wear and tear.
In summary, Viton O-rings are superior in terms of chemical and temperature resistance, durability, and longevity, but they are also more expensive. Regular O-rings may be sufficient for less demanding applications and are more cost-effective. Always consider the specific conditions of your application when choosing an O-ring material.
Can I use silicone instead of an O-ring?
Using silicone as a direct substitute for an O-ring depends on the specific application and the conditions under which the seal is required to function. Here are some considerations:
1. Sealing Requirements: O-rings are designed to create a very effective seal between two parts, especially in dynamic applications where parts may move or vibrate. Silicone in the form of a caulk or sealant may not provide the same level of sealing efficiency, especially under pressure.
2. Physical Properties: O-rings are made from materials that can withstand a range of pressures and temperatures while maintaining their shape and flexibility. Silicone sealants or sheets may not have the same level of durability or resilience under similar conditions.
3. Chemical Compatibility: While silicone has good chemical resistance, the specific formulation of an O-ring might be chosen for its resistance to particular chemicals. Replacing it with a different silicone material could lead to reduced chemical resistance.
4. Application Design: Many systems are specifically designed to use O-rings. Using a different material like silicone sealant could lead to improper fit or function, potentially causing leaks or mechanical failures.
5. Ease of Replacement and Maintenance: O-rings are generally easier to replace and maintain compared to silicone sealants, which may require removal and reapplication.
If you're considering using silicone as a substitute for an O-ring, it's important to carefully evaluate these factors. In some low-stress, low-pressure, and non-critical applications, silicone sealants might work as a temporary fix. However, for most industrial or mechanical applications, it's advisable to use the appropriate O-ring designed for the specific purpose. If in doubt, consulting with a mechanical engineer or the equipment manufacturer is recommended.
Can you use Vaseline on silicone O-rings?
Using Vaseline (petroleum jelly) on silicone O-rings is generally not recommended for long-term applications or critical sealing situations. While Vaseline is a common lubricant and can provide short-term lubrication for silicone O-rings, there are some important considerations:
1. Compatibility: Silicone rubber is known for its resistance to a wide range of chemicals, including petroleum-based products like Vaseline. However, over extended periods, the Vaseline can potentially cause the silicone material to swell or deteriorate. This is particularly important in applications where the integrity of the seal is critical.
2. Temperature: Vaseline has a limited temperature range for effective lubrication. It may not perform well at extreme temperatures, especially high temperatures, where it can break down or become less effective.
3. Migration: Vaseline can migrate over time, potentially contaminating the surrounding environment or interfering with other materials and components in the system.
4. Longevity: Vaseline is not a long-lasting lubricant. It may need to be reapplied frequently to maintain its lubricating properties.
For critical sealing applications or situations where the integrity of the seal is essential, it's advisable to use a lubricant that is specifically designed for O-ring applications and is compatible with silicone rubber. If you notice any issues, it's advisable to switch to a more suitable lubricant to protect the O-rings and maintain the integrity of the seal. Please get in tougch with a Canyon Components engineer if you have any questions.
How do I choose an O-ring?
Choosing the right O-ring for your application is crucial to ensure a reliable seal. Here are the steps to help you choose the appropriate O-ring:
1. Identify the Application Requirements:
- Determine the operating conditions, including temperature, pressure, and exposure to chemicals.
- Consider whether the application is static (stationary) or dynamic (moving).
- Identify any specific industry or regulatory standards that must be met, such as FDA compliance for food-grade applications.
2. Material Selection:
- Select an O-ring material that is compatible with the operating conditions. Common materials include Nitrile (Buna-N), Viton, EPDM, Silicone, FFKM Perfluoroelastomers, and others.
- Consider the material's resistance to chemicals, temperature range, and compatibility with the fluids or gases involved.
3. Size and Dimensions:
- Measure the groove dimensions where the O-ring will be placed accurately.
- Determine the required O-ring size, including inner diameter (ID), outer diameter (OD), and cross-section (thickness).
- Ensure that the selected O-ring size will function properly when paired with the groove dimensions.
4. Temperature and Pressure Ratings:
- Check the temperature and pressure ratings of the selected O-ring material. Ensure that it can withstand the expected conditions without degradation or failure.
5. Chemical Compatibility:
- Verify that the O-ring material is compatible with the substances it will come into contact with, such as oils, fuels, chemicals, or gases.
- Consult chemical compatibility charts or databases to ensure the material's resistance to specific chemicals.
6. Hardness and Durometer:
- Consider the hardness or durometer of the O-ring material. Softer materials may be more flexible but less durable, while harder materials may be more durable but less flexible.
7. Installation and Maintenance:
- Follow proper installation procedures to ensure a secure and effective seal.
- Establish a maintenance schedule to inspect and replace O-rings regularly, as they can wear out over time.
8. Consult with Experts:
- If you have uncertainties or unique requirements, consult with Canyon Components O-ring experts who can provide guidance and recommend the best O-ring solution for your application.
Remember that choosing the right O-ring is essential for preventing leaks, maintaining equipment integrity, and ensuring safety in various industrial and mechanical systems. Taking the time to carefully assess your application's needs and selecting the appropriate O-ring material and design will contribute to the success and reliability of your sealing solution.
Is platinum cured silicone better than silicone?
The difference between regular silicone and platinum silicone primarily lies in their respective curing processes and the resulting properties:
1. Curing Process:
- Regular Silicone: This type of silicone is typically cured using a process that involves peroxides. Peroxide curing is an older method and is less expensive. However, it can leave behind byproducts in the silicone material, which may not be suitable for certain applications, particularly where purity is essential.
- Platinum Silicone: Platinum-cured silicone uses a platinum catalyst for curing. This process is more advanced and results in a purer product, as it doesn't leave behind any byproducts. This feature makes platinum silicone particularly valuable in medical, food, and skin-contact applications.
2. Physical Properties:
- Regular Silicone: Though it varies based on formulation, regular silicone might have slightly different physical properties compared to its platinum counterpart. For example, it might have slightly different elasticity or tensile strength.
- Platinum Silicone: Platinum silicone generally has superior physical properties, including better thermal stability, increased tensile strength, and enhanced durability. It's also often more transparent and has better biocompatibility.
3. Biocompatibility and Safety:
- Regular Silicone: The byproducts left from peroxide curing can lead to issues in applications where purity is critical. For example, it might not be suitable for long-term medical implants or in food-grade applications.
- Platinum Silicone: Due to its purity and lack of byproducts, platinum silicone is often preferred in medical applications, food-grade products, and baby products. It's considered safer and more inert in these contexts.
4. Cost:
- Regular silicone is generally less expensive than platinum silicone, making it a more cost-effective choice for applications where the superior properties of platinum silicone are not necessary.
In summary, while both regular and platinum silicone have similar basic chemical compositions, platinum silicone's curing process results in a purer, more stable product with better physical properties and higher biocompatibility. This makes it more suitable for high-end, sensitive applications, especially in the medical, food, and baby product industries. Regular silicone, being more cost-effective, is still widely used in a variety of industrial and consumer applications where the specific advantages of platinum silicone are not required.
What are cheap O-rings made of?
Cheap O-rings are typically made from less expensive elastomer materials compared to premium or specialized O-rings like Viton, specialty Silicone blends, Aflas, or FFKM. The choice of material depends on the cost-effectiveness required for the application. Here are some common inexpensive elastomers used for cheap O-rings:
1. Nitrile Rubber (NBR): Nitrile rubber, also known as Buna-N, is one of the most cost-effective elastomers. It offers good resistance to oils, fuels, and lubricants, making it a popular choice for many industrial applications. While it may not have the same level of performance as more expensive materials, it is suitable for many standard sealing applications.
2. EPDM (Ethylene Propylene Diene Monomer): EPDM is known for its excellent weather resistance and is often used in outdoor applications. It's more cost-effective than premium elastomers like Viton and Silicone and is suitable for sealing applications that don't require high-temperature or chemical resistance.
3. SBR (Styrene Butadiene Rubber): SBR is an economical elastomer often used in low-cost O-rings. It has good abrasion resistance but may not offer the same level of chemical resistance as Nitrile or EPDM.
4. Natural Rubber (NR): Natural rubber is another low-cost elastomer option. It offers good elasticity and low-temperature flexibility but may not perform well in environments with oils or certain chemicals.
5. Neoprene (CR): Neoprene is a moderately priced elastomer known for its resistance to weathering, ozone, and UV radiation. It's often used in outdoor applications where cost is a consideration.
While these materials are cost-effective, it's important to note that they have limitations compared to more expensive elastomers like Viton, specialty Silicone blends, Aflas, and FFKM. They may not perform well in extreme temperature or chemical environments. When choosing O-rings, it's essential to consider the specific requirements of your application and select the material that balances performance and cost-effectiveness to meet those needs.
What are yellow O-rings used for?
Yellow O-rings are typically used as a visual indicator to distinguish them from O-rings made of other materials or colors. The color coding helps in identifying the specific material or application of the O-ring without the need for detailed inspection or testing. Here are a few common uses of yellow O-rings:
1. Food-Grade Applications: Yellow O-rings are sometimes used in food processing and pharmaceutical industries where hygiene and compliance with food safety regulations are critical. The yellow color may indicate that the O-ring is made of a food-grade material, such as FDA-compliant elastomers.
2. Chemical Compatibility: In some cases, yellow O-rings may be used in applications where they are exposed to specific chemicals or aggressive environments. The color can indicate that the O-ring is made of a material with enhanced chemical resistance or compatibility for that particular application.
3. High-Temperature Applications: Yellow O-rings may be used in high-temperature applications where the material is specially formulated to withstand elevated temperatures. The color coding helps in quickly identifying the O-rings suitable for high-temperature sealing.
4. Material Differentiation: Yellow can be used as a general color code to differentiate O-rings made of certain materials from others. For example, it may signify a specific type of elastomer or a proprietary material formulation used by a particular manufacturer.
5. Specialized Applications: In some cases, yellow O-rings may be used in specialized applications where they need to stand out or be easily identifiable due to specific performance characteristics, such as resistance to abrasion or extreme conditions.
It's important to note that the specific meaning of a yellow O-ring may vary between manufacturers or industries. Therefore, when using color-coded O-rings, it's essential to refer to the manufacturer's documentation or industry standards to ensure that the O-ring is being used appropriately for the intended application. Additionally, always follow safety and material compatibility guidelines when selecting O-rings for specific purposes.
What do different colored O-rings mean?
The color of an O-ring doesn't inherently signify a specific characteristic or quality; rather, it's often used as a means to identify different materials or specifications. Here's a general guide to what different colored O-rings might indicate:
1. Black: The most common color for O-rings, typically made of nitrile (Buna-N), neoprene, EPDM, or other general-purpose materials. These are widely used in various applications due to their good resistance to oils, fuels, and certain chemicals. However, it should be noted that virtually any elastomeric material can be, and will frequently be manufactured in black colorations. This includes specialty materials like Aflas, FFKM Perfluoroelastomers, and silicone.
2. Blue: Fluorosilicone O-rings are typically manufactured in blue colorations. Also, blue is often associated with FDA-approved materials that are safe for food, water, and beverage contact. Blue O-rings are also easily detectable, which helps in maintaining safety standards in food processing industries.
3. Green: Commonly indicates the presence of hydrogenated nitrile (HNBR), which offers better heat and chemical resistance compared to standard nitrile. Viton® (fluorocarbon rubber) can also frequently be found in green colorations.
4. Brown: Typically signifies the use of Viton® (fluorocarbon rubber), known for its excellent resistance to high temperatures and chemicals, including petroleum products.
5. Red, Orange, or Pink: Frequently used for silicone O-rings, which are known for their heat resistance and use in food-grade applications.
6. White or Clear: Often indicates that the O-ring is made from silicone, Teflon (PTFE), or another material that is suitable for sanitary or medical applications.
7. Yellow: May indicate special compounds, such as polyurethane, which are known for their wear resistance and strength.
8. Metal Detectable O-rings: These O-rings are infused with metal detectable materials and are often blue. They are used in the food and pharmaceutical industries where contamination by foreign objects is a critical concern.
It's important to note that these color associations are not universal and can vary between manufacturers. The color alone should not be relied upon to determine the material or suitability of an O-ring for a specific application. Always refer to the manufacturer's specifications or consult with a Canyon Components engineer when selecting an O-ring for a particular use.
What is a platinum cured silicone O-ring?
A platinum-cured silicone O-ring is a type of sealing ring made from silicone rubber that has been manufactured using a platinum-based curing process. This curing method is often referred to as "platinum cure" and is distinct from the more common peroxide-cured silicone rubber.
Here are some key characteristics and advantages of platinum-cured silicone O-rings:
1. Purity: Platinum-cured silicone rubber is known for its high purity. It does not release byproducts during the curing process, making it suitable for applications where product purity and minimal leachables or extractables are critical. This is particularly important in industries such as pharmaceuticals, food processing, medical devices, and semiconductor.
2. Biocompatibility: Platinum-cured silicone rubber is biocompatible and non-toxic, making it suitable for use in medical and healthcare applications, including medical devices and pharmaceutical manufacturing.
3. Low Extractables: Due to its purity, platinum-cured silicone has low levels of extractables, which means it is less likely to release substances into the surrounding environment or fluids it comes into contact with. This property is essential in industries where contamination must be minimized.
4. High Temperature Resistance: Silicone rubber, in general, has good temperature resistance, and platinum-cured silicone is no exception. It can withstand a wide range of temperatures, from very low to moderately high, depending on the specific formulation.
5. Excellent Elasticity and Flexibility: Silicone rubber is known for its excellent elasticity and flexibility, which make it effective as a sealing material, even in applications with frequent movement or compression.
6. Chemical Resistance: Platinum-cured silicone rubber has good resistance to various chemicals, making it suitable for use in industries where exposure to chemicals is a concern.
7. FDA Compliance: Platinum-cured silicone rubber can meet FDA (U.S. Food and Drug Administration) requirements, making it suitable for food and beverage applications.
It's important to note that while platinum-cured silicone O-rings offer many advantages, they may be more expensive than peroxide-cured silicone O-rings due to the cost of the platinum catalyst and the complexity of the manufacturing process. The choice between platinum-cured and peroxide-cured silicone O-rings depends on the specific requirements of the application, with platinum-cured silicone being favored in applications where purity, biocompatibility, and low extractables are critical.
What is a very high temperature O-ring?
The choice of the best O-ring material for high-temperature applications depends on the specific temperature range and other environmental factors involved. Several elastomer materials are suitable for high-temperature sealing, and the selection should be based on the following considerations:
1. Silicone Rubber (VMQ):
- Temperature Range: Certain Silicone rubber blends can handle temperatures up to 600°F (315°C), however most are only rated for 400°F (205°C).
- Advantages: Excellent high-temperature resistance, good flexibility, and resistance to ozone and UV exposure.
- Applications: Suitable for a wide range of high-temperature applications, including aerospace, automotive, and food processing.
2. Fluorocarbon Rubber (FKM/Viton):
- Temperature Range: FKM can withstand temperatures up to 437°F (225°C).
- Advantages: Exceptional chemical resistance, high-temperature resistance, and durability.
- Applications: Commonly used in oil and gas, automotive, chemical processing, and aerospace industries.
3. Perfluoroelastomer (FFKM):
- Temperature Range: Certain FFKM CanRez blends can handle temperatures up to 635°F (335°C) and excursions to even higher temperatures.
- Advantages: Excellent high-temperature and ultimate chemical resistance, low outgassing, and low permeability.
- Applications: Used in demanding high-temperature and chemical environments, such as semiconductor manufacturing and oil and gas.
4. Fluorosilicone (FVMQ):
- Temperature Range: FVMQ materials can handle temperatures up to 356°F (180°C).
- Advantages: Good high-temperature resistance, flexibility, and resistance to oils and fuels.
- Applications: Suitable for aerospace, automotive, and other applications where a combination of temperature and chemical resistance is required.
The best O-ring material for high-temperature applications varies depending on the specific temperature range, chemical exposure, pressure, and other environmental factors. It's essential to consult with a material expert or O-ring manufacturer to select the most suitable material for your particular application to ensure optimal performance and longevity. Additionally, consider the specific grade and formulation of the elastomer material to match the requirements of your high-temperature application.
What is the best O-ring material for high temperatures?
The choice of the best O-ring material for high-temperature applications depends on the specific temperature range and other environmental factors involved. Several elastomer materials are suitable for high-temperature sealing, and the selection should be based on the following considerations:
1. Silicone Rubber (VMQ):
- Temperature Range: Certain Silicone rubber blends can handle temperatures up to 600°F (315°C), however most are only rated for 400°F (205°C).
- Advantages: Excellent high-temperature resistance, good flexibility, and resistance to ozone and UV exposure.
- Applications: Suitable for a wide range of high-temperature applications, including aerospace, automotive, and food processing.
2. Fluorocarbon Rubber (FKM/Viton):
- Temperature Range: FKM can withstand temperatures up to 437°F (225°C).
- Advantages: Exceptional chemical resistance, high-temperature resistance, and durability.
- Applications: Commonly used in oil and gas, automotive, chemical processing, and aerospace industries.
3. Perfluoroelastomer (FFKM):
- Temperature Range: Certain FFKM CanRez blends can handle temperatures up to 635°F (335°C) and excursions to even higher temperatures.
- Advantages: Excellent high-temperature and ultimate chemical resistance, low outgassing, and low permeability.
- Applications: Used in demanding high-temperature and chemical environments, such as semiconductor manufacturing and oil and gas.
4. Fluorosilicone (FVMQ):
- Temperature Range: FVMQ materials can handle temperatures up to 356°F (180°C).
- Advantages: Good high-temperature resistance, flexibility, and resistance to oils and fuels.
- Applications: Suitable for aerospace, automotive, and other applications where a combination of temperature and chemical resistance is required.
The best O-ring material for high-temperature applications varies depending on the specific temperature range, chemical exposure, pressure, and other environmental factors. It's essential to consult with a material expert or O-ring manufacturer to select the most suitable material for your particular application to ensure optimal performance and longevity. Additionally, consider the specific grade and formulation of the elastomer material to match the requirements of your high-temperature application.
What is the difference between silicone and fluorosilicone O-rings?
Silicone and fluorosilicone O-rings are both elastomeric sealing materials, but they have different chemical compositions and properties that make them suitable for different applications. Here's a comparison of their key characteristics:
Silicone O-Rings:
1. Composition: Silicone O-rings are made from silicone rubber, which is a polymer composed of silicon, oxygen, carbon, and hydrogen atoms. The unique chemical structure of silicone gives it its characteristic flexibility and heat resistance.
2. Temperature Range: Silicone O-rings have a broad temperature range and can withstand temperatures from approximately -100°F to 600°F (-75°C to 315°C) depending on the blend. They are excellent for high-temperature applications.
3. Chemical Resistance: Silicone has good resistance to water, steam, and many chemicals. However, it is not recommended for use with petroleum-based products, fuels, and certain solvents.
4. Elasticity: Silicone O-rings are known for their flexibility and elasticity, making them suitable for dynamic sealing applications.
5. Electrical Insulation: Silicone is an excellent electrical insulator and is used in electrical and electronic applications.
Fluorosilicone O-Rings:
1. Composition: Fluorosilicone O-rings are made from fluorosilicone rubber, which is a modified form of silicone rubber. It contains fluorine atoms in addition to silicon, oxygen, carbon, and hydrogen atoms. This modification enhances its resistance to oils and fuels.
2. Temperature Range: Fluorosilicone O-rings have a temperature range similar to standard silicone, typically from -100°F to 356°F (-75°C to 180°C). While they can withstand high temperatures, they are not as heat-resistant as some other elastomers.
3. Chemical Resistance: Fluorosilicone offers improved resistance to petroleum-based products, including oils, fuels, and solvents, compared to standard silicone. It is particularly suitable for applications where exposure to these substances is a concern.
4. Elasticity: Fluorosilicone maintains the flexibility and elasticity characteristic of silicone rubber, making it suitable for dynamic sealing applications.
5. Fuel and Oil Resistance: The primary advantage of fluorosilicone over standard silicone is its enhanced resistance to oils and fuels, which is valuable in automotive and aerospace applications.
Summary:
- Silicone O-rings: Suitable for high-temperature applications and where exposure to water and steam is a concern. Not recommended for use with petroleum-based products.
- Fluorosilicone O-rings: Ideal for applications requiring resistance to oils, fuels, and solvents, while still maintaining flexibility. They have a broader range of chemical resistance compared to standard silicone.
The choice between silicone and fluorosilicone O-rings should be based on the specific requirements of the application, particularly in terms of temperature, exposure to oils or fuels, and chemical compatibility.
What is the difference between silicone and platinum silicone?
The difference between regular silicone and platinum silicone primarily lies in their respective curing processes and the resulting properties:
1. Curing Process:
- Regular Silicone: This type of silicone is typically cured using a process that involves peroxides. Peroxide curing is an older method and is less expensive. However, it can leave behind byproducts in the silicone material, which may not be suitable for certain applications, particularly where purity is essential.
- Platinum Silicone: Platinum-cured silicone uses a platinum catalyst for curing. This process is more advanced and results in a purer product, as it doesn't leave behind any byproducts. This feature makes platinum silicone particularly valuable in medical, food, and skin-contact applications.
2. Physical Properties:
- Regular Silicone: Though it varies based on formulation, regular silicone might have slightly different physical properties compared to its platinum counterpart. For example, it might have slightly different elasticity or tensile strength.
- Platinum Silicone: Platinum silicone generally has superior physical properties, including better thermal stability, increased tensile strength, and enhanced durability. It's also often more transparent and has better biocompatibility.
3. Biocompatibility and Safety:
- Regular Silicone: The byproducts left from peroxide curing can lead to issues in applications where purity is critical. For example, it might not be suitable for long-term medical implants or in food-grade applications.
- Platinum Silicone: Due to its purity and lack of byproducts, platinum silicone is often preferred in medical applications, food-grade products, and baby products. It's considered safer and more inert in these contexts.
4. Cost:
- Regular silicone is generally less expensive than platinum silicone, making it a more cost-effective choice for applications where the superior properties of platinum silicone are not necessary.
In summary, while both regular and platinum silicone have similar basic chemical compositions, platinum silicone's curing process results in a purer, more stable product with better physical properties and higher biocompatibility. This makes it more suitable for high-end, sensitive applications, especially in the medical, food, and baby product industries. Regular silicone, being more cost-effective, is still widely used in a variety of industrial and consumer applications where the specific advantages of platinum silicone are not required.
What is the most common type of O-ring?
The most common type of O-ring material used is Nitrile rubber, often referred to as NBR (Nitrile Butadiene Rubber) O-rings. NBR O-rings are widely used in various industries and applications due to their versatile properties and cost-effectiveness. Here are some reasons why NBR O-rings are commonly used:
1. Oil and Fuel Resistance: NBR O-rings exhibit excellent resistance to oils, fuels, and lubricants, making them ideal for sealing applications in automotive, machinery, and hydraulic systems.
2. Chemical Compatibility: NBR is compatible with a wide range of non-polar and polar chemicals, which makes it suitable for many industrial applications.
3. Temperature Range: NBR O-rings can perform effectively within a moderate temperature range, typically from -40°C (-40°F) to 125°C (257°F).
4. Cost-Effectiveness: NBR is relatively inexpensive compared to some other elastomer materials, making it a cost-effective choice for sealing solutions.
5. Availability: NBR O-rings are readily available in various sizes, shapes, and durometers, making them easy to source for a wide range of applications.
While NBR is the most common type of O-ring material, it's important to note that O-rings are available in a variety of materials, each with its own set of properties and suitability for specific applications. Depending on the requirements of the application, other types of O-ring materials, such as Viton (FKM), EPDM, silicone, and HNBR, may also be used to meet specific performance criteria such as temperature resistance, chemical compatibility, or durability. The choice of O-ring material should be based on the specific needs of the sealing application.
What type of silicone is used for O-rings?
Silicone rubber O-rings are typically made from various types of silicone elastomers. The specific type of silicone used for O-rings can vary based on the application requirements, temperature range, and performance characteristics needed. Some common types of silicone elastomers used for O-rings include:
1. VMQ Silicone (Polydimethylsiloxane): VMQ silicone is the most common type of silicone rubber used for O-rings. It offers good flexibility, high and low-temperature resistance, and excellent electrical insulation properties. VMQ silicone is suitable for a wide range of applications, including sealing, gasketing, and insulation.
2. Fluorosilicone Rubber (FVMQ): Fluorosilicone rubber is a modified silicone elastomer that contains fluorine atoms in its chemical structure. This modification enhances its resistance to fuels, oils, and solvents, making it suitable for applications where exposure to these substances is common. FVMQ O-rings are often used in aerospace and automotive applications.
3. Phenyl Silicone Rubber (PVMQ): Phenyl silicone rubber contains phenyl groups in its chemical structure, which provide improved resistance to low temperatures compared to standard VMQ silicone. PVMQ O-rings are used in applications requiring low-temperature stability.
4. Liquid Silicone Rubber (LSR): Liquid silicone rubber is a versatile silicone elastomer that can be injection molded to produce O-rings and other complex shapes. LSR O-rings offer good flexibility, durability, and resistance to extreme temperatures. They are often used in medical devices, food processing, and other industries where biocompatibility and high-temperature resistance are important.
5. Electrically Conductive Silicone: In some specialized applications, silicone rubber O-rings are formulated to be electrically conductive, providing EMI (electromagnetic interference) shielding or grounding properties.
The choice of silicone type for O-rings depends on the specific requirements of the application, including temperature range, chemical exposure, and performance expectations. It's important to consult with O-ring manufacturers or suppliers to select the most suitable silicone elastomer for your specific needs.